トリマーの兄貴分ともいえる、“ルーター”。
ルーター1台あれば熟練の技が必要な加工も可能になります。
しかし実際どんな加工が出来るの?トリマーとの違いは? と思いますよね。
そこで今回は電動工具 “ルーター” の使い方と構造について詳しく説明します。
ルーターとは?
各部名称
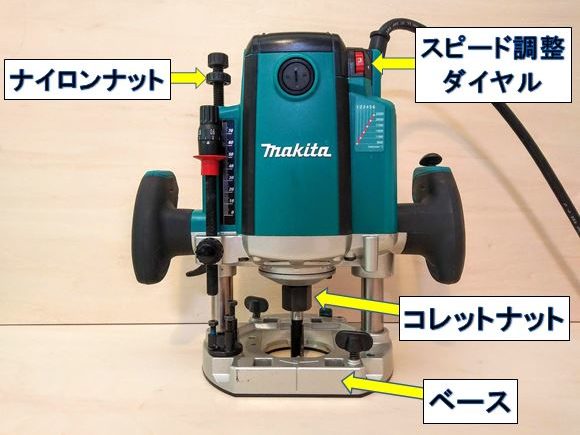
ルーター内側
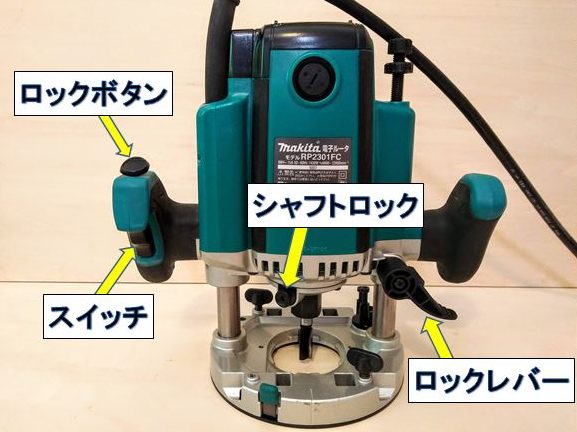
ルーター外側
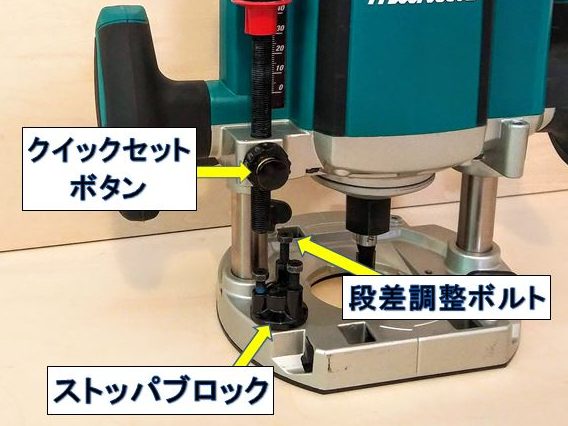
内側詳細
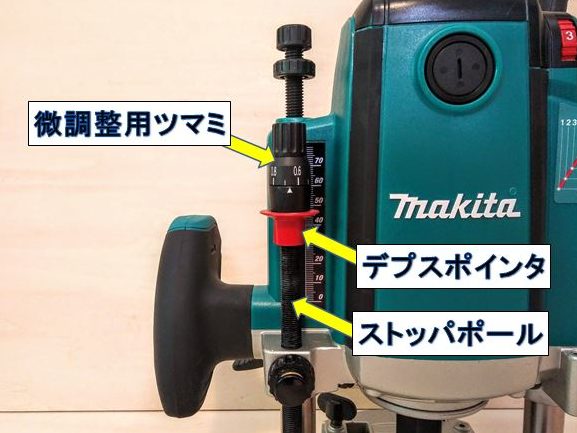
内側詳細
ルーターとは、高速回転(毎分9000~27000回転)する先端ビット(先端の刃)によって、様々な切削加工が出来る電動工具です。
面取り加工・溝掘り加工・ならい加工・円加工など様々な加工が可能です。
先端ビットの回転速度はトリマー(毎分25000~35000回転)に劣りますが、出力はトリマーの3倍ほどあり使用する先端ビットも太く大きいので、よりパワフルな切削が出来ます。
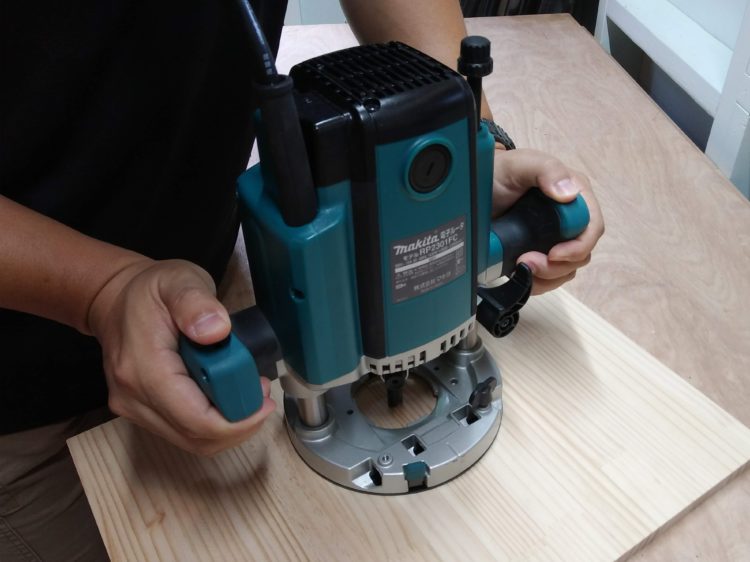
両手でハンドルを握る
トリマーは軽量なので片手で操作しますが、ルーターは重量があるため両手でハンドルを握り操作します。
(専用のテーブルにルーターを固定し、材料を動かし加工することも多いです。➩ ルーターテーブルの構造と使い方 参照)
今回はマキタ製のルーター、“RP2301FC” を使用して構造と使い方について説明します。
ビットの脱着
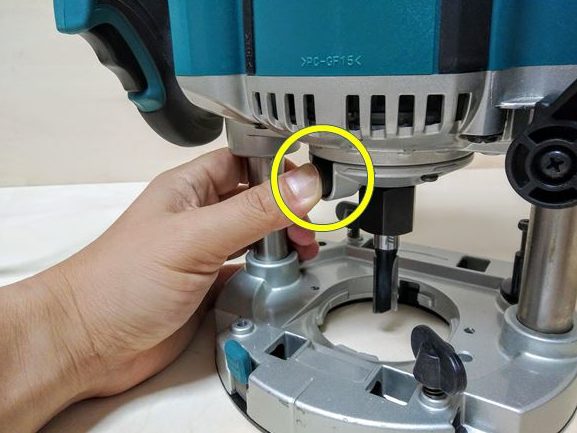
シャフトロックを押し込む
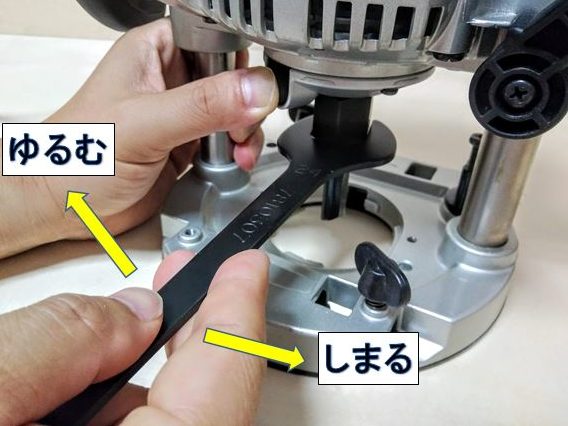
スパナでコレットナットを締め付け
ビットの脱着は必ず電源コードを抜いてから行います。(誤作動による事故を防ぐ為)
シャフトロックを押し込んで、シャフト(回転軸)が回らないように固定します。
付属のスパナ(24mm)をコレットナットに差し込んで、ビットの取り付け時(コレットナットを締める)は右回りに、取り外す時(コレットナットを緩める)は左回りにコレットナットをまわします。
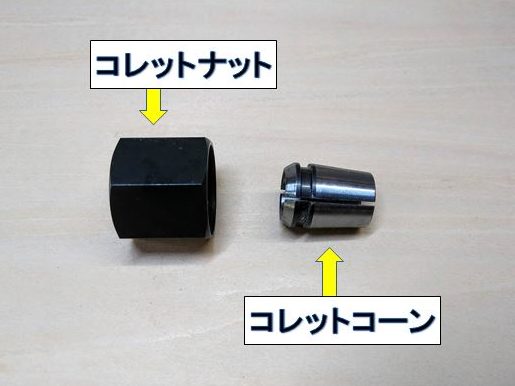
コレットナットとコレットコーン
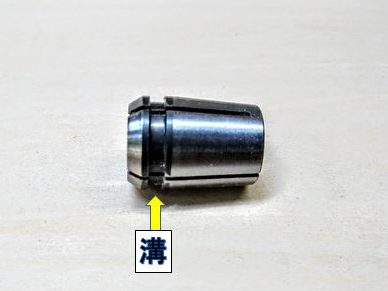
コレットコーンの溝
ビットを締め付け固定する部分は、コレットナットとコレットコーンの2つの部品で構成されています。
コレットコーンには溝があります。
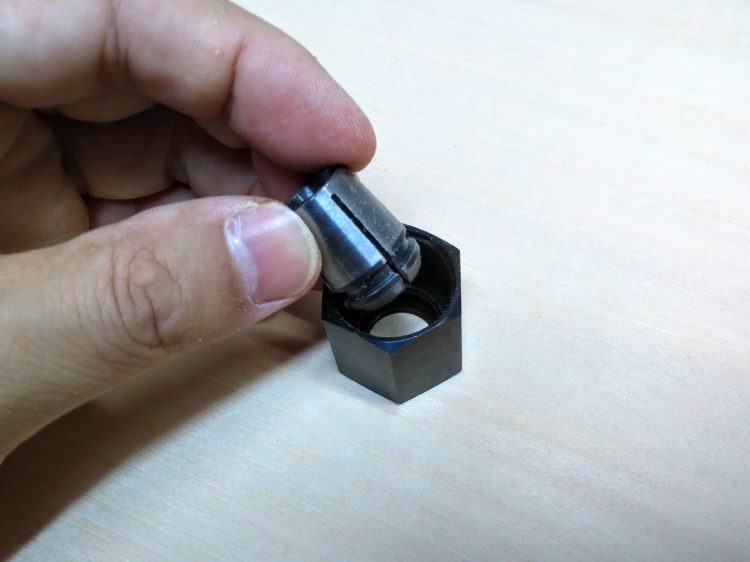
コレットコーンを差し込む
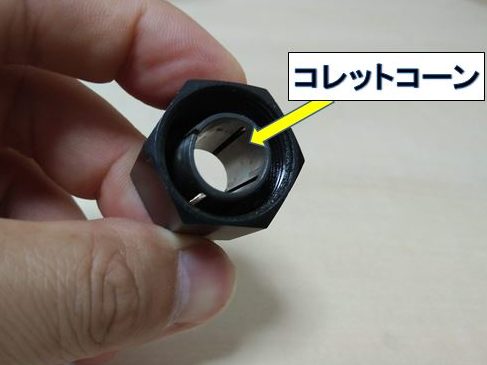
コレットコーン
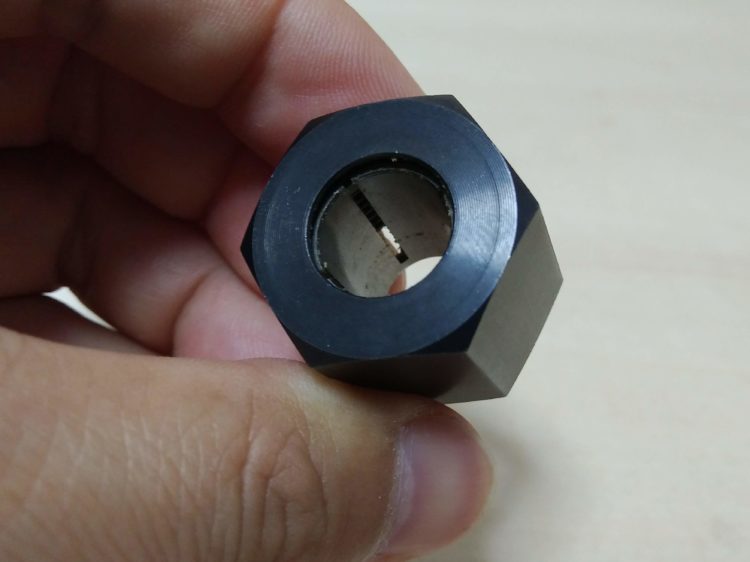
コレットナット表側
コレットコーンをコレットナットに差し込むと、コレットコーンの溝がナット内部にはまる構造になっていて、コレットコーン・コレットナットが一体化します。
ビットを取り付けずコレットナットを締め付けると、コレットコーンが破損するので、必ずビットを差し込んでから締め付けを行って下さい。
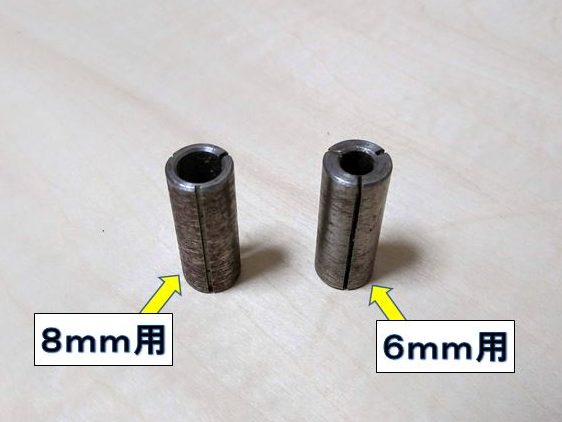
コレットスリーブ
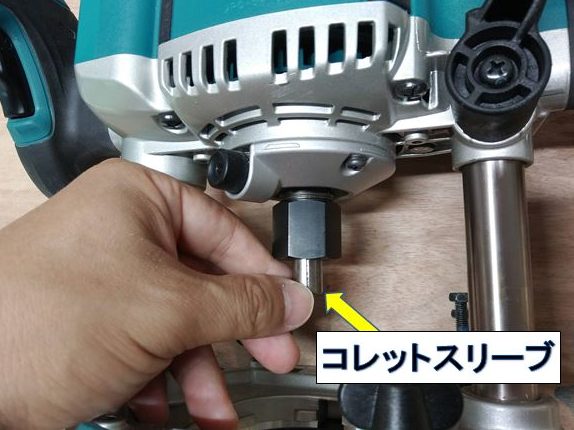
コレットスリーブをチャック孔に差し込む
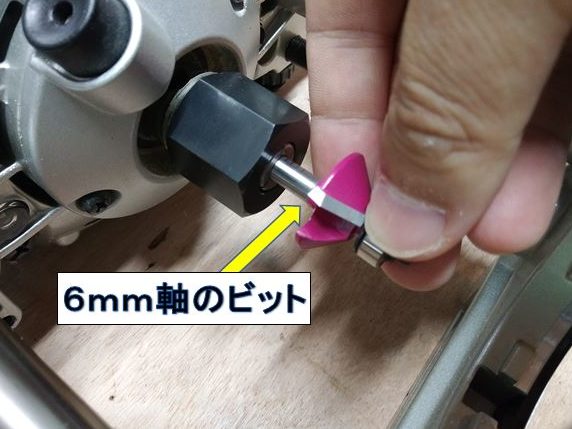
6mm軸のビットを取り付け
基本的にルーターのビット軸径は12mmですが、コレットスリーブ(6mm用・8mm用)をチャック孔に差し込むと、軸径6mm・8mmのビットを使用する事が出来ます。
切削の深さ調整
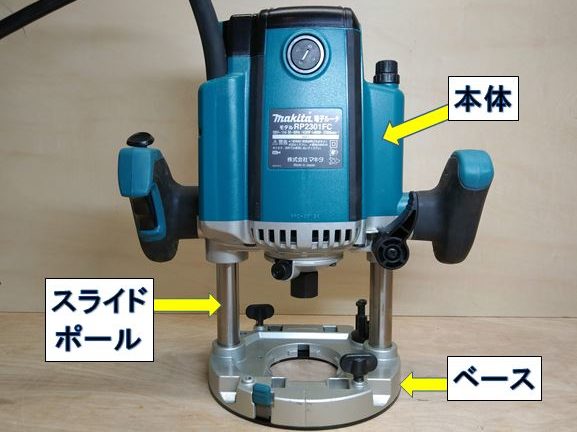
本体が上がっている状態

本体が下がっている状態
ルーターは本体とベースがスライドポールで繋がっています。
本体は常にバネの力により持ち上げられた状態になっています。
切削は本体を押し下げて行います。
押し下げる量を設定する事により、切削の深さを調整する仕組みです。
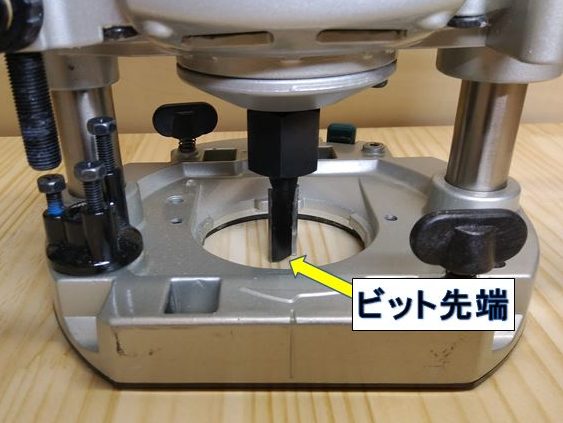
ビット先端が部材に当たる
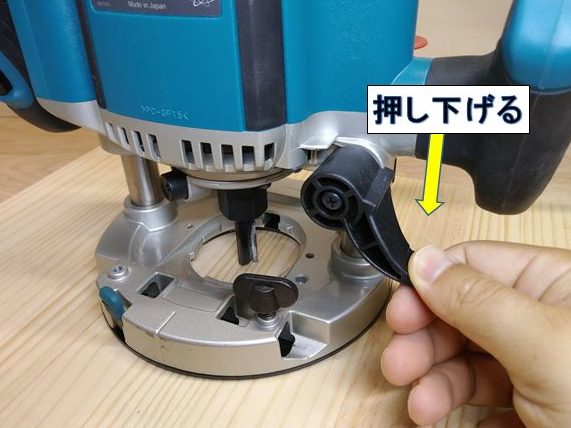
ロックレバーを押し下げる
ビット先端が部材に当たる(ベース裏面と同一面上)位置まで本体を押し下げます。
本体を押し下げた位置でロックレバーを押し下げ、固定します。
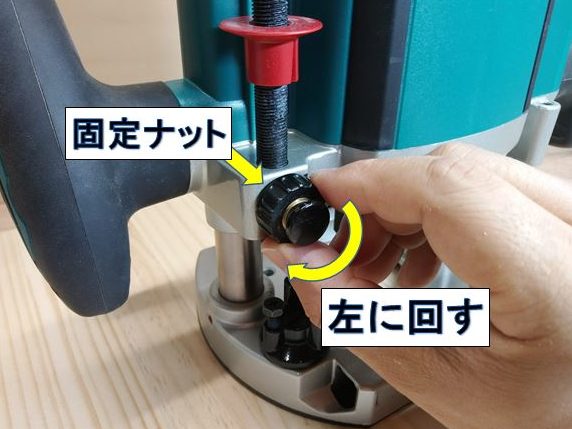
ストッパポール固定ナットを緩める
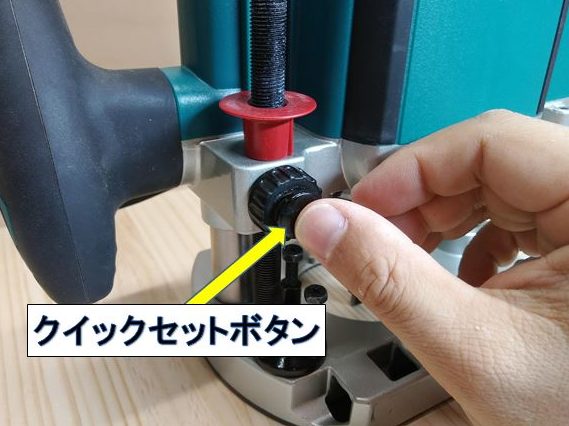
クイックセットボタンを押す
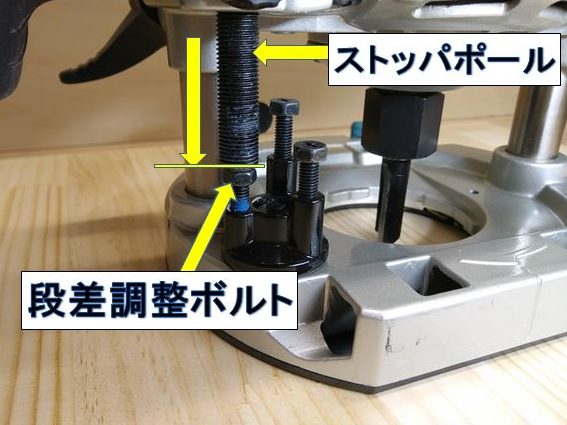
ストッパポールを下げる
ストッパポール固定ナットを左に回し緩めます。
クイックセットボタンを押しながら、ストッパポールを段差調整ボルトに当たるまで下げます。
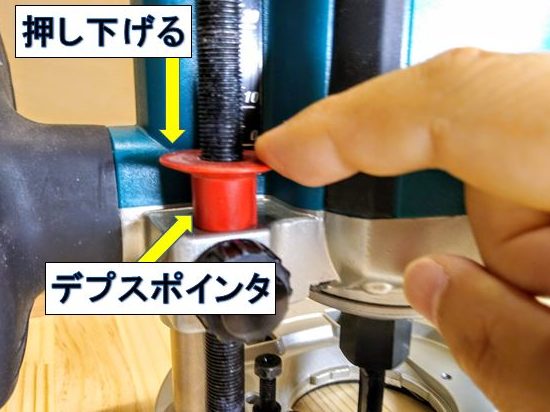
デプスポインタを押し下げる
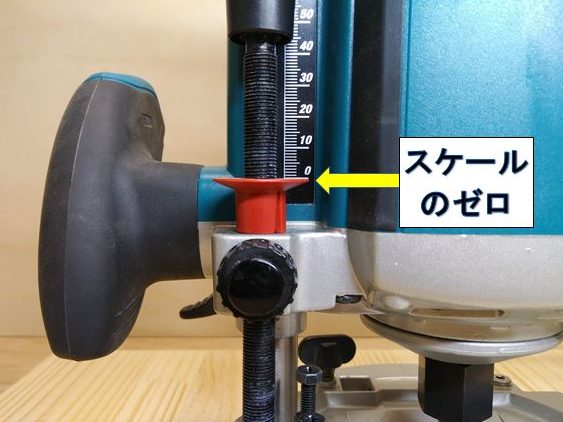
デプスポインタをスケールのゼロに合わせる
デプスポインタを一番下まで押し下げます。
デプスポインタの上端が本体に記されているスケールの0(ゼロ)に合います。
デプスポインタの上端が指し示すスケールの数値が実際の切削深さになります。
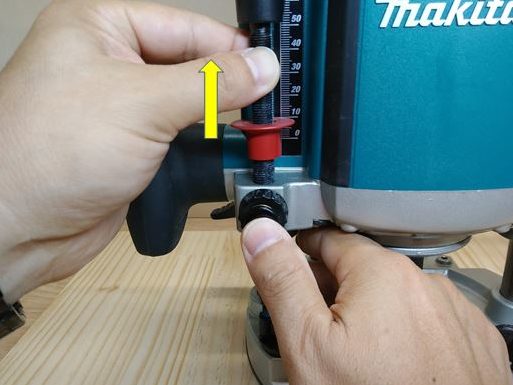
ストッパポールを押し上げる
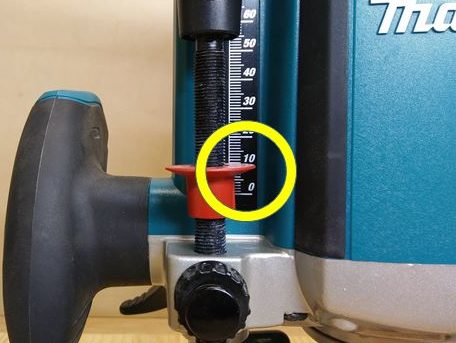
実際の切削深さ=スケールの値
切削深さを設定します。
クイックセットボタンを押しながら、ストッパポールを押し上げます。(デプスポインタは動かさないでください。)
デプスポインタの上端を、スケールの目盛り(実際の切削深さの値と同じ)に合わせたら、クイックセットボタンから手を離します。
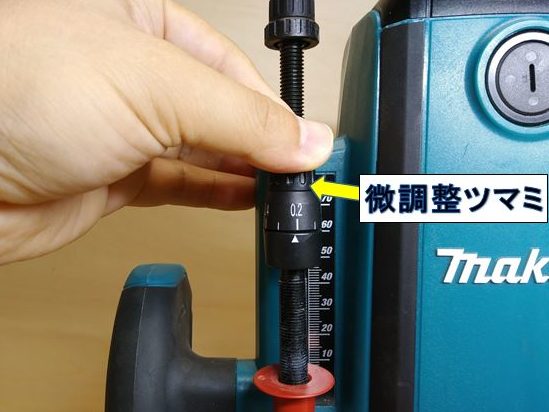
微調整ツマミを回す
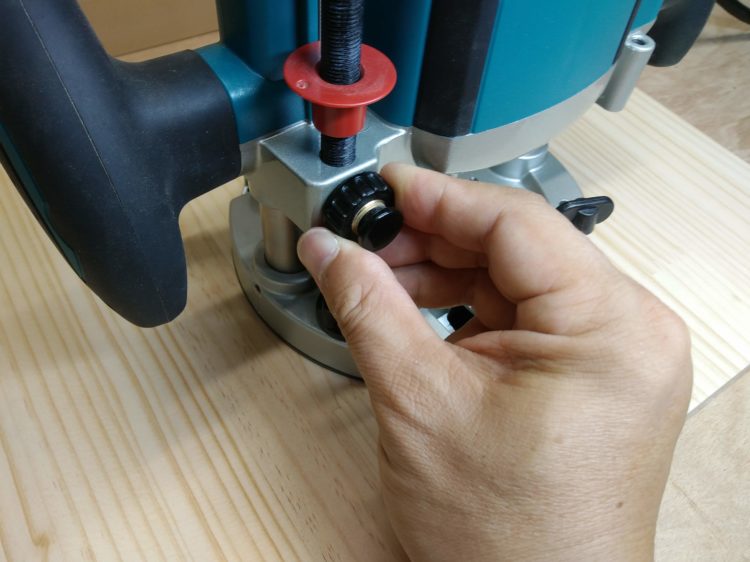
ストッパポール固定ナットを締める
切削深さの微調整は、微調整ツマミを回して調整します。
ツマミを右回りに回すと切削が深くなり、左に回すと浅くなります。(1回転させると1mm深さを変える事が出来ます。)
固定ナットを締め付けストッパポールを固定し、最終的に切削深さを設定します。
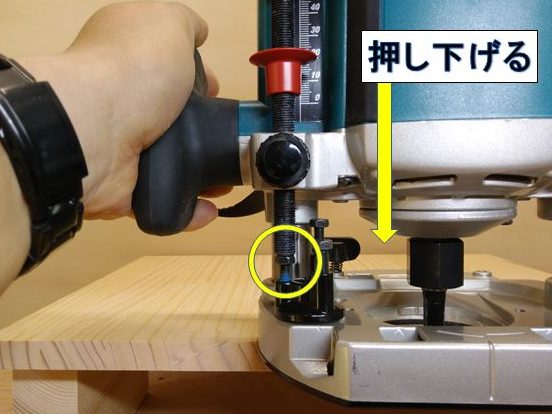
段差調整ボルトに当たるまで押し下げる
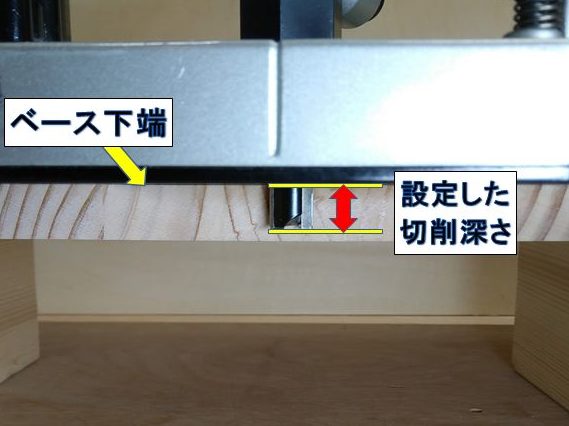
ビットの出具合
ロックレバーを解除しストッパポールを段差調整ボルトに当たるまで本体を下げると、設定した深さ分ビットが出て切削する事が出来ます。
ストッパブロック
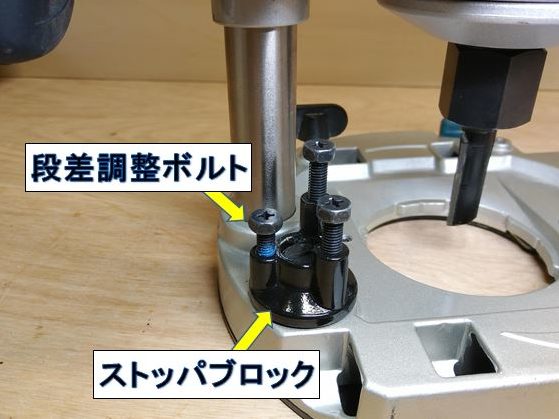
3つの段差調整ボルト
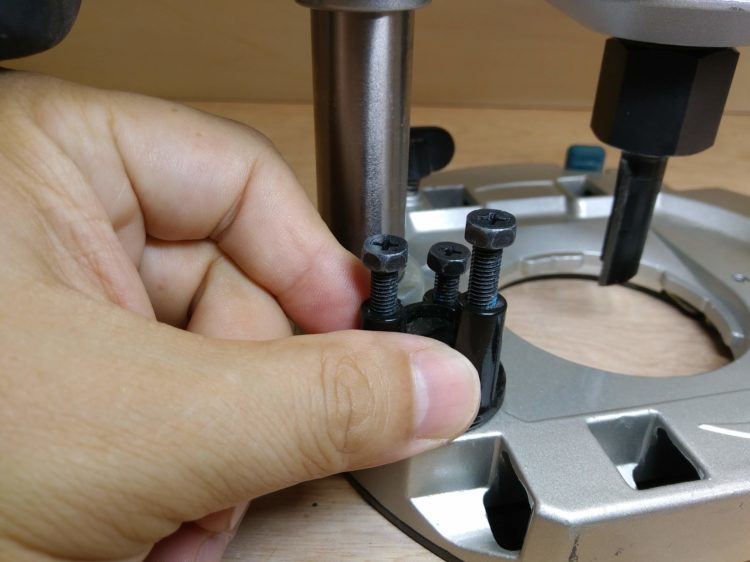
ストッパブロックを回転
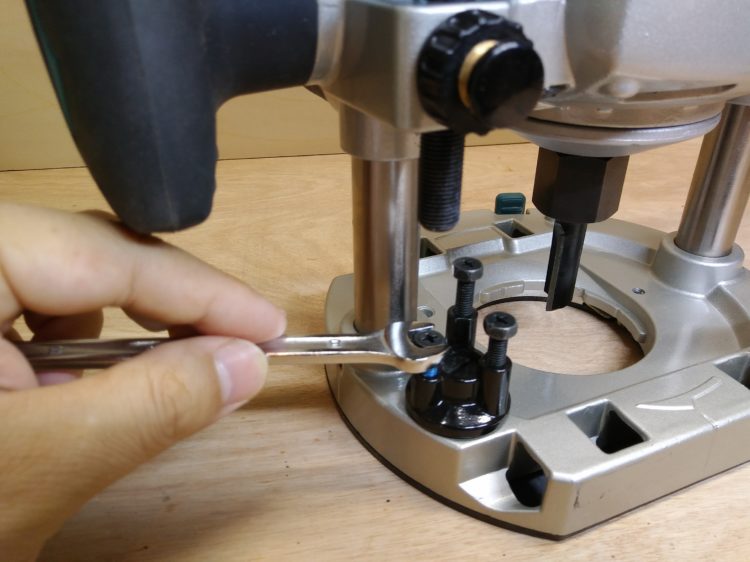
スパナで高さを調整
ストッパブロックには高さの異なる段差調整ボルトがあり、ストッパブロックを回転させることで簡単に切削の深さを変えることが出来ます。
深い溝を切削する際は、切削を何回かに分け、徐々に仕上がりの深さに溝を掘ります。
ストッパブロックの機能を利用すると、ストッパポールの設定を変えることなく、3回に分けて仕上がりの深さに溝をほる事が出来ます。
それぞれの段差調整ボルトの高さは、スパナ(8mm)やドライバーで回すと変える事が出来ます。
(ボルトを1回転すると高さが0.8mm変わります。)
ナイロンナット
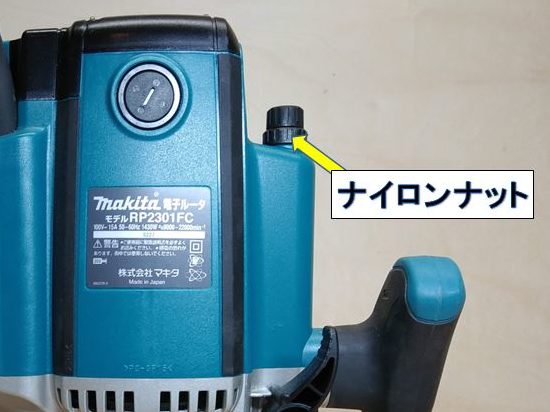
ナイロンナット
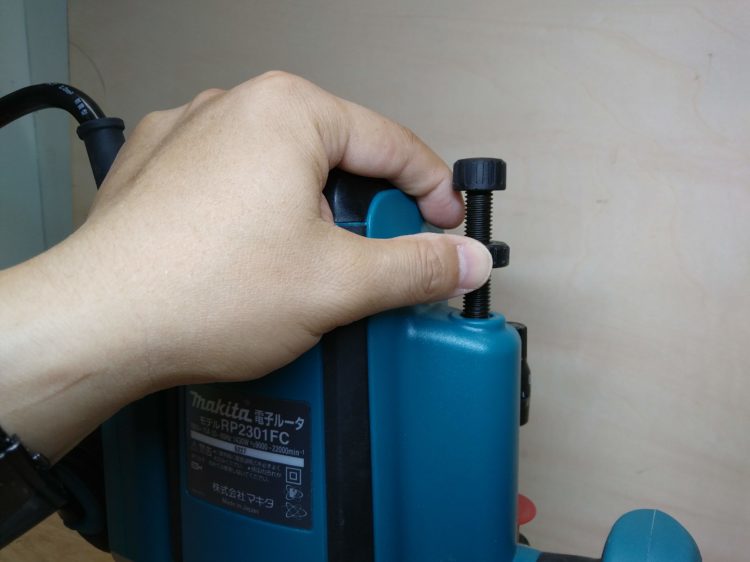
ナイロンナットを回して下げる
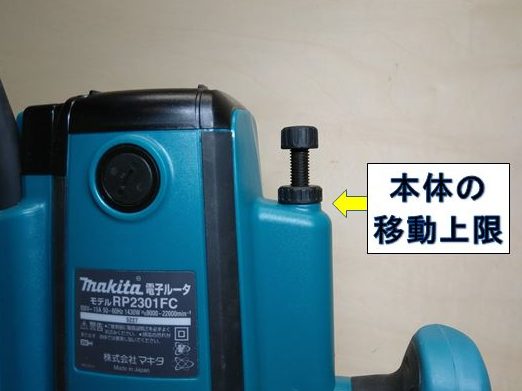
本体の移動上限
本体の上下移動は、ナイロンナットがストッパーとなり、それより上にはいかない仕組みです。
(ナイロンナットが本体の上下移動の上限となります。)
ナイロンナットを回して下げる事によって本体の上限を下げると、切削時の下限との距離が短くなり、効率のいい作業が行えます。
スイッチ操作・スピード調整ダイヤル
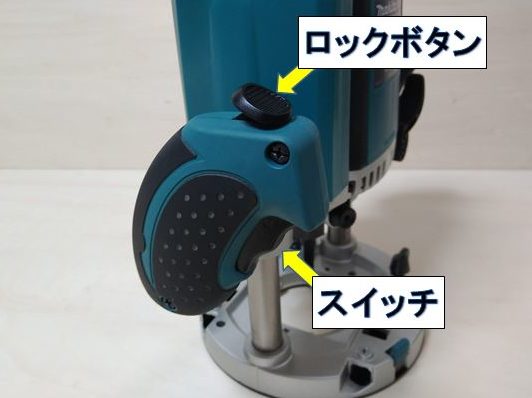
スイッチとロックボタン
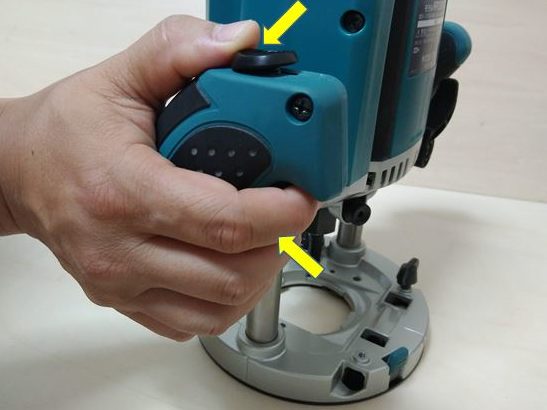
ロックボタンを押した状態でスイッチを押し込む
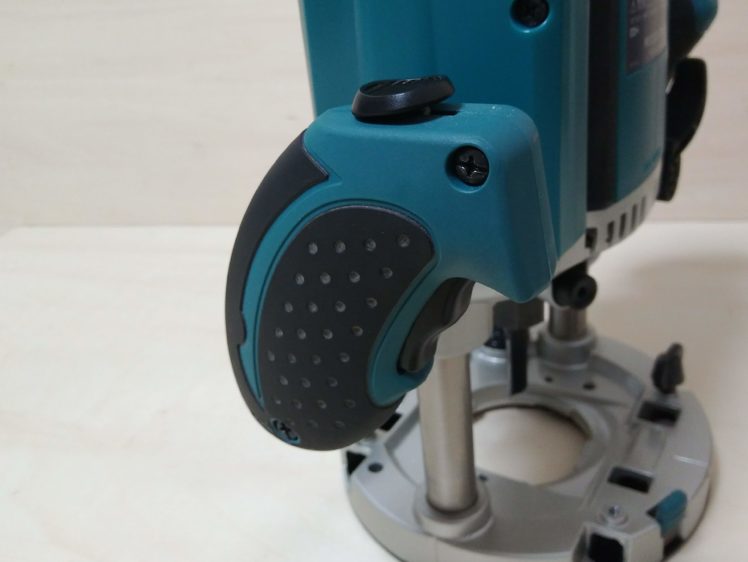
スイッチが固定(連続運転モード)
ロックボタンを押しながらスイッチをいっぱいに引くと、スイッチが入った状態で固定され、連続運転が出来ます。
スイッチを切る場合は、もう一度スイッチを引き込み、ロックボタンが戻ったらスイッチを離します。
スイッチを離すとロック機能が働き、スイッチを引くことが出来なくなります。
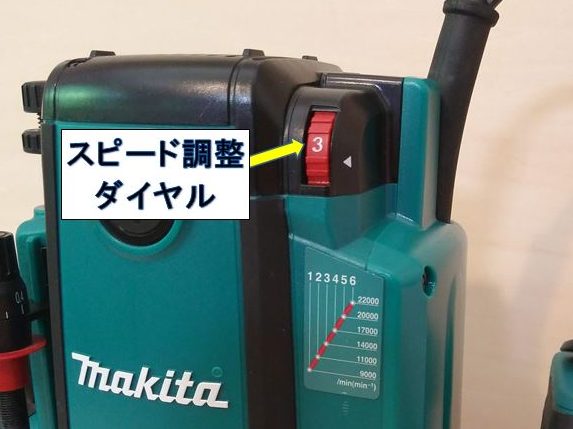
スピード調整ダイヤル
マキタのルーター、“RP2301FC” には “スピード調整ダイヤル” が付属しています。
回転数を6段階(毎分9000~22000回転の範囲内)で変える事が出来、ダイヤルを6側に回すと高速回転、1側に回すと低速回転になります。
プラスチックやアクリルなどの切削時はビットの熱で材料が融ける可能性があるので、低速回転での切削が望ましいです。
基本の操作法
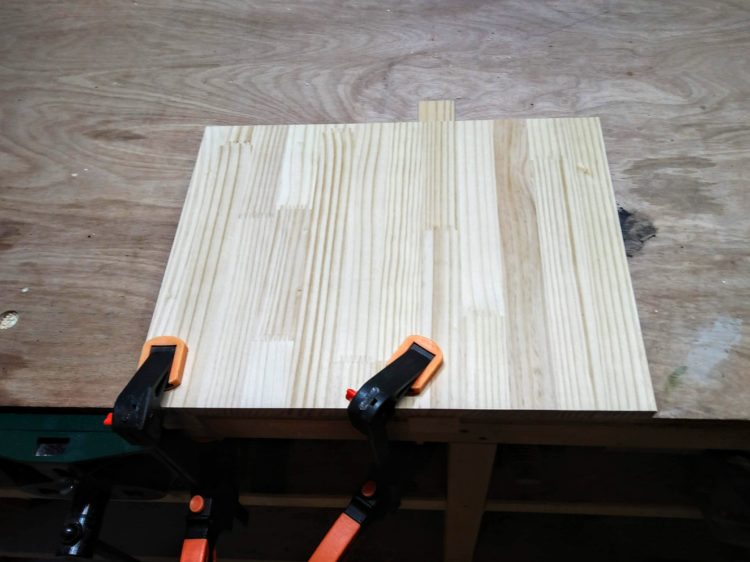
加工材をしっかりと固定する
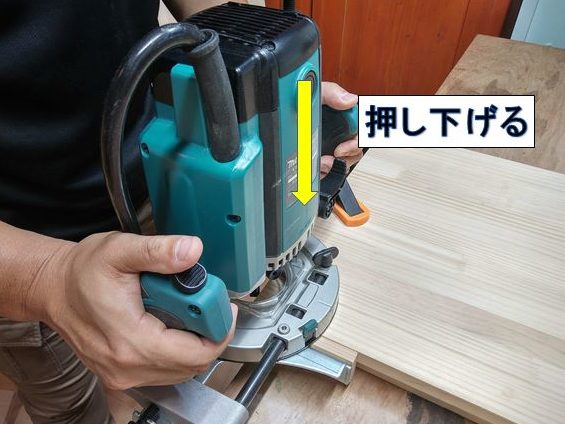
設定した深さまで本体を下げる
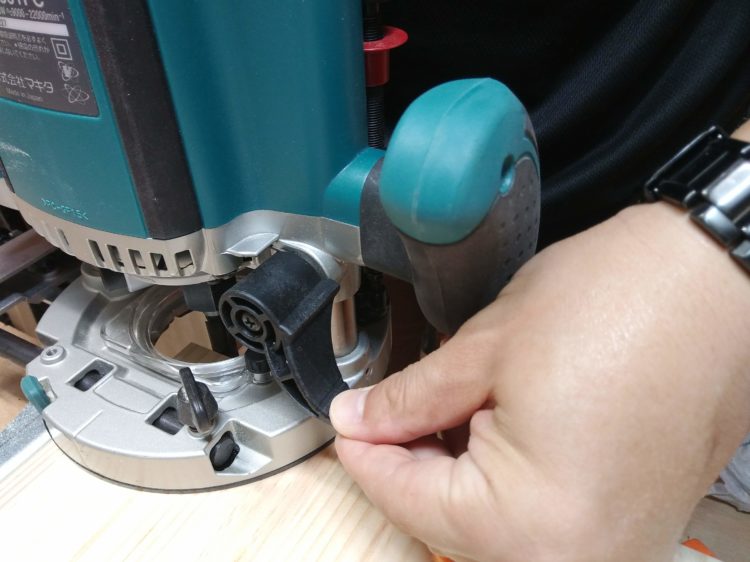
ロックレバーで固定
ルーターは作業時基本的に両手で保持するので、加工材はクランプ等でしっかり固定しておきます。
加工材の端にルーターをベース面が水平になる様に乗せ(ビットが加工材に当たらない様にしておく)、設定した深さまで本体を押し下げたら、ロックレバーで固定します。
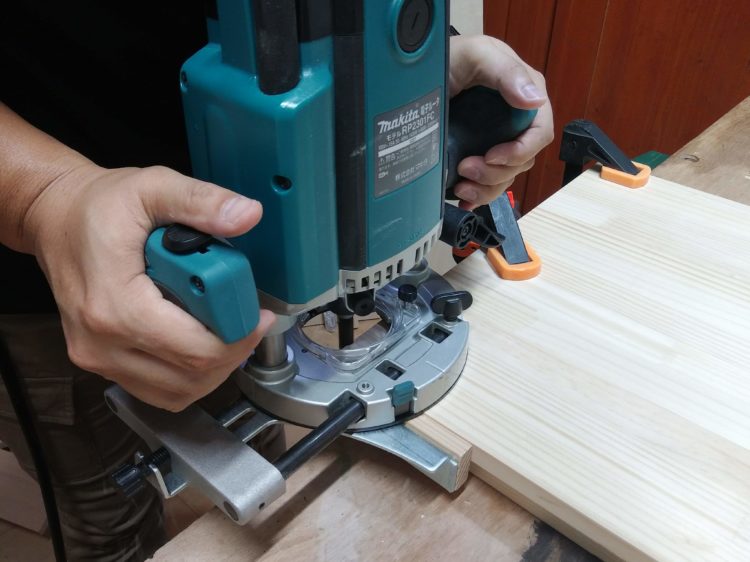
ルーターを一定速度で送る
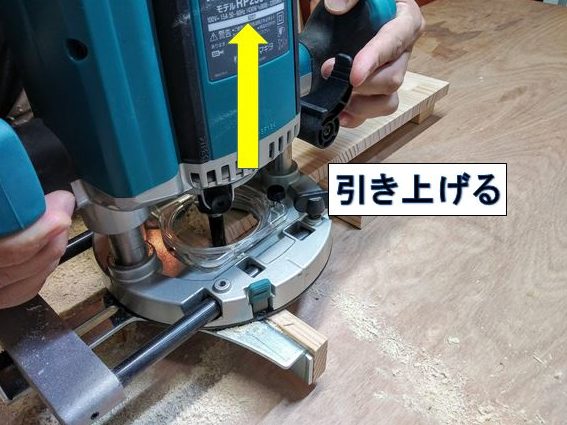
ロックレバーを解除し本体を引き上げる
ビットが加工材に当たらない場所でスイッチを入れ、ベース面・ガイドを加工材に密着させ、切削します。
ルーターは前方に(右から左の場合もあり)一定速度で送り切削します。
切削範囲を加工し終えたら、ロックレバーを解除し本体を引き上げ、スイッチを切ります。
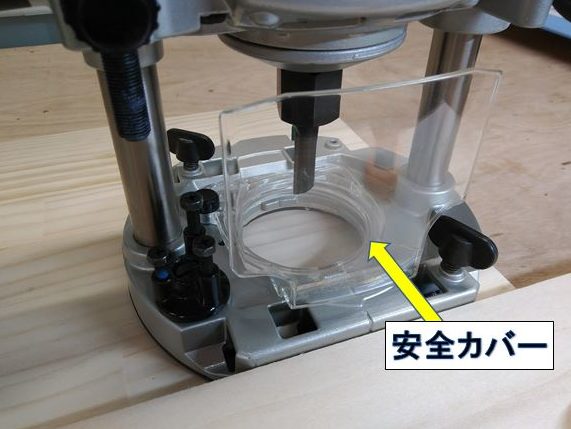
安全カバーを取り付ける
切削作業時は、切り屑が作業者の方に来ないように必ず安全カバーを取り付けます。
切削時のルーターの送り方向は、加工内容によって変わります。
これから紹介する加工法の説明か、記事終わりの “ルーターの送り方向まとめ” を参照してください。
面取り加工
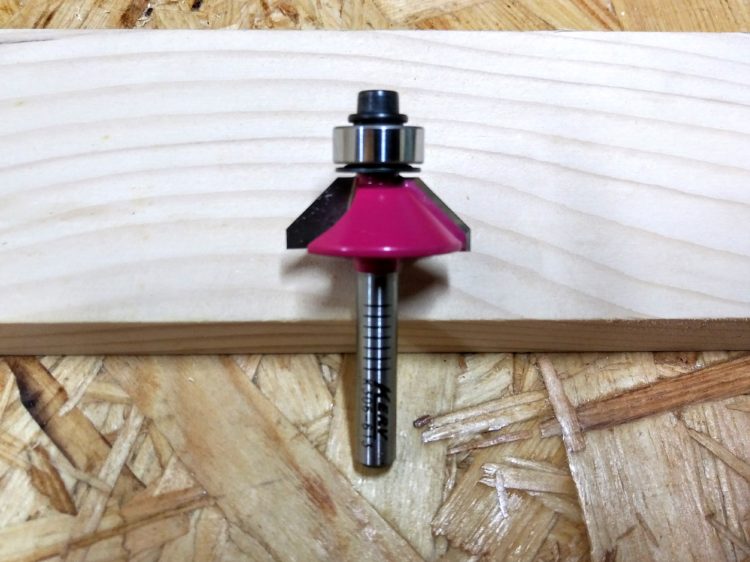
コロ付角面ビット(6mm軸
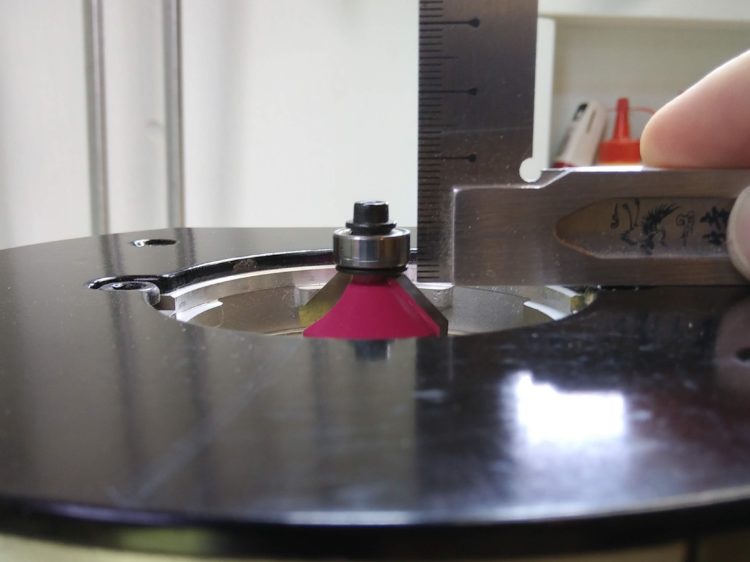
ビットの出を調整
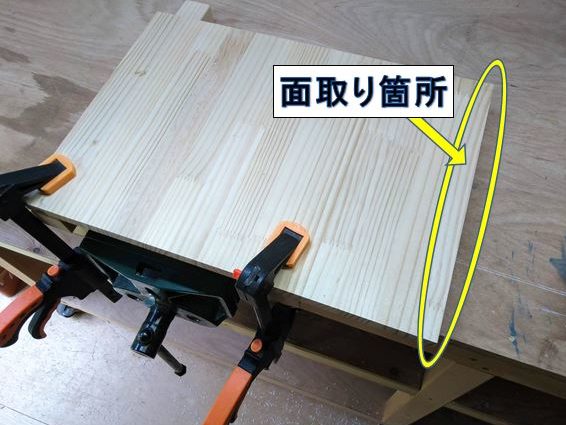
加工材を固定
コロ付角面ビット(6mm軸)を使用し、面取り加工していきます。
コレットスリーブ(6mm軸用)をチャック孔に差し込んで、ビットを取り付けます。
ビットの出の調整は通常ストッパポールを使用して行いますが、本体をひっくり返しベースを押し下げスコヤを使用して行う場合もあります。(特にコロ付ビットを使用する場合)
任意のビットの出に調整したら、ロックレバーで本体を固定します。
加工材は作業台等にしっかり固定します。
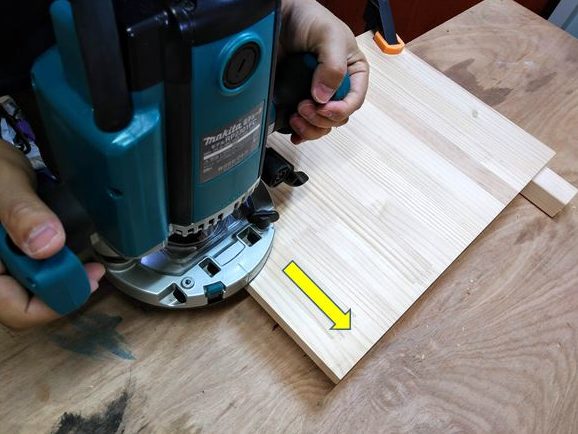
ルーター送り方向
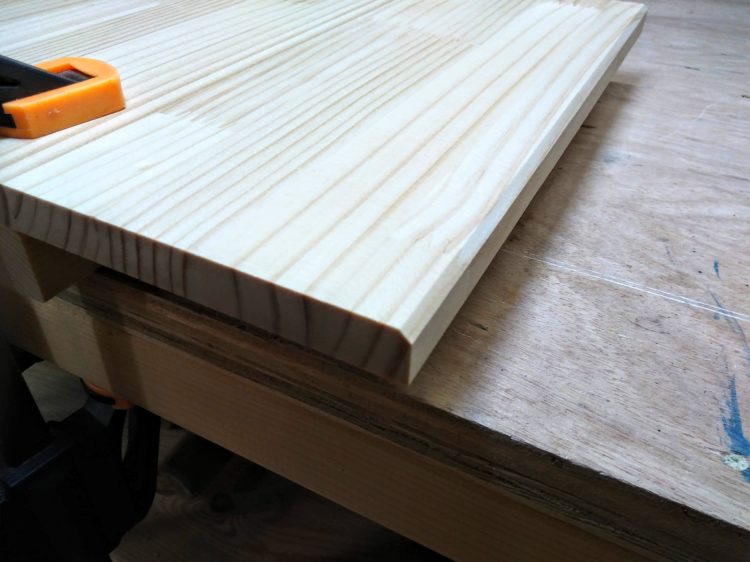
角面加工完了
加工材を左手に見ながら(ビットが加工材の右手に位置します。)ルーターを前進させ面取りしていきます。
面取り加工はルーターでも出来ますが、トリマーの方が利便性(操作性、ビットの出の調整し易さなど)が高いです。
通常の面取り加工はトリマーで行い、切削量の多くビットに負担が大きい飾り面などはルーターで行う様にするといいでしょう。
溝ほり加工
ストレートガイドによる溝ほり
ストレートガイドユニット組み立て
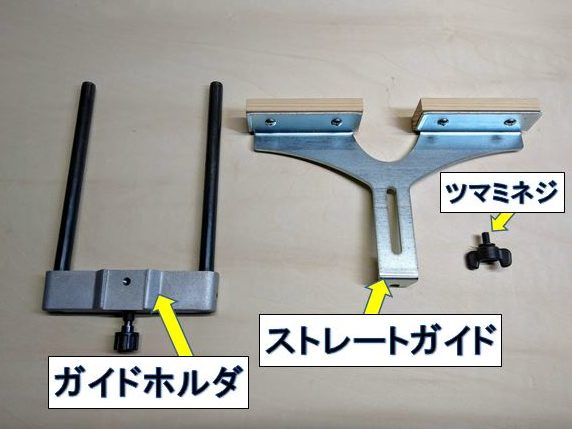
ストレートガイドユニット
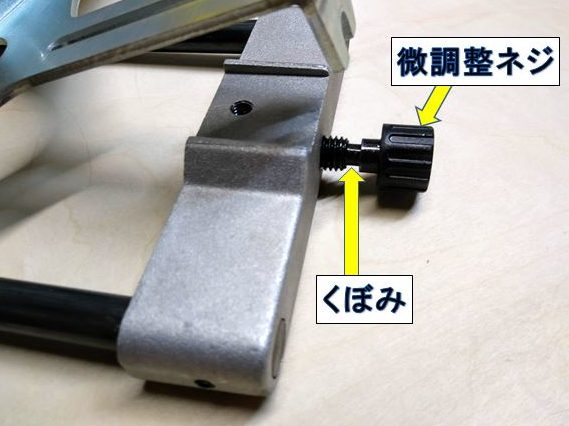
微調整ネジにストレートガイドをはめ込む
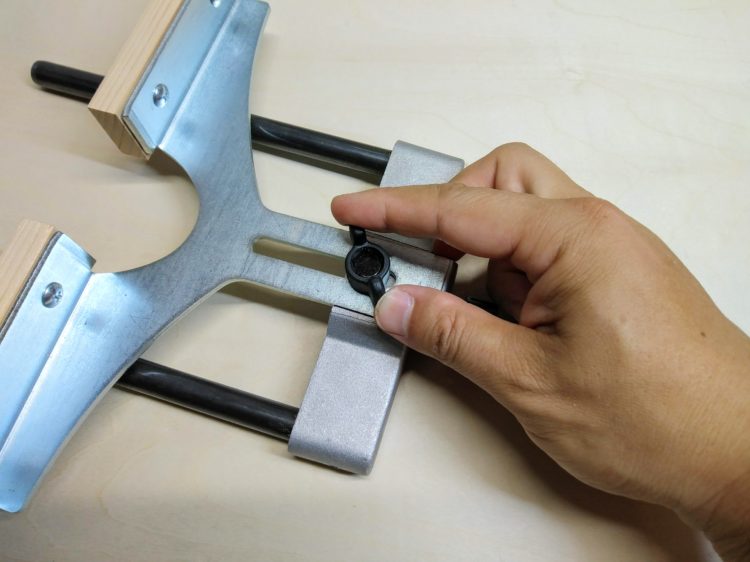
ツマミネジを締めストレートガイドを固定
付属のストレートガイドユニットを組み立てます。
ガイドホルダ・微調整ネジのくぼみにストレートガイドをはめ込みます。
ツマミネジを締め、ガイドホルダとストレートガイドを固定します。
ストレートガイドと部材の接地面には当て板を取り付けておきます。
ストレートガイド取り付け・微調整
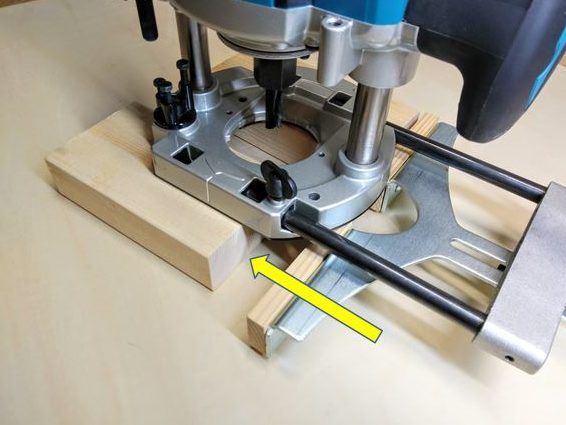
ストレートガイドを本体に取り付け
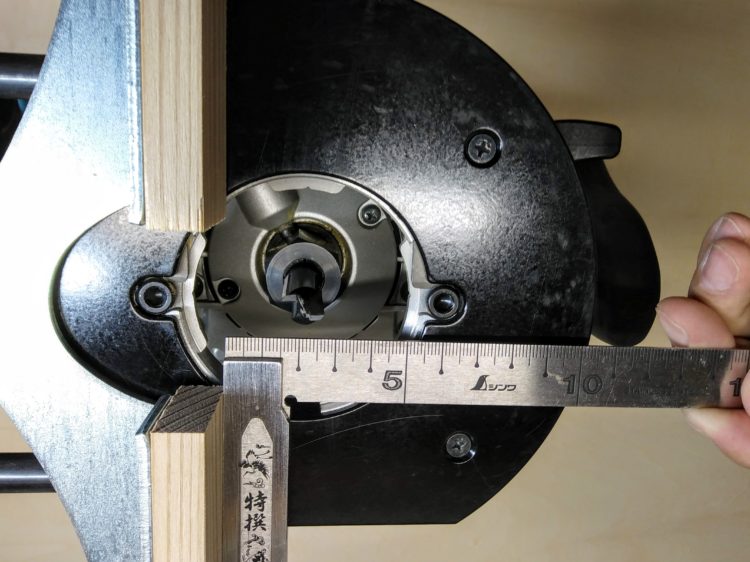
ストレートガイドとビットの間隔を調整
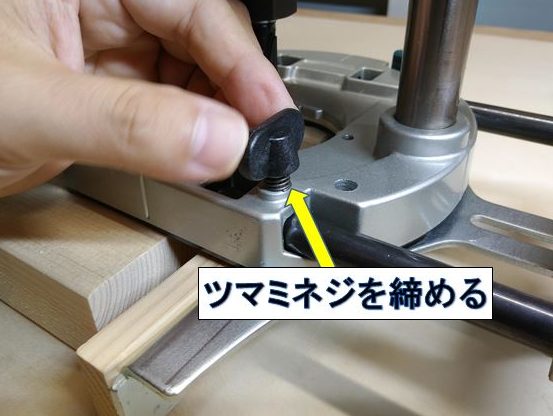
ツマミネジを締め固定
本体ベースにある取り付け穴にストレートガイドを差し込みます。
ストレートガイドとビットの間隔を任意の寸法に調整します。
本体のツマミネジ(2ヶ所)を締め付け、ストレートガイドを固定します。
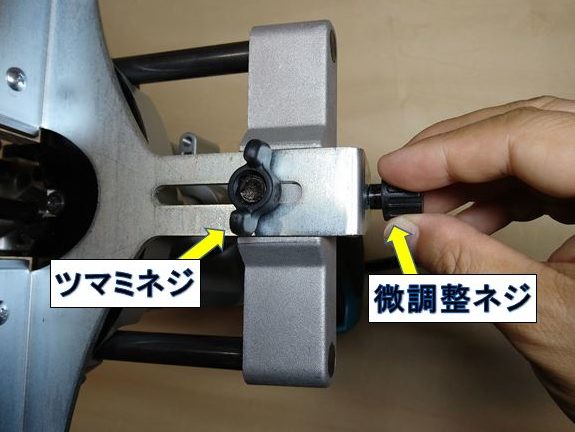
ツマミネジを緩め、微調整ネジで調整
本体にストレートガイドを固定した後に、ガイドとビットの間隔を調整する事が可能です。
ストレートガイドのツマミネジを緩め、微調整ネジを回し調整します。(ネジを1回転するとガイドを1.5mm移動出来ます。)
切削方法
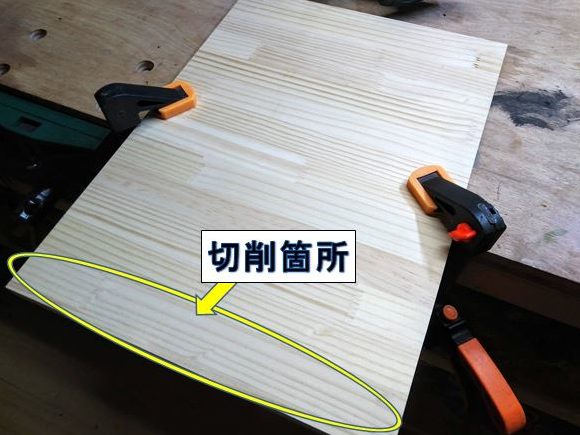
加工材を固定
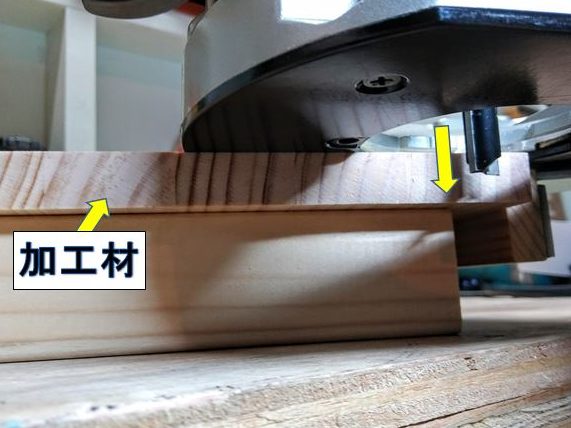
設定した深さまで本体を下げる
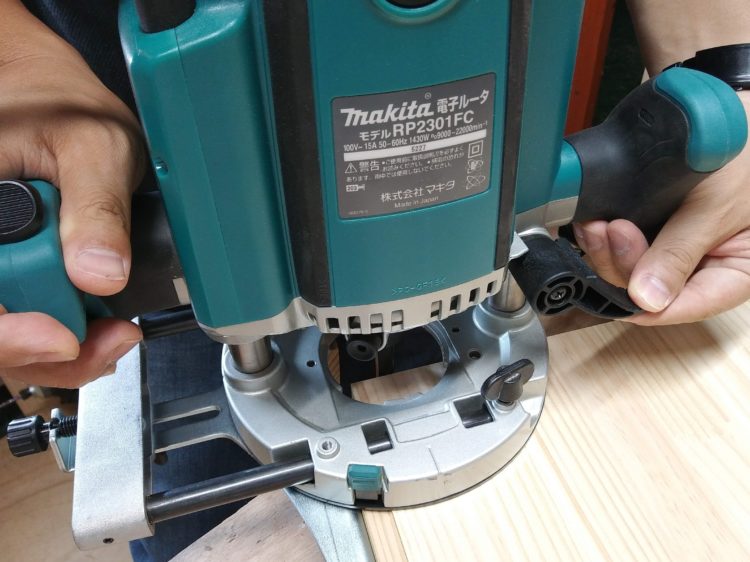
ロックレバーを下げ本体を固定
加工材を作業台等にしっかりと固定します。
ルーターのベースを加工材の端に水平にのせ、設定した切削深さまで本体を押し下げ、ロックレバーで固定します。
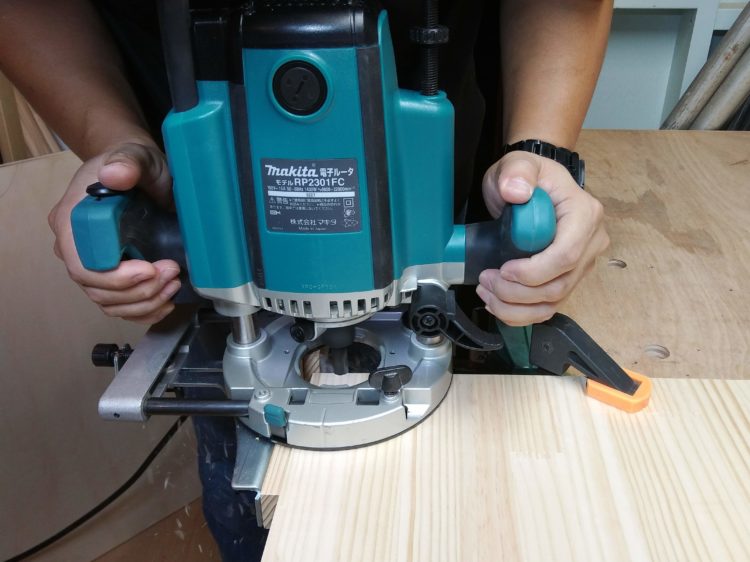
電源を入れ切削開始
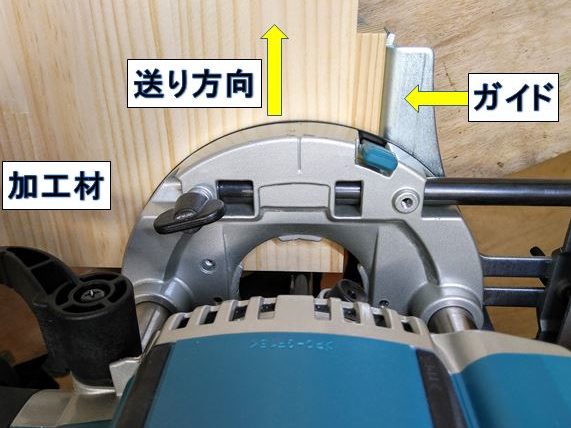
ルーター送り方向
加工材にビットが当たらない場所でスイッチをいれます。
ビットの回転が安定したらストレートガイドをしっかり加工材に押し当て切削していきます。
ルーターは加工材に対しストレートガイドが右手になる様にして、前方へ送ります。
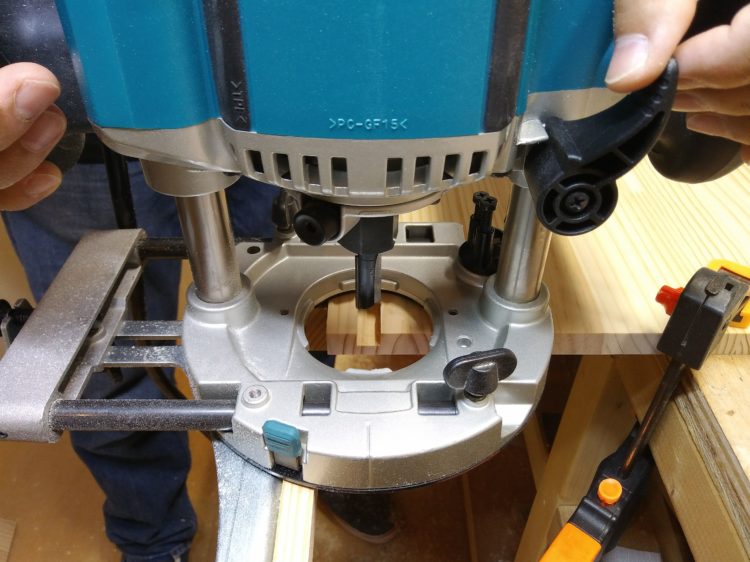
ロックレバーを解除しスイッチを切る
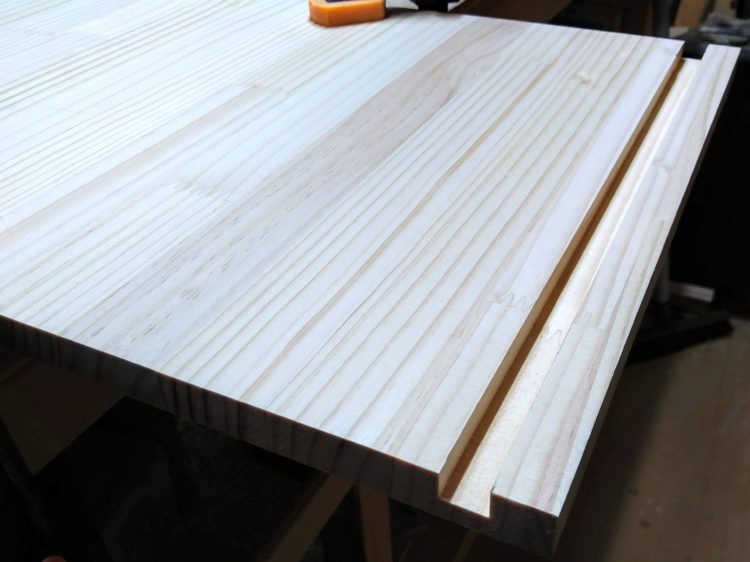
ストレートガイドによる溝ほり
切削が完了したら、ロックレバーを解除しビットを引き上げ、スイッチを切ります。
加工材の端から端へ通した溝加工ではない場合(加工材の途中から溝をほったり、途中で止める溝加工など)、ルーターの操作方法が異なります。
加工材の途中から切削を始める場合
- ルーターを切削位置に正確にセットする(ストレートガイドをきちんと加工材に押し当てた状態)
- ルーターのスイッチを入れビットを回転させる。
- ビットの回転が落ち着いたら、その位置で本体を設定した深さまで押し下げ、ロックレバーで固定する。
- 前方にルーターを送り切削する。
加工材の途中で止める溝をほる場合
- 止める場所まで切削して来たら、ルーターの送りをやめ、その場でロックレバーを解除し、本体を引きあげる。(ビットを引き上げる)
- スイッチを切る
ガイド(定規)による溝ほり
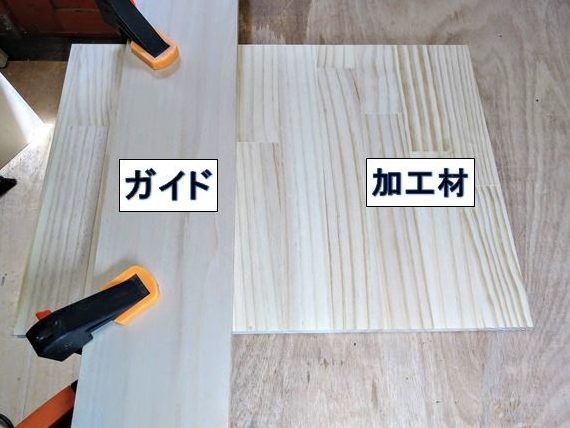
加工材にガイドを固定
加工材の端から離れた場所に溝をほる場合は、ストレートガイドは使えません。(ストレートガイドは比較的加工材の端から近い場所の溝ほり用です。)
真っ直ぐな面を持ったガイド(定規)を加工材に固定して切削します。
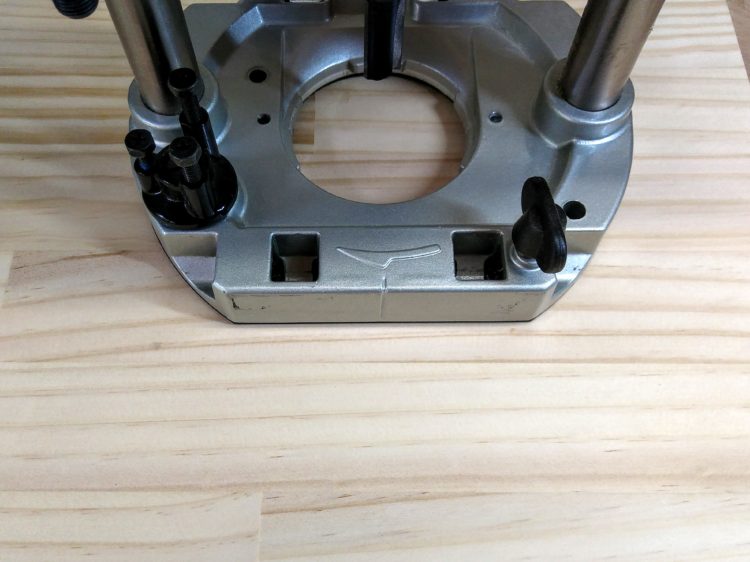
ベースの直線面
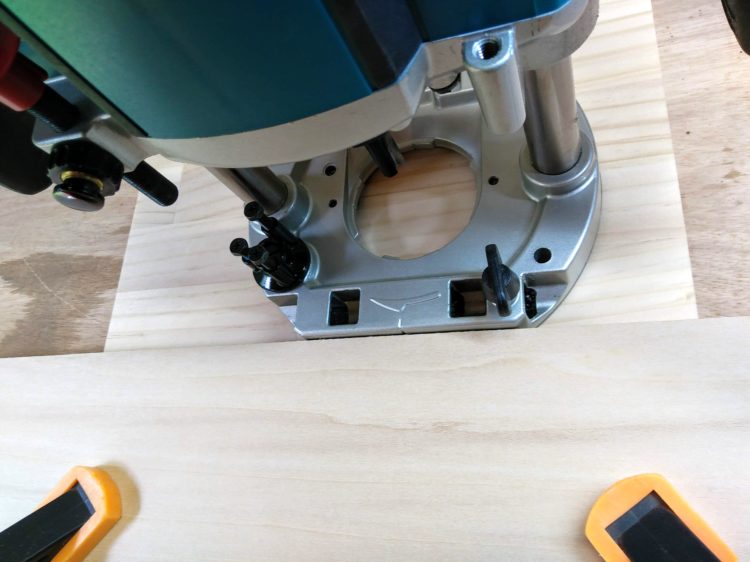
直線面をガイドに沿わせる
ルーターのベースには直線の辺になっている箇所があります。
ガイドにはベースの直線面を押し当て切削します。
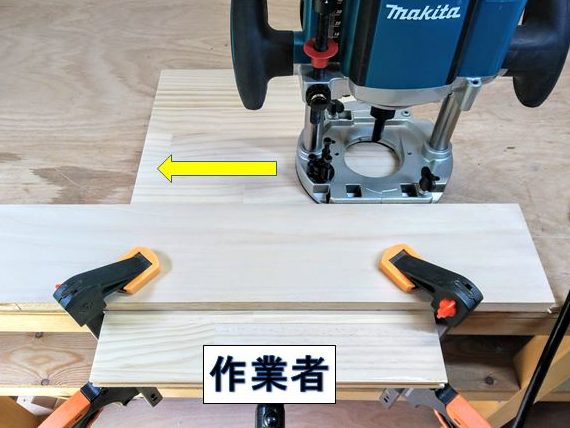
ルーターの送り方向と作業者の立ち位置
ガイドにルーターベースの直線面を沿わせると、作業者はハンドルの向きから、ルーターとの間にガイドを挟んだ場所に立ちます。
ルーターは作業者から見て右から左へ送り、切削します。
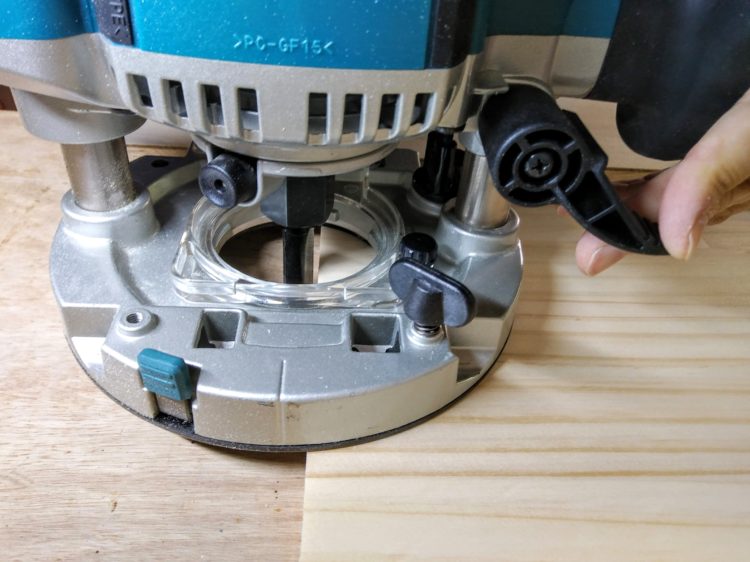
切削深さまで押し下げ固定
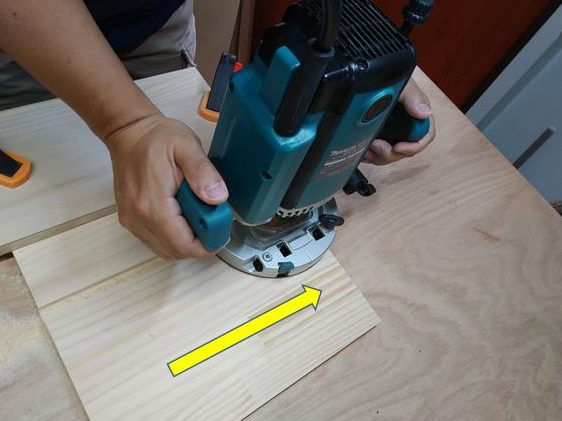
ルーター送り方向
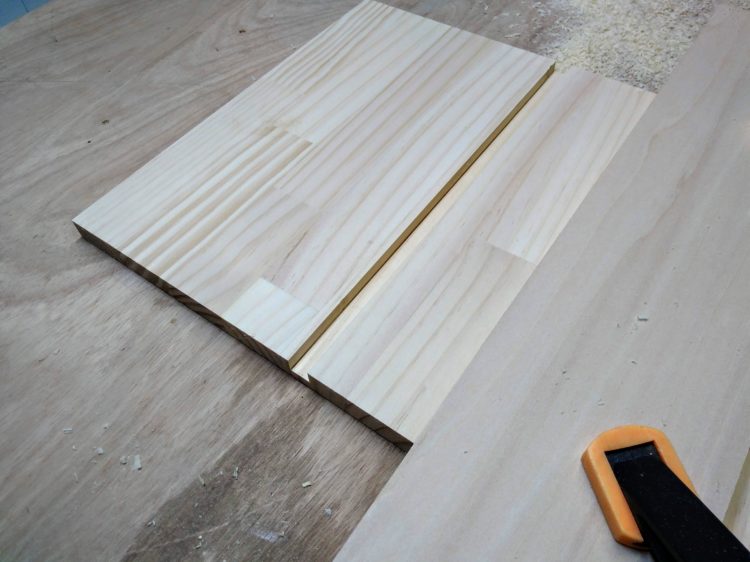
ガイド(定規)による溝ほり
加工材にルーターのベースを水平に乗せ、切削深さまで押し下げたらロックレバーで固定します。
スイッチを入れ、ガイドにしっかりと沿わせながら右から左へ切削していきます。
切削し終わったらロックレバーを解除し、本体を引き上げスイッチを切ります。
ならい加工
テンプレットガイド使用による窓あけ加工
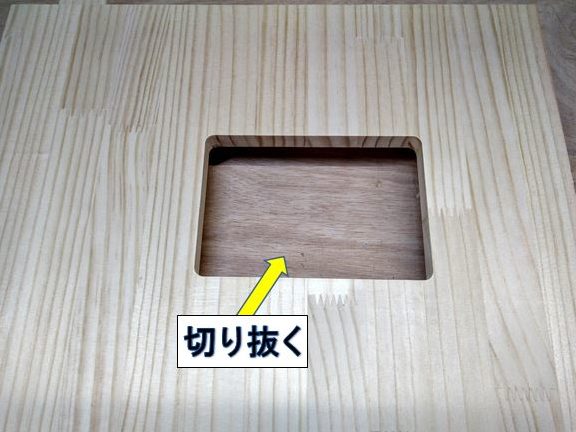
窓あけ加工
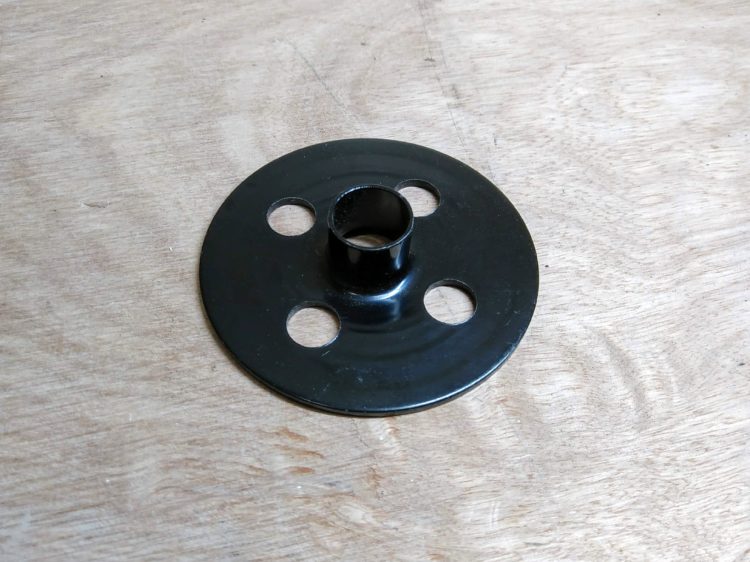
テンプレットガイド
型板(テンプレート)による窓あけ加工は、ルーターにテンプレットガイドを取り付けて行います。
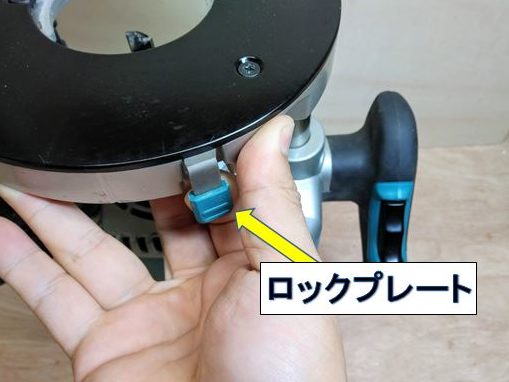
ロックプレートを引く
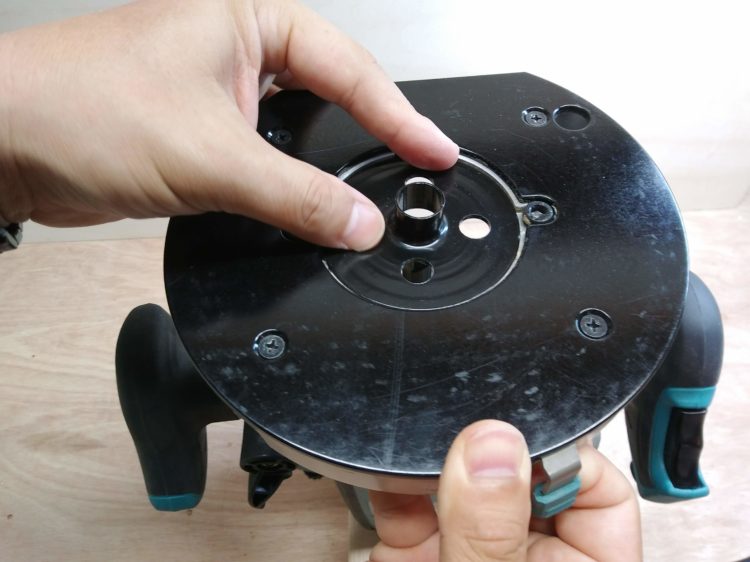
テンプレットガイドをはめ込む
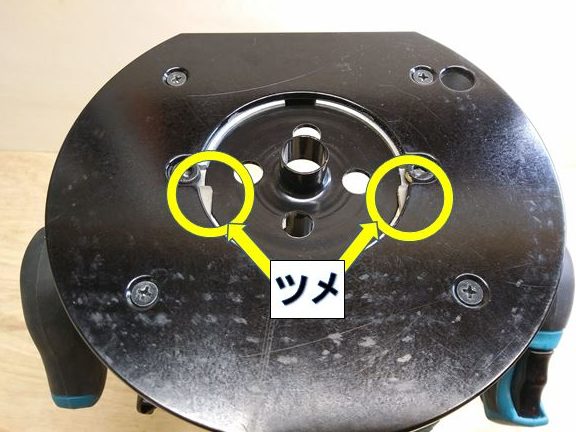
ツメが出て固定される
ルーター・ベース横のロックプレートを引き出しながらテンプレットガイドをはめ込みます。
ロックプレートを戻すと、左右にツメが出てテンプレットガイドが外れないように固定されます。
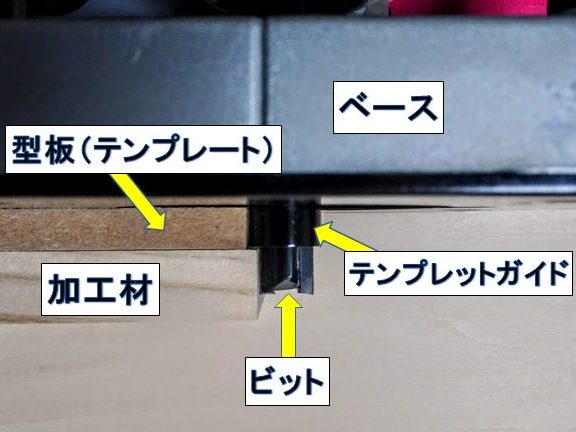
テンプレットガイド・型板・加工材・ビットの各位置
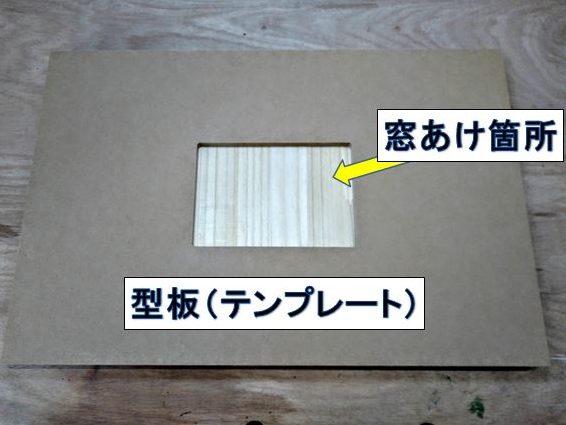
加工材の上に型板(テンプレート)を固定
切削時、テンプレットガイドが型板(テンプレート)に沿う事で、ならい加工が出来ます。
加工材の上に型板(テンプレート)を固定する事になります。
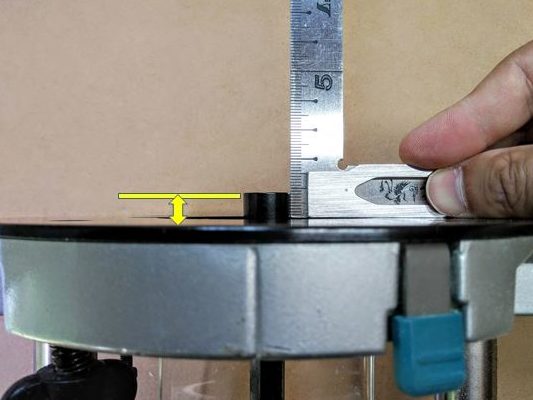
ルーターのベース面からテンプレットガイドの先端までの長さ
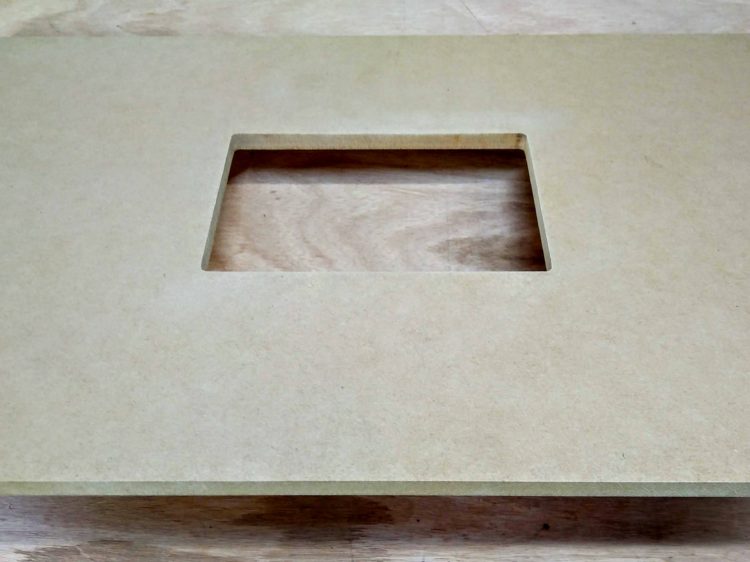
厚み9mmのMDFで型板(テンプレート)を作製
型板(テンプレート)を作製する際、厚みに注意が必要です。
型板(テンプレート)の厚みがルーター・ベース面からテンプレットガイドの先端までの長さより薄かった場合、テンプレットガイドが加工材に当たって乗り上げてしまいます。
必ず型板(テンプレート)の厚みはルーター・ベース面からテンプレットガイドの先端までの長さより厚くします。
今回はルーターのベース面からテンプレットガイドの先端までの長さを測ると約8.5mmあるので、厚み9mmのMDFを型板(テンプレート)として使用します。
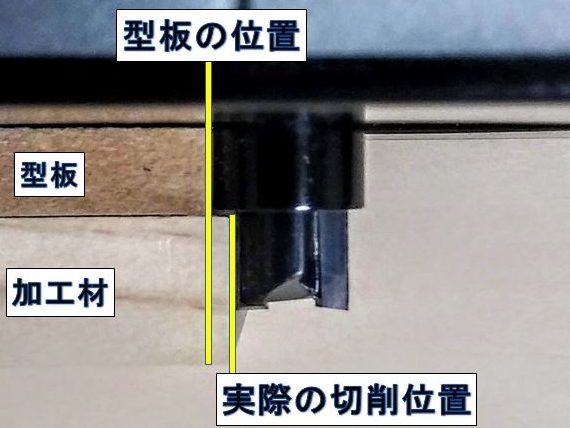
型板(テンプレート)と実際の切削位置のズレ
型板(テンプレート)を加工材に固定する際、位置に注意が必要です。
テンプレットガイドの構造上、型板(テンプレート)の位置と実際の切削位置にズレが生じます。
ルーターのテンプレットガイドには様々な種類があり、使用するビットの刃径によってもズレの値が異なります。
型板(テンプレート)を正確な位置に固定する為に、テンプレットガイドと実際に切削する位置(ビット位置)のズレを確認しておく必要があります。
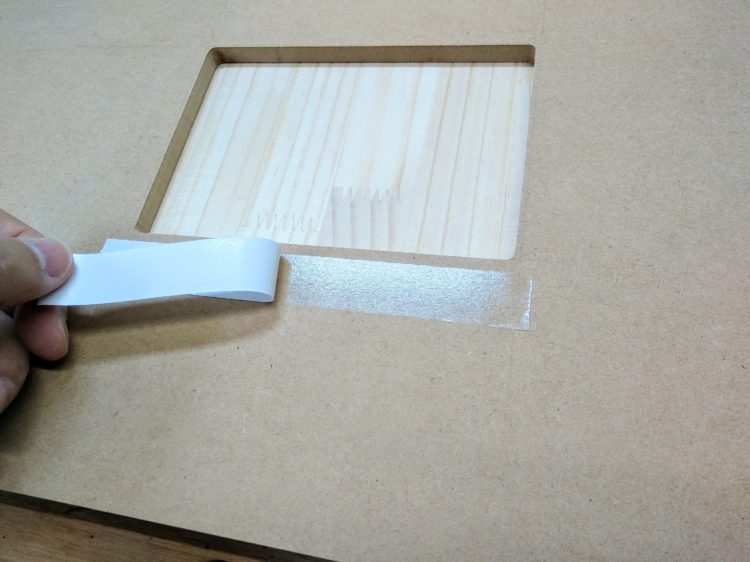
型板(テンプレート)裏側に両面テープを貼る
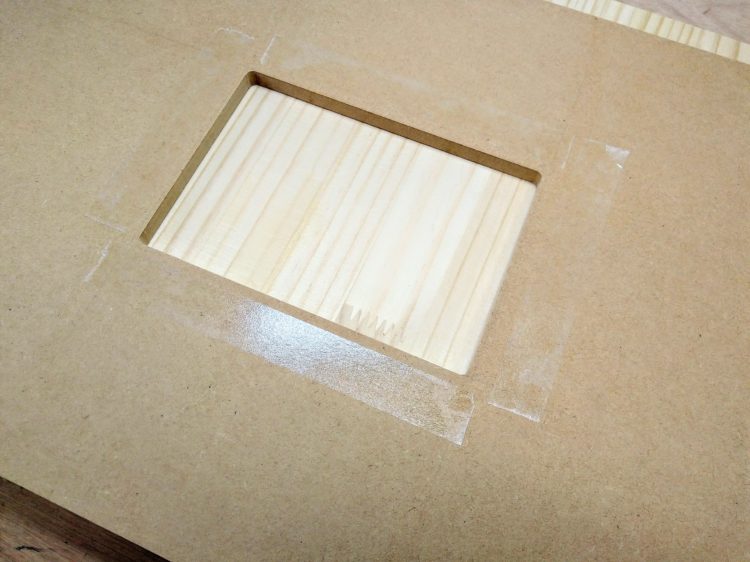
4辺すべてに貼る
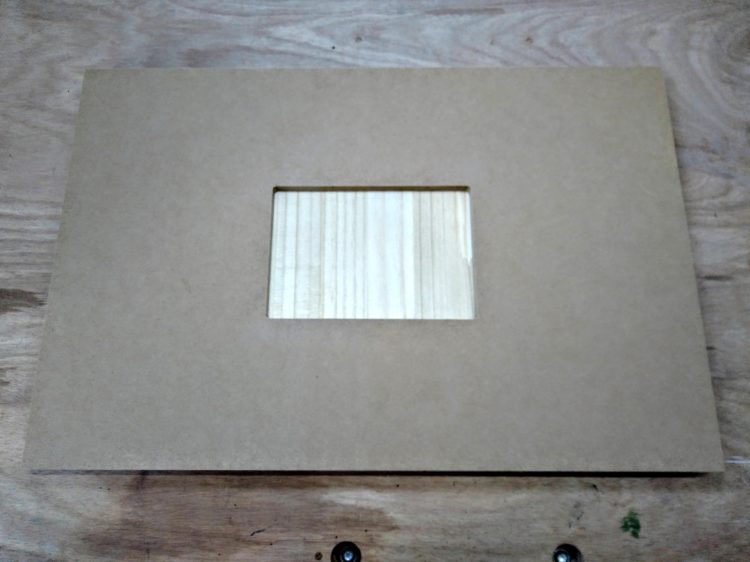
加工材に型板(テンプレート)を固定
加工材に型板(テンプレート)を固定する際、クランプ等を使用しますが、両面テープを貼り付け固定する場合もあります。
一般用両面テープで厚み0.1mm程度の物を使用し、張り合わせて固定します。
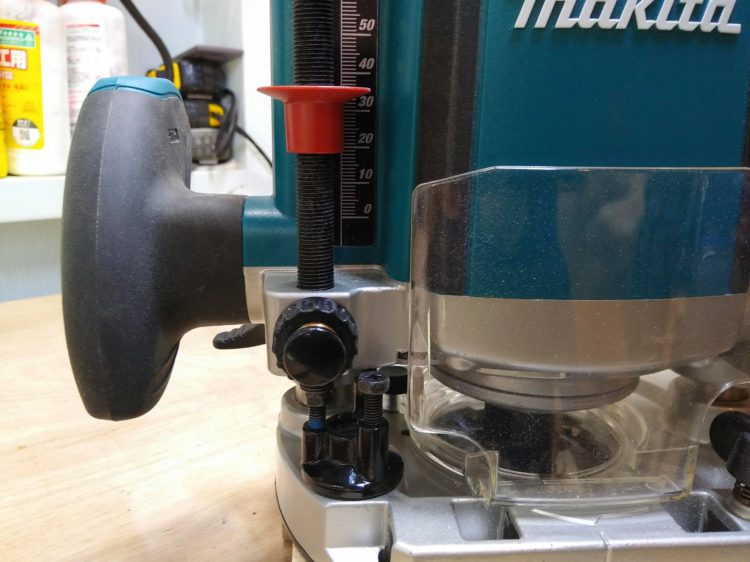
ビットの切削深さを設定
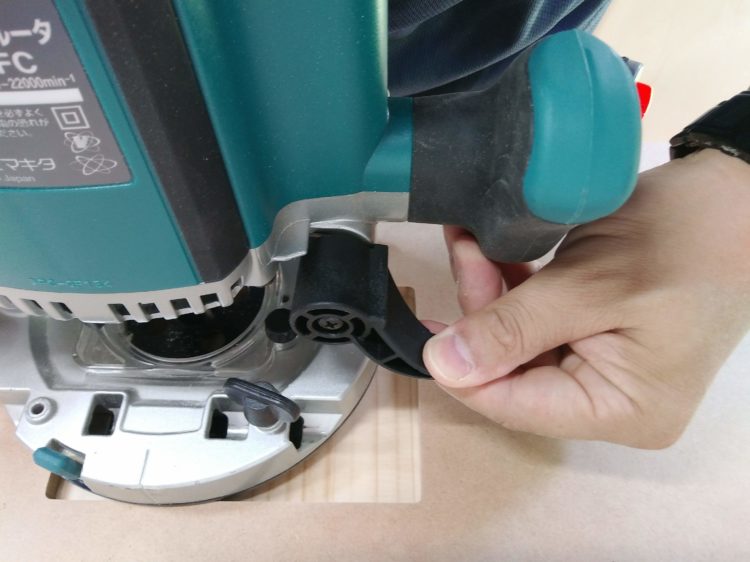
設定した深さで固定
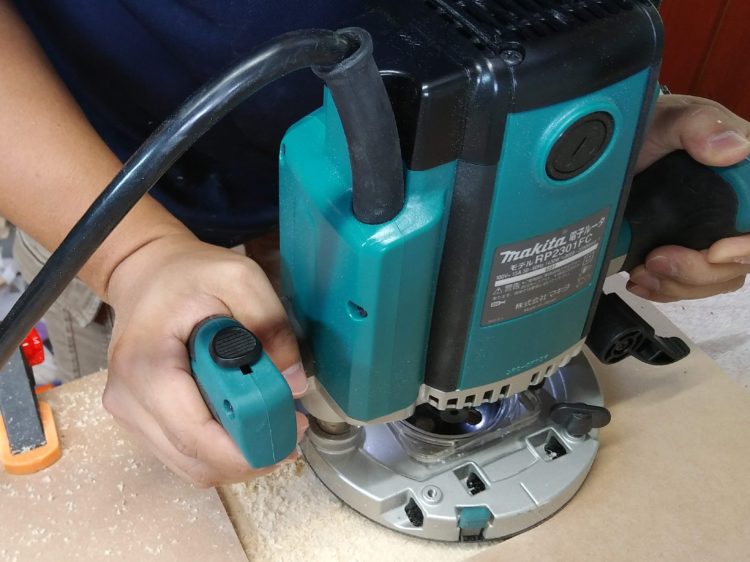
切削し始めます
窓あけ加工のビットの切削深さは、加工材の板厚+型板(テンプレート)の厚みに設定します。(実際に切り抜くには+2~3mm深く設定します)
切り抜く場所の内側の型板(テンプレート)から少し離れたところでスイッチを入れます。
ビットの回転が安定したら設定した切削深さまでルーターを押し下げ、ロックレバーで固定します。
ルーターをそのまま移動し型板(テンプレート)に沿わせて切削していきます。
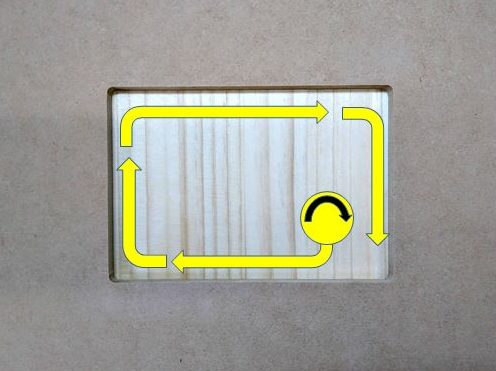
ルーターを時計回りに送る
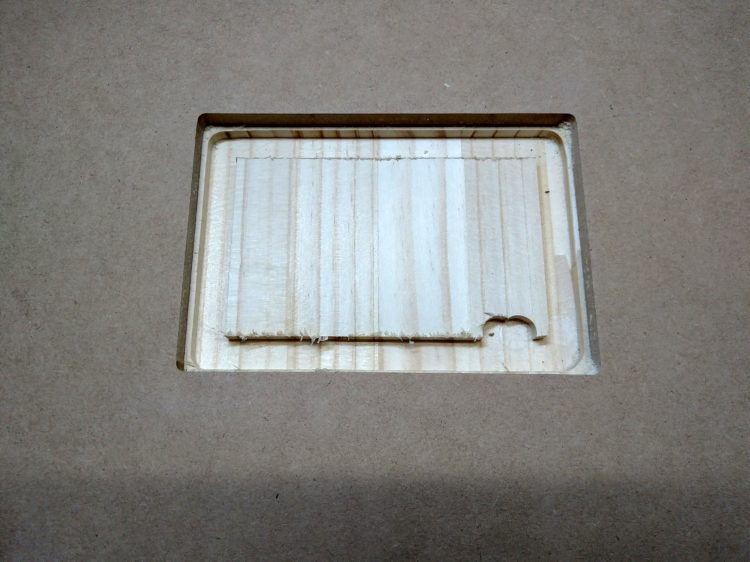
切削一回目
ルーターの送り方向は、時計回りに送り切削します。
ストッパブロックを利用し、何回かに分けて深さを変え切削します。
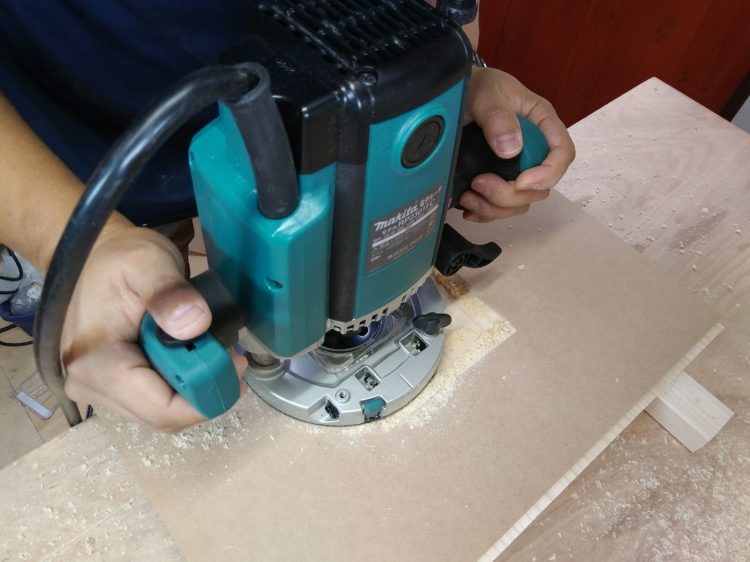
何回かに分け切削
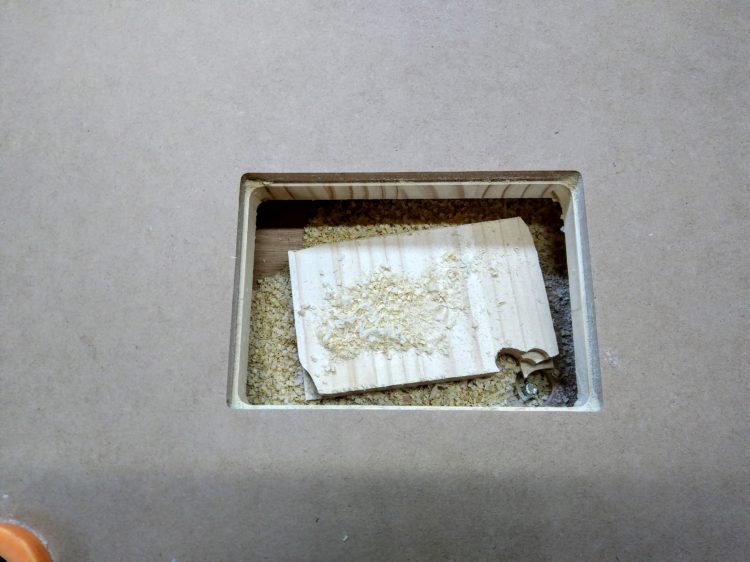
切り抜けました
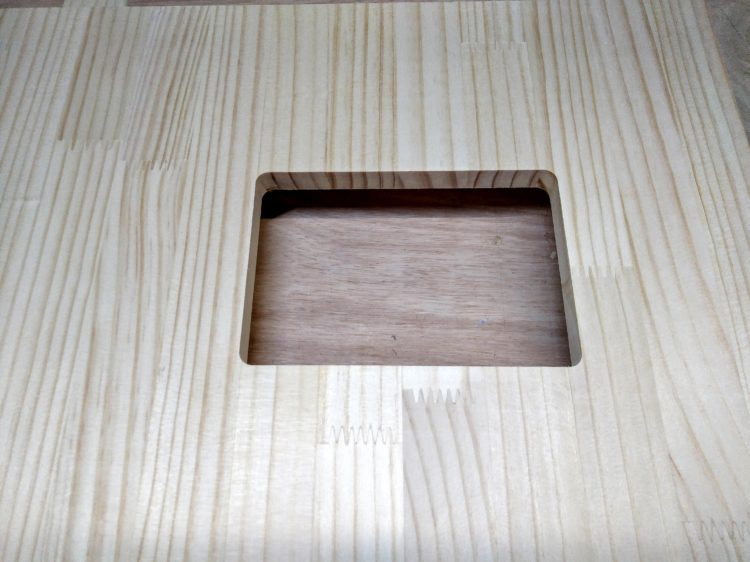
窓あけ加工完了
テンプレットガイドを使用した窓あけ加工の完成です。
コロ付ビット(トップベアリング・パターンビット)によるならい加工
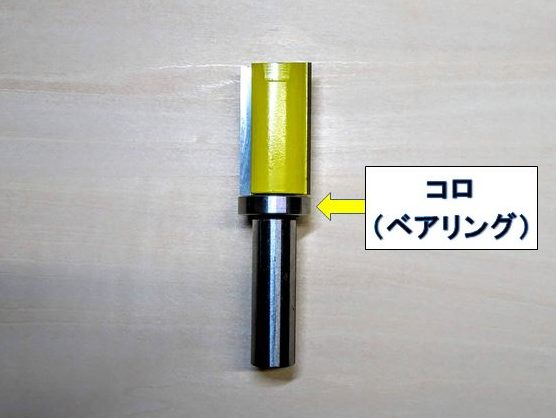
トップベアリング・パターンビット
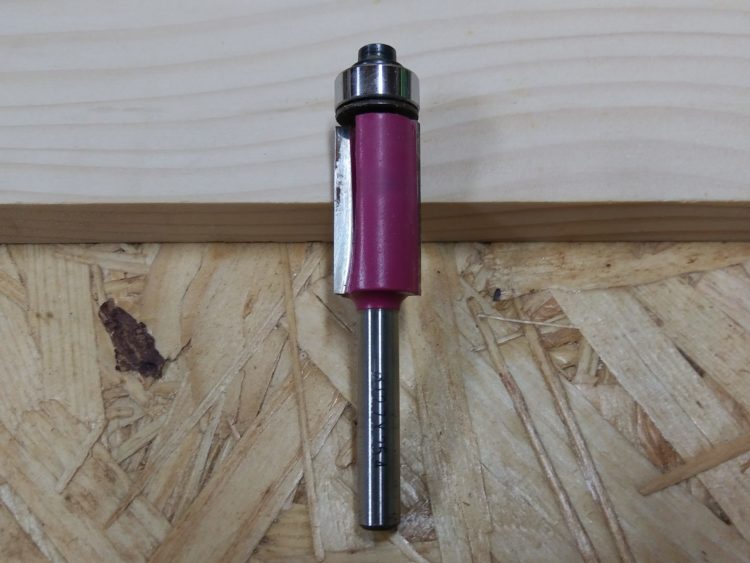
コロ付フラッシュビット
ルーターにテンプレットガイドを装着して行うならい加工は、型板(テンプレート)と実際に切削した部材にずれが生じます。(型板に直接あたるのはテンプレットガイドで、ビットはその外側を切削する為)
あらかじめ、テンプレットガイドとビットの位置のずれを考慮して、型板(テンプレート)を固定する必要があります。
ビットの刃径と同じ寸法のコロ(ベアリング)が付属している、トップベアリング・パターンビットやコロ付フラッシュビットを使用すると、型板(テンプレート)と切削した部材にずれが無くならい加工が出来ます。
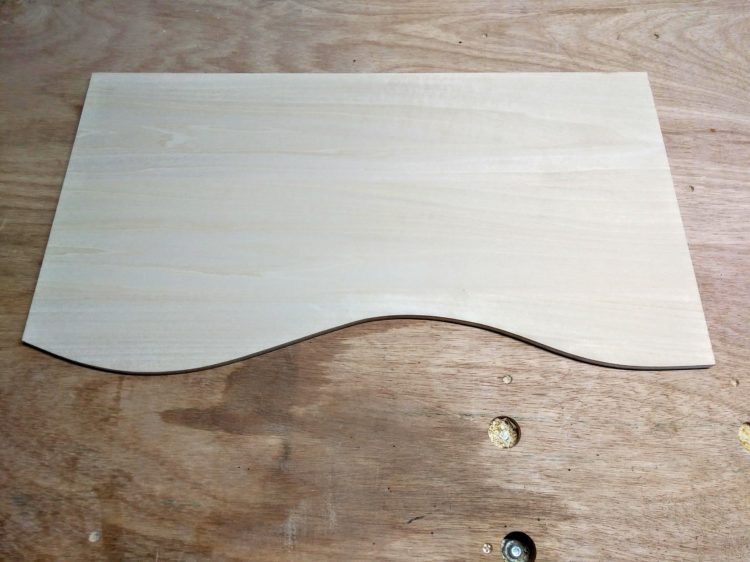
5.5mmシナべニアの型板(テンプレート)
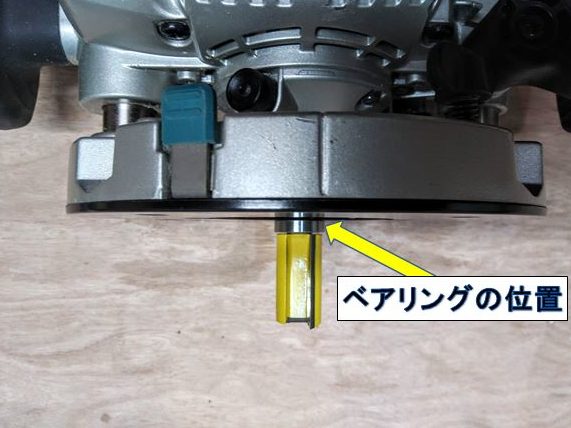
トップベアリング・パターンビット
型板(テンプレート)を5.5mm厚のシナべニアで作製し、トップベアリング・パターンビットを使用しならい加工をします。
トップベアリング・パターンビットはルーターに装着すると、ベアリングが刃より上に位置します。
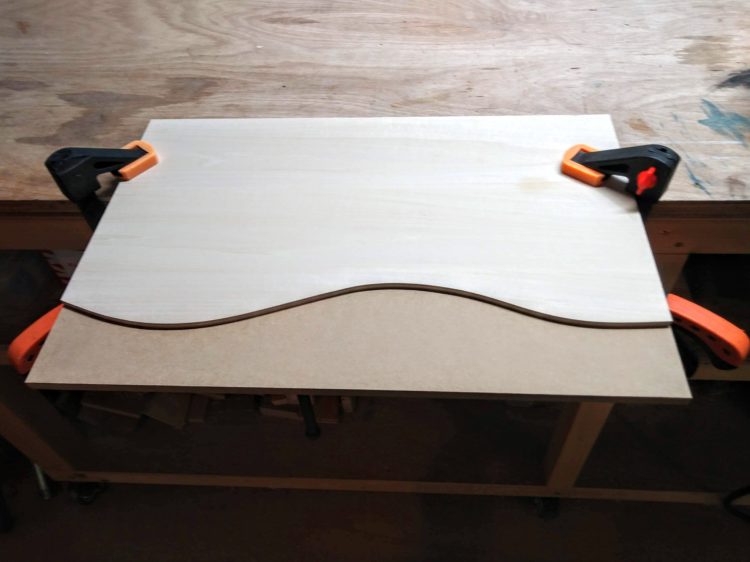
型板を上、加工材を下にし固定
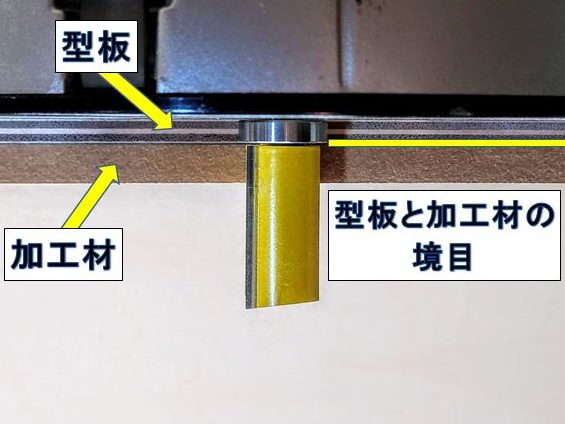
ビットの出具合
型板に沿うベアリングが刃より上にくるので、型板を上・加工板を下にして作業台に固定します。
(コロ付フラッシュビットを使用する場合は、型板下・加工板上にして固定します。)
ビットの出具合は、ベアリングの位置が型板と加工板の境目より上になる様にセットします。
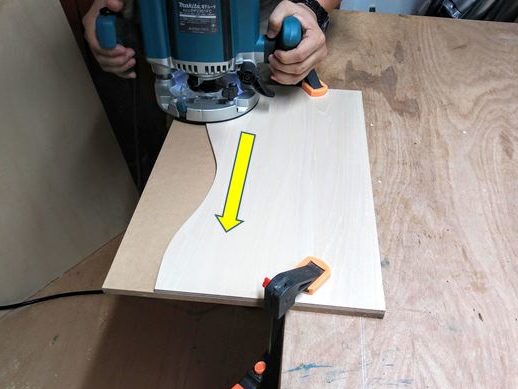
ルーターを前方へ送る
ビットの出具合をロックレバーで固定し、切削していきます。
加工面がビットの左手に来るようにして前方にルーターを送り切削します。
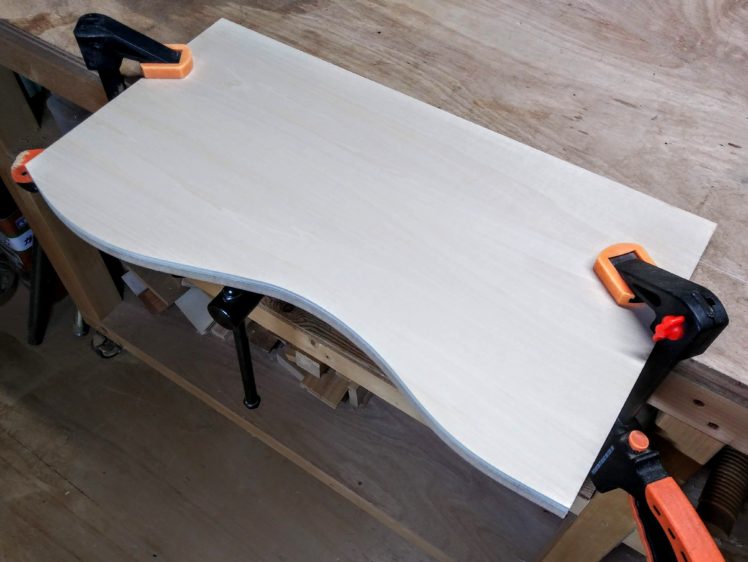
切削終了
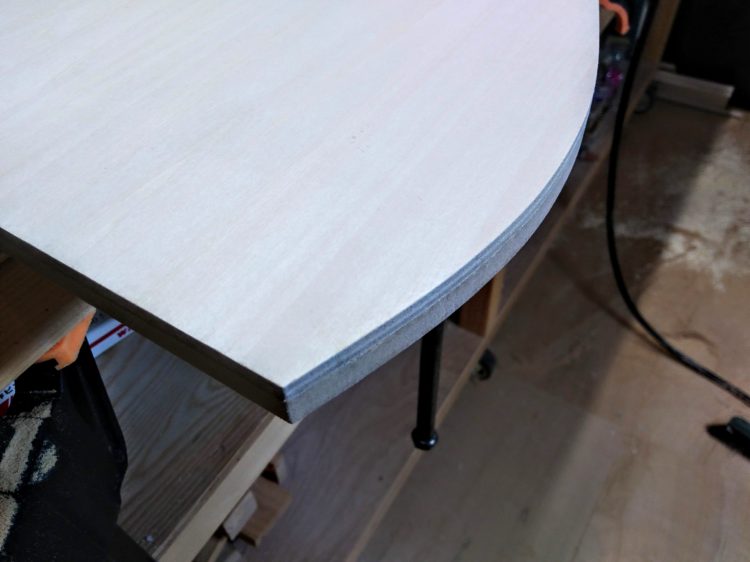
型板と面の仕上がり
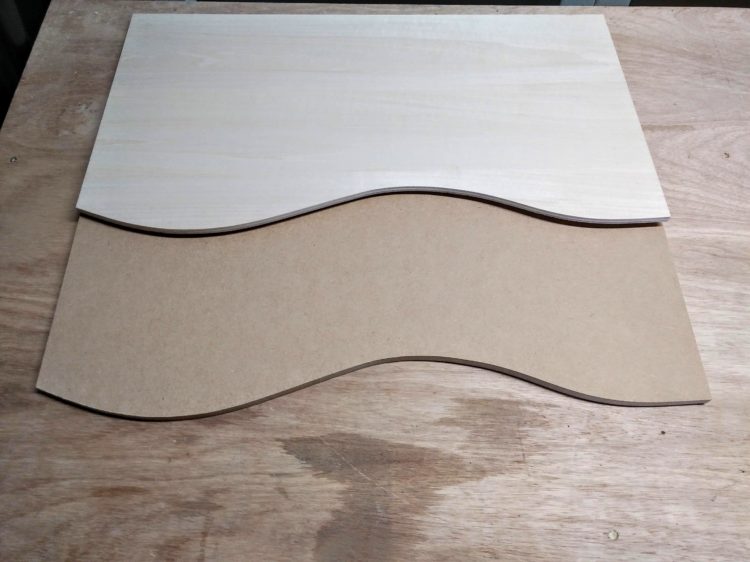
ならい加工完成
ベアリング付(コロ付)ビットでならい加工すると、テンプレットガイド使用時と違って、型板と加工材が面で仕上げる事が出来ます。
平滑加工
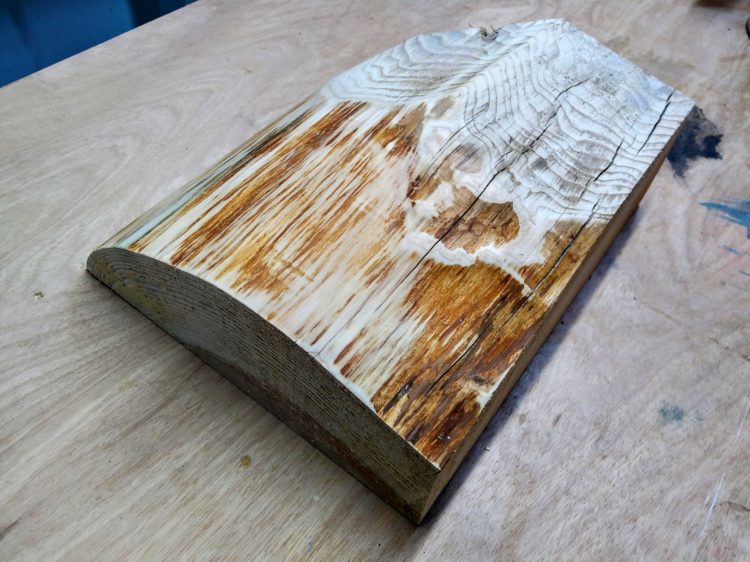
凹凸のある材料
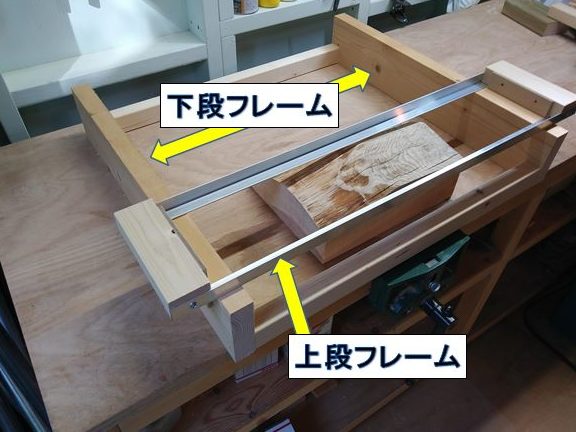
平滑面を切削する為の治具
ルーターでは治具を作製して、凹凸のある材料に平滑面を作る事が出来ます。
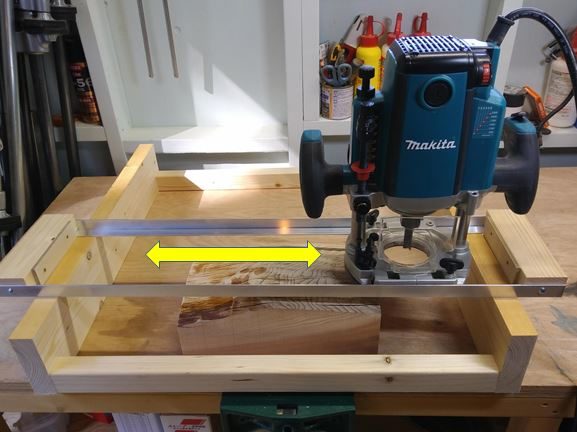
ルーターを左右にスライド出来る
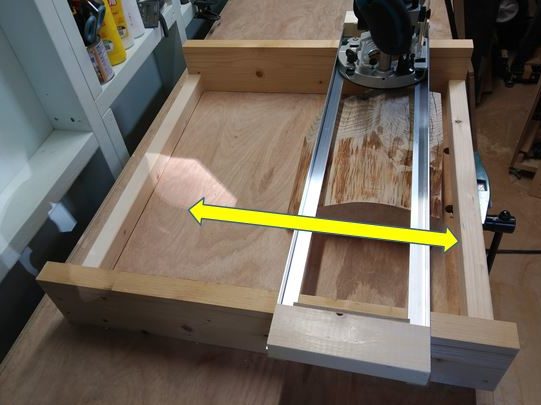
前後方向に移動できる
アルミのLアングルを使用した上段のフレームにはルーターがピッタリはまる様になっており、ルーターを左右にスライド出来ます。
上段フレームが水平になる様に、下段フレームの左右の高さは同じにしてあります。
上段フレームは前後方向にも移動する事が出来ます。
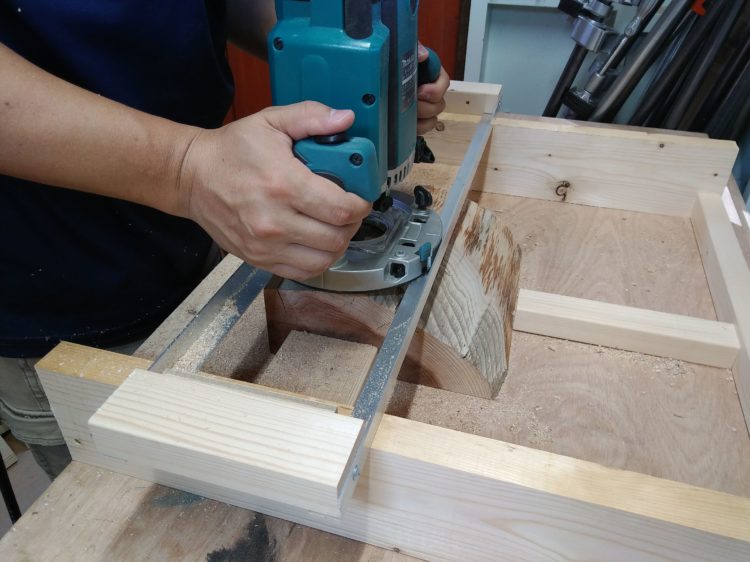
ルーターを左右に動かし切削
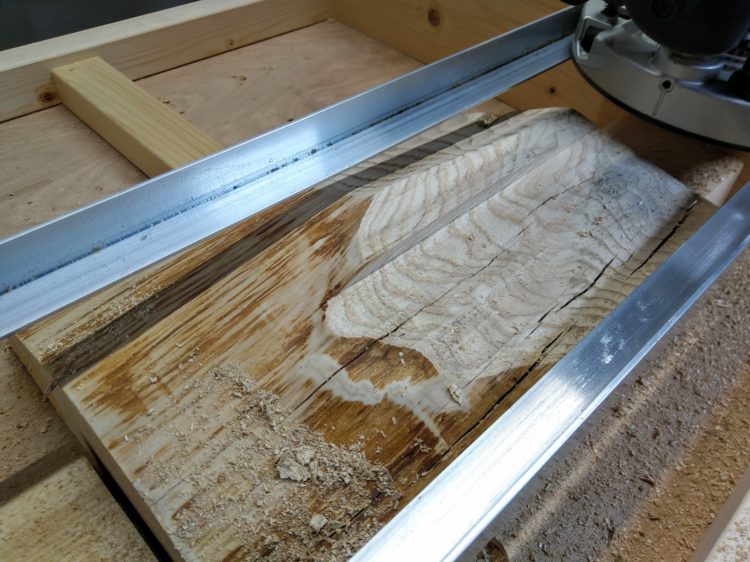
少しずつ前へ移動し切削
ストレートビットをルーターに装着し、切削の深さにセッティングします。
今回は深く(40mmほど)切削するので、ストッパブロックを使用し、徐々に深く掘り下げていきます。
手前側から切削し始め、ルーターを左右に動かし、徐々に前方へ移動・切削していきます。
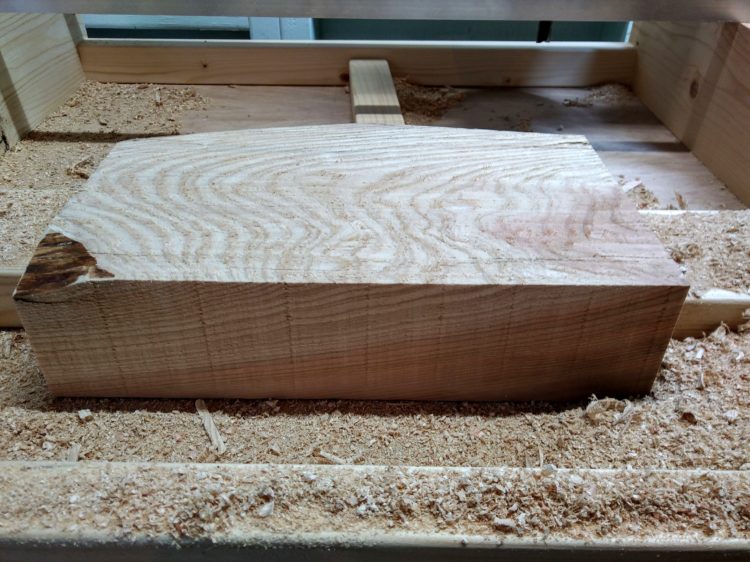
平滑面完成(40mm切削)
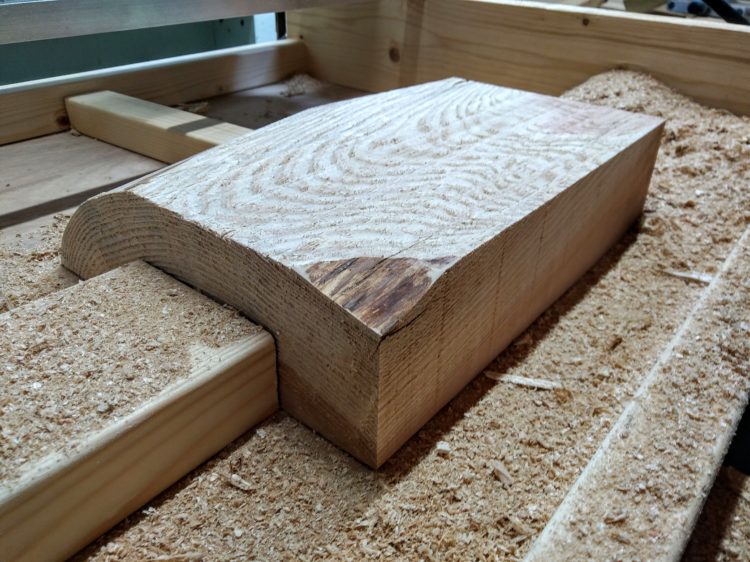
平滑面(横)
徐々に切削深さを深くしていき、平滑面の完成です。
今回の治具に手を加えると、くぼみや弧状の加工も可能です。
円加工
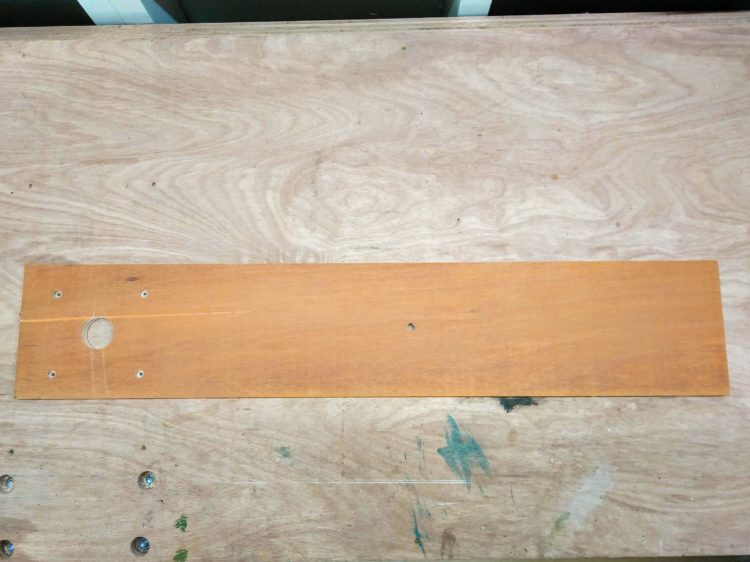
半径になる治具(板材)を用意
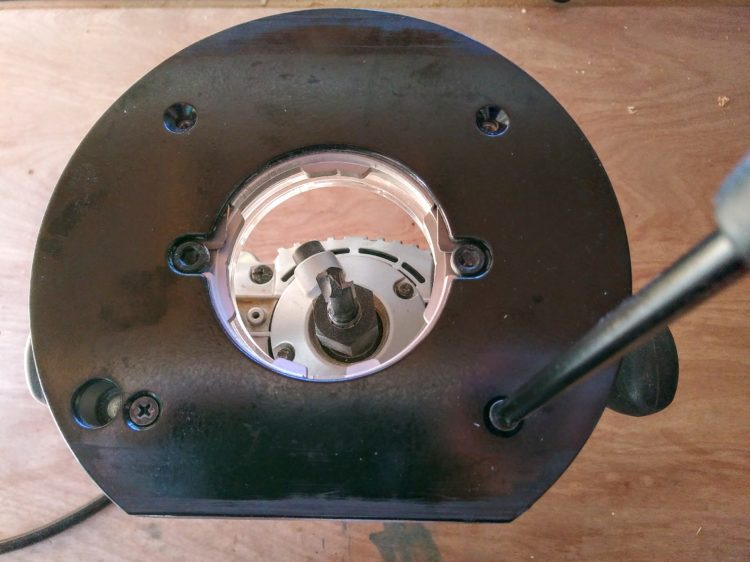
ベースプレートの固定ネジを外す
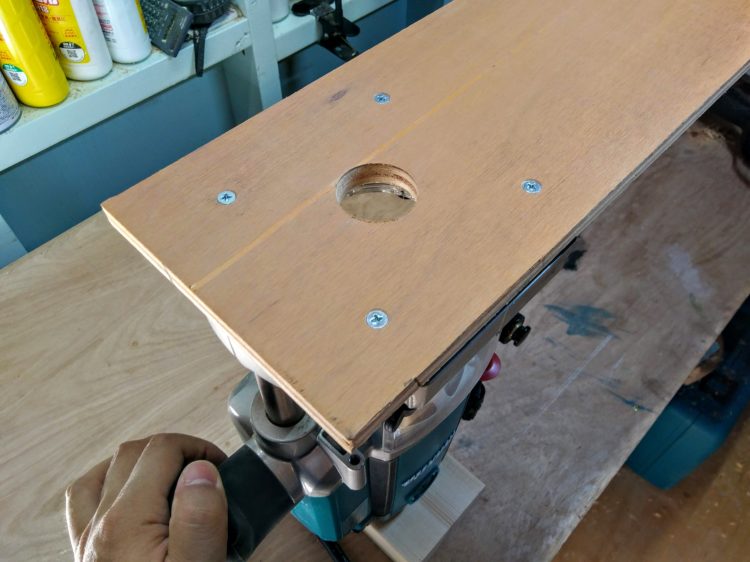
ルーターに治具を取り付け
ルーターに直接治具を取り付け円加工(今回は半円)をしていきます。
円の半径となる治具を用意します。(ビットの出し入れの箇所に穴をあけ、ルーターに取り付ける為のネジ穴をあけておきます。)
べープレートの固定ネジを外し、そのネジ穴を使用し治具をネジ止め・固定します。
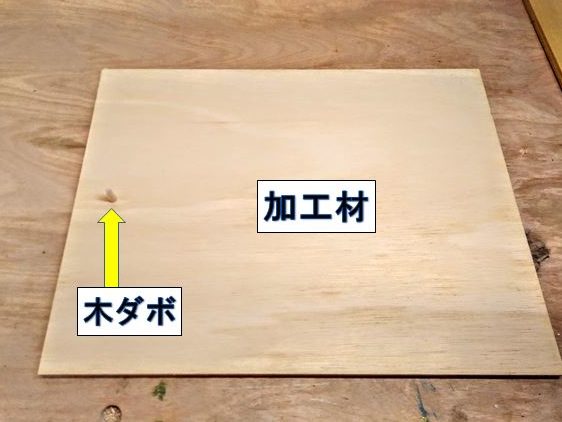
円の中心に木ダボを打ち込む
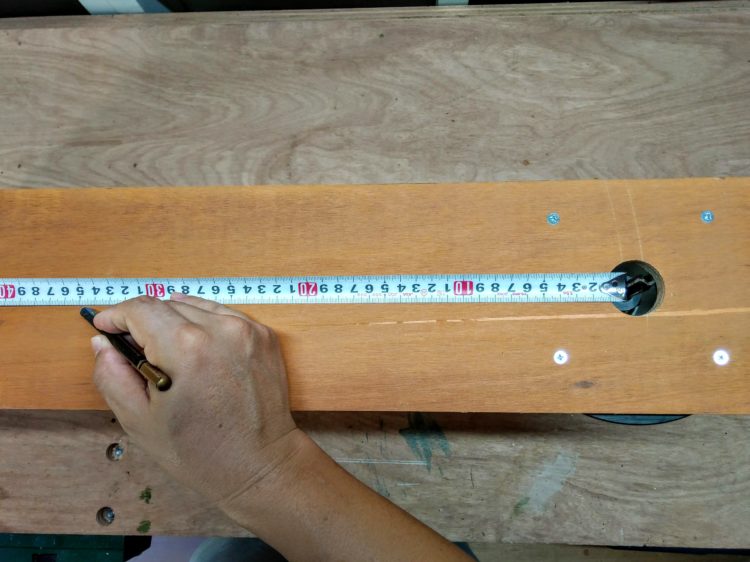
ビットから半径寸法の位置に墨付け
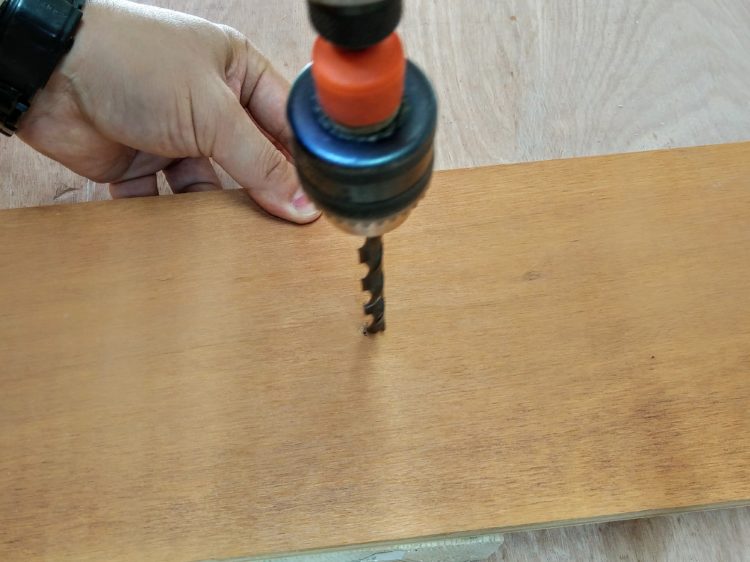
木ダボがはまる下穴をあける
加工材の円の中心に木ダボを打ち込んでおきます。
治具にはビットから任意の半径寸法を測った箇所に墨付けします。
治具の墨付けした箇所に、加工材に打ち込んである木ダボがはまる下穴をあけます。
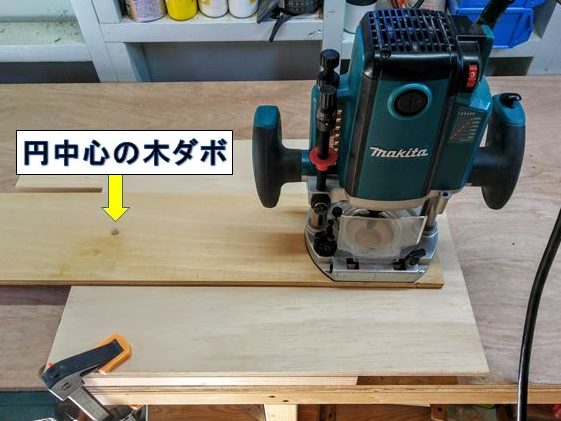
治具を加工材の木ダボにはめ込む
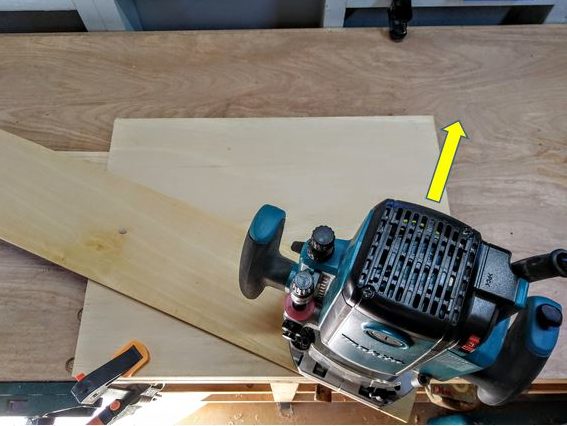
ルーターの進行方向
治具にあけた下穴に加工材の木ダボをはめ込みます。
円加工時のルーターの送り方向は、反時計回り(加工面がビットの左手に来る様にし、前方向に送る)になります。
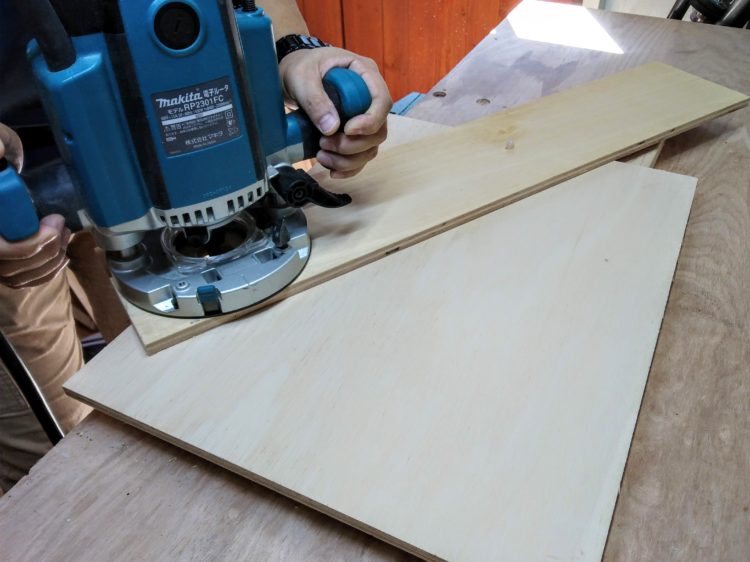
円切削開始
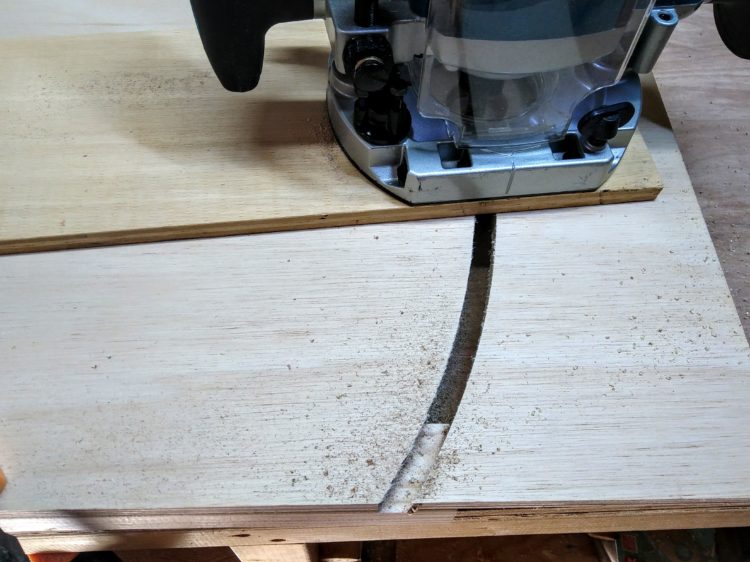
一定の速度でルーターを前方に送る
切削深さにビットを調整・固定したら、切削し始めます。
ルーターを一定の速度で前方に送り、切削していきます。
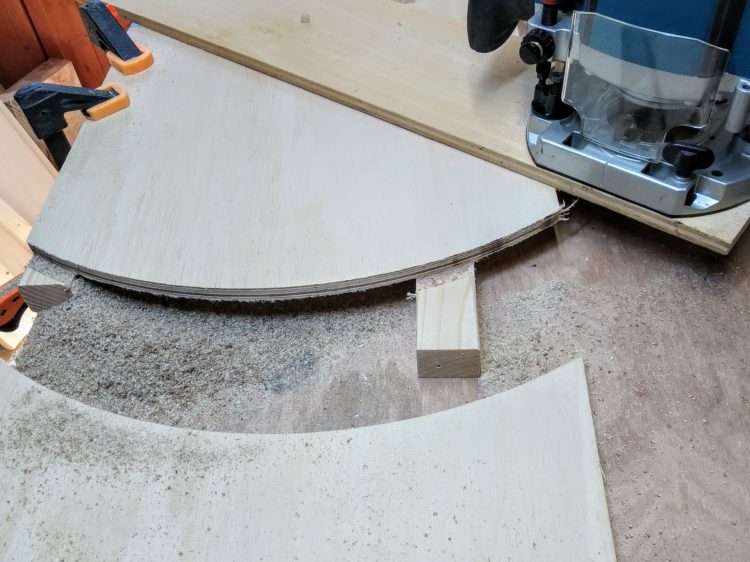
円(半円)加工終了
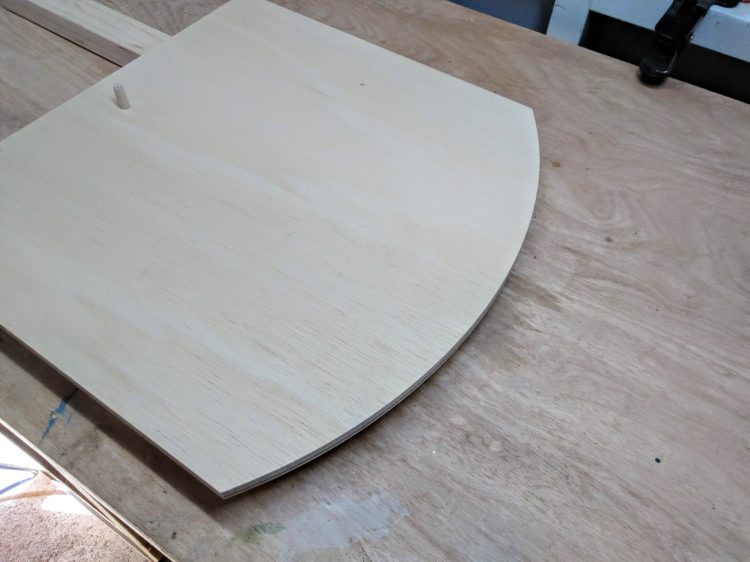
円(半円)加工完了
円(半円)加工の完成です。
ルーターテーブル
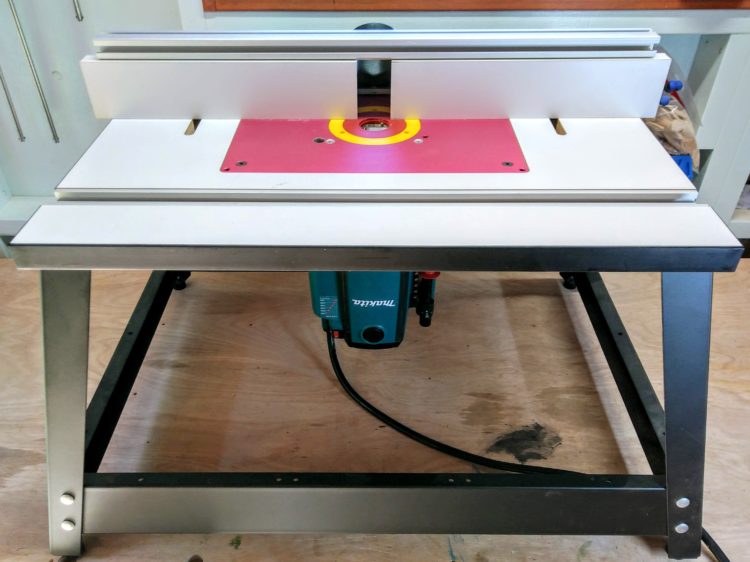
ルーターテーブル
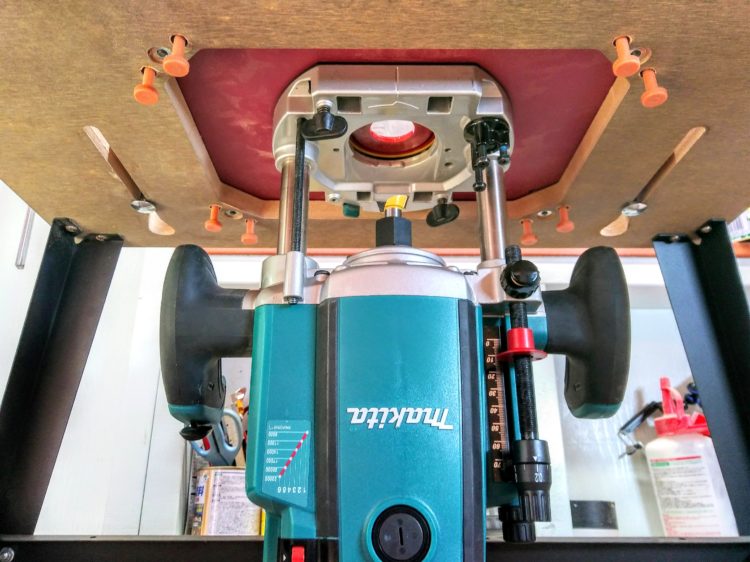
ルーターをテーブル裏面に取り付け
ルーターテーブルとは、逆さまにしたルーターをテーブルの裏面に固定し様々な切削加工を行うための土台となるテーブルです。
ビットがテーブル下から出てくる形になり、加工材を動かして切削加工します。
ルーターを手で保持する場合と違い、細かい加工や繰り返しの加工を安全に行うことが出来、大型のビットも使用可能になります。
ルーターテーブルの詳細に関しては、ルーターテーブルの構造と使い方 の記事を参照してください。
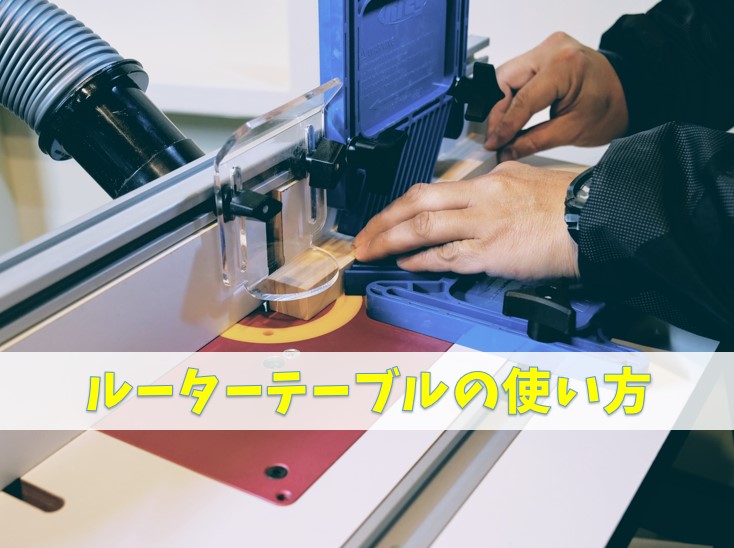
ルーターの送り方向まとめ
原則的にルーターは、加工材がビットの左手に来るようにして前方に送り、切削します。
ビットは時計回りに回転しており、送り方向が間違うとルーターの制御が難しくなり、正確な切削加工が出来なくなります。
色々な加工法におけるルーターの送り方向を説明していきます。
木端面の切削加工
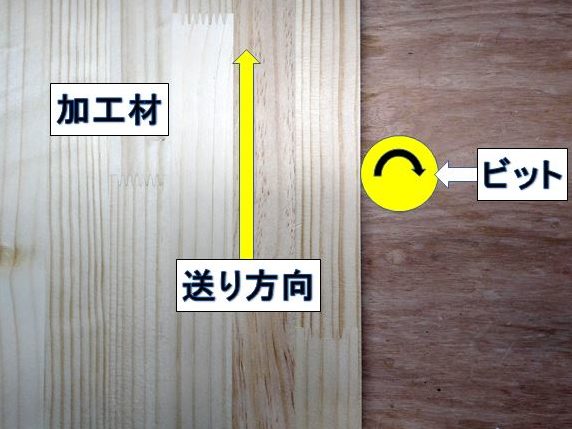
木端面の切削加工
コロ付ビットによる面取り加工など加工材の木端面に切削加工する場合は、ビットに対し左に木端面が来るようにしてルーターを前方に送ります。
ストレートガイドを使用する切削加工
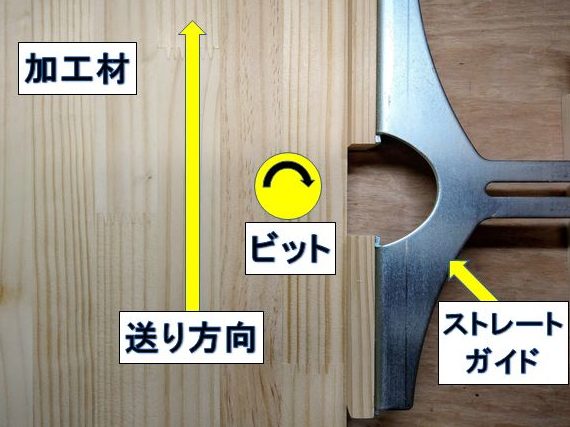
ストレートガイドを使用する切削加工
ストレートガイドを使用する場合は、ルーターの送り方向(前方)に対してストレートガイドが右側に来るようにして切削します。
ガイド(直定規)を使用する切削加工
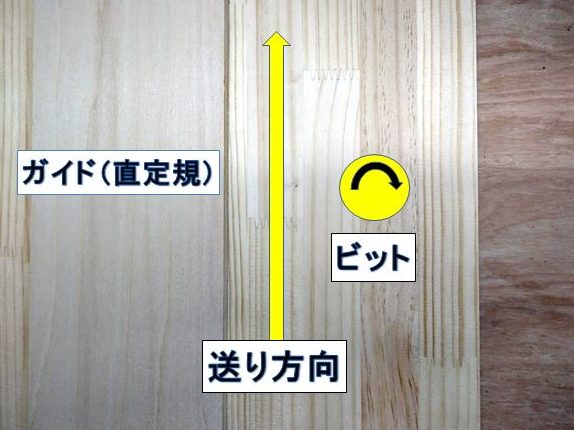
ガイド(直定規)を使用した切削加工
ガイド(直定規)を使用した切削加工の場合は、ガイド(直定規)を左側に来るようにして前方へルーターを送ります。
型板(テンプレート)を使用し内側を切削加工
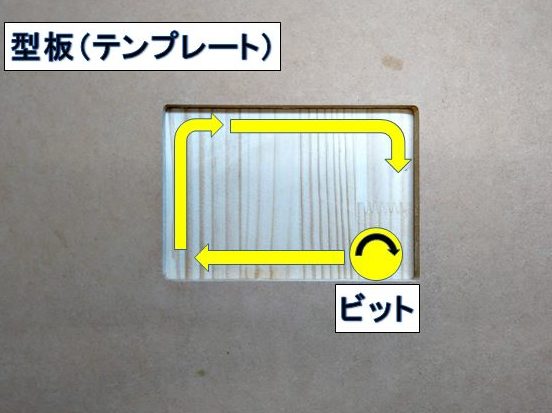
型板(テンプレート)を使用し内側を切削加
窓あけ加工などのならい加工で型板(テンプレート)の内側を切削加工する場合は、ルーターを時計回りに送り切削します。
型板(テンプレート)を使用し外側を切削加工
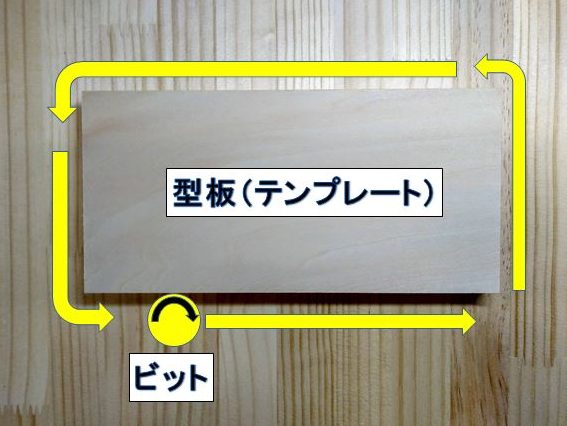
型板(テンプレート)を使用し外側を切削加工
コロ付ビットを使用したならい加工などで、型板(テンプレート)の外側を切削加工する場合は、ルーターを反時計回りに送り切削します。
円切削加工
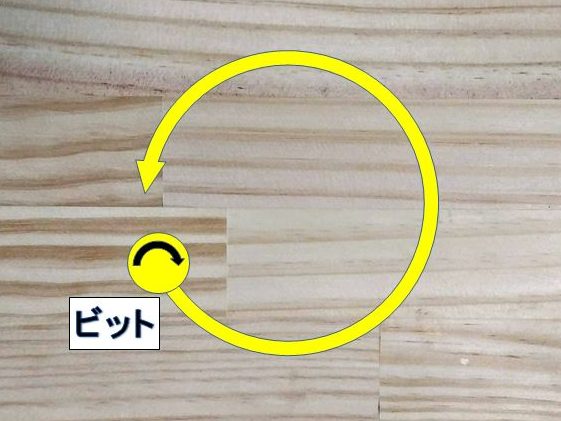
円切削加工
円切削加工を行う場合には、ルーターを反時計回りに送り切削します。
まとめ
今回は、ルーターの構造と使い方について説明しました。
ビットや治具を変える事で様々な加工が出来ます。
パワーがあり大きな物の加工もこなしますが、それなりに重量があるので、加工内容によってトリマーと使い分けする事が必要です。
今回使用したルーターはコチラです⇨
ぜひ参考にしてみてくださいね。