DIYにおいて、材料に穴をあけるという加工は非常に多い作業の一つです。
通常は、あける穴の大きさによってサイズの合うドリルビットに交換し、穴をあけます。
ドリルビットは、穴あけの径が大きくなるほど価格も高くなっていき、各サイズ揃えるのも大変になります。
そんな場合に便利なのが、”自在錐(自由錐)” です。
今回は、一つの錐で様々な径の穴あけが可能な ”自在錐(自由錐)” の種類と使い方を紹介します。
自在錐(自由錐)とは?
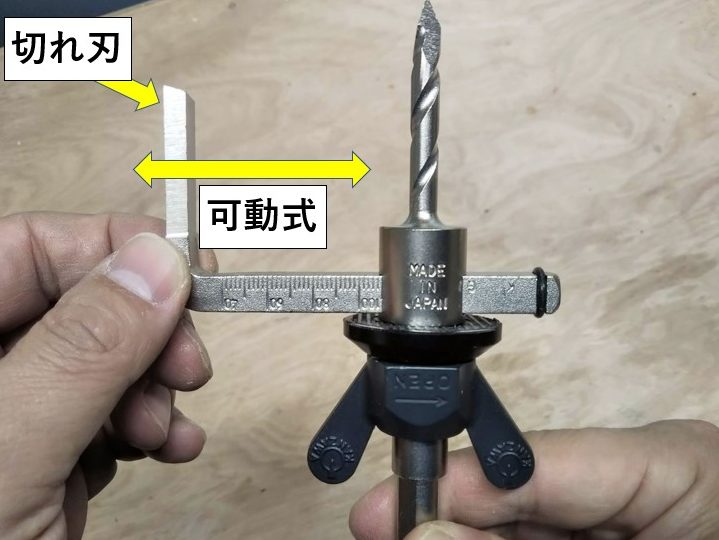
切れ刃が可動式
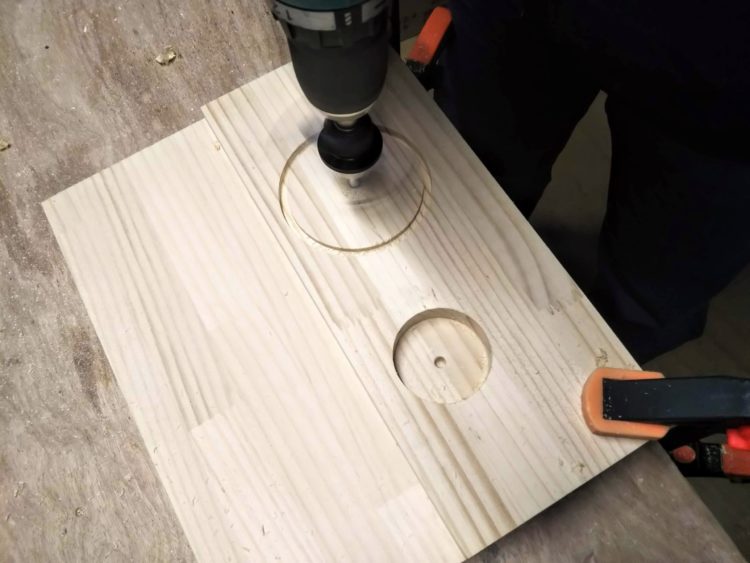
切れ刃の位置を変えて穴あけ
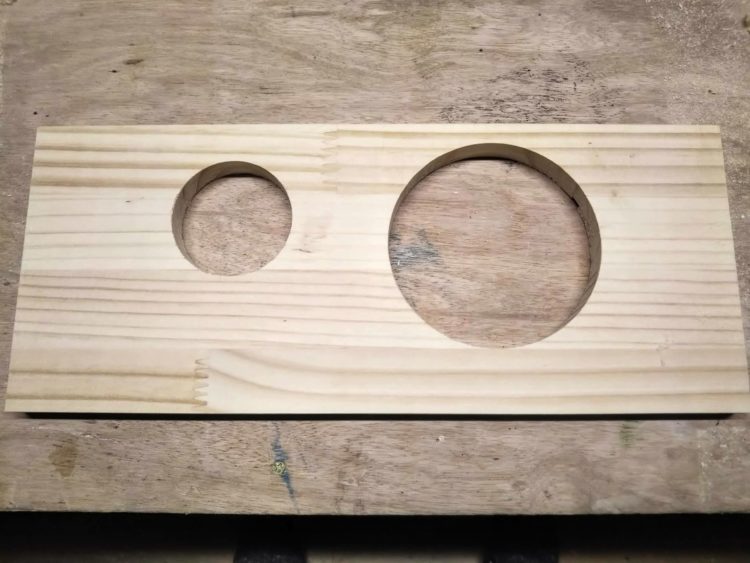
一つの錐で寸法の異なる穴あけが可能
”自在錐(自由錐)” は、通常のドリルビットと異なり、穴あけの径を自由に変えることが出来る錐です。
通常のドリルビットは穴の径ごとに一つ一つ揃える必要がありますが、自在錐(自由錐)は一つあれば様々な径の穴あけが可能で大変便利な錐です。
自在錐(自由錐)の種類
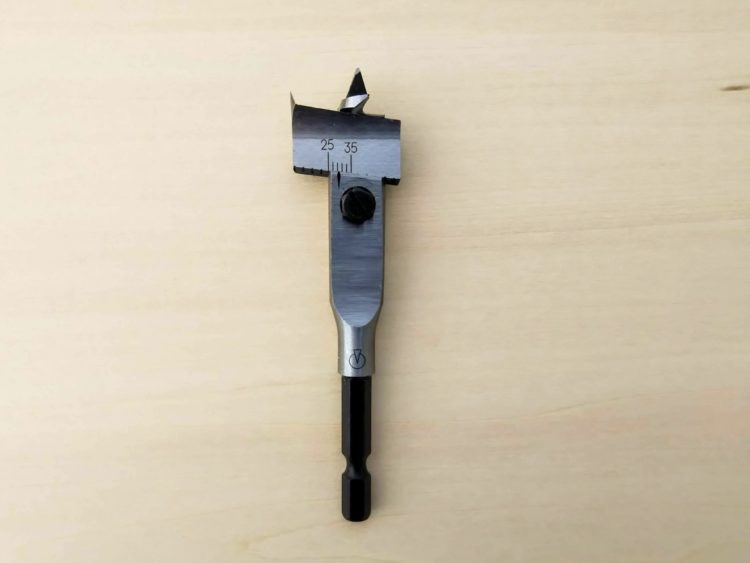
自在錐(小径穴用)
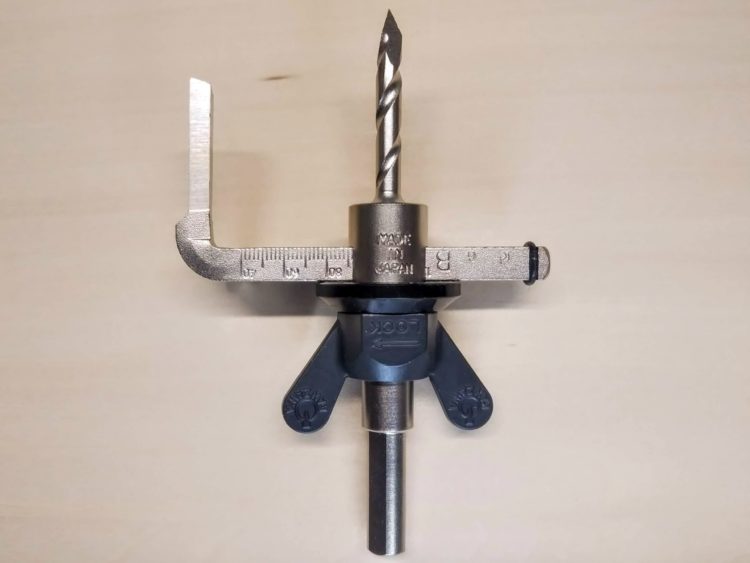
自在錐(大径穴用・片刃タイプ)
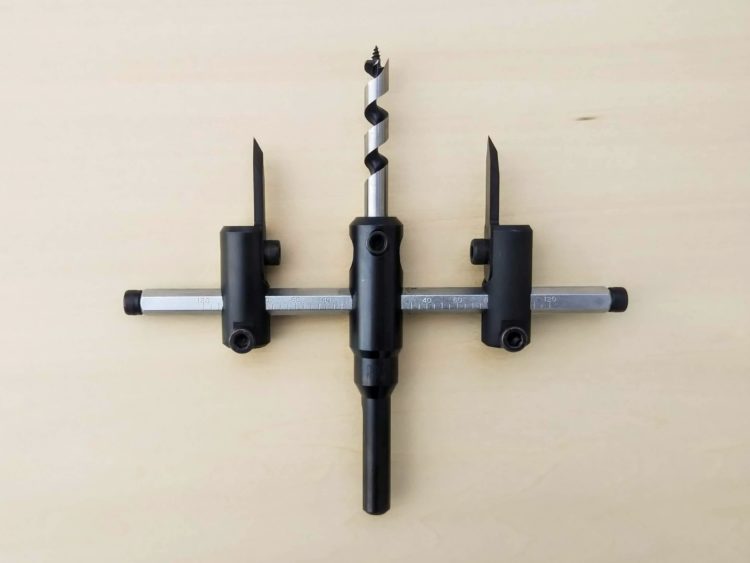
自在錐(大径穴用・両刃タイプ)
自在錐(自由錐)には、小さい径の穴あけ用と大きい径の穴あけ用があり、構造及び切削方法が異なります。
小径穴用自在錐
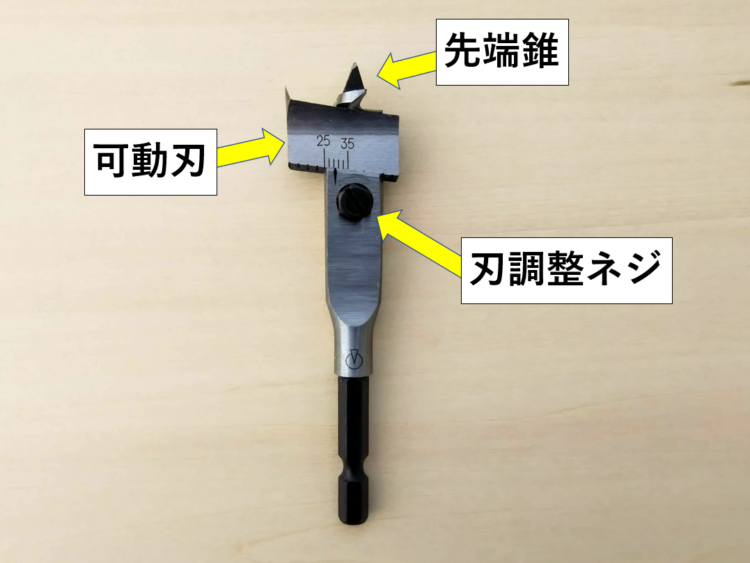
小径穴用自在錐・各部名称
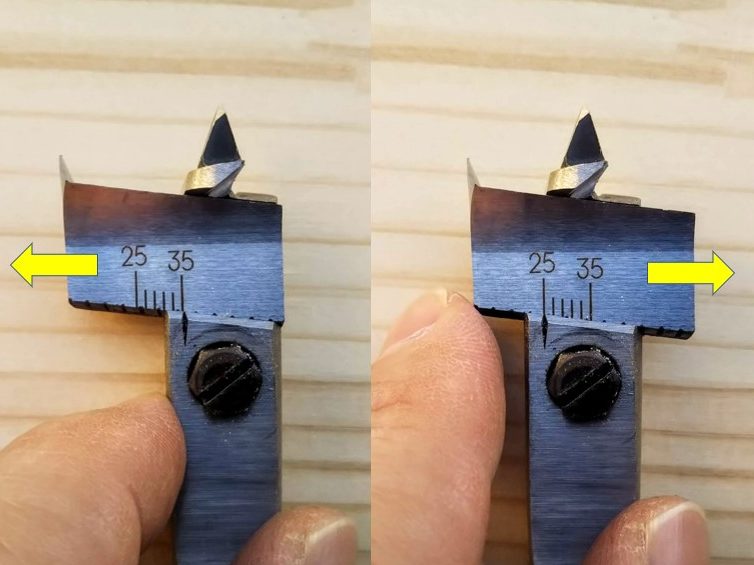
可動刃を左右にスライドさせる
小径穴用自在錐は、錐部分に先端錐と可動式の刃があり、可動刃をスライドさせることで、切削する穴の径を変える仕組みになっています。
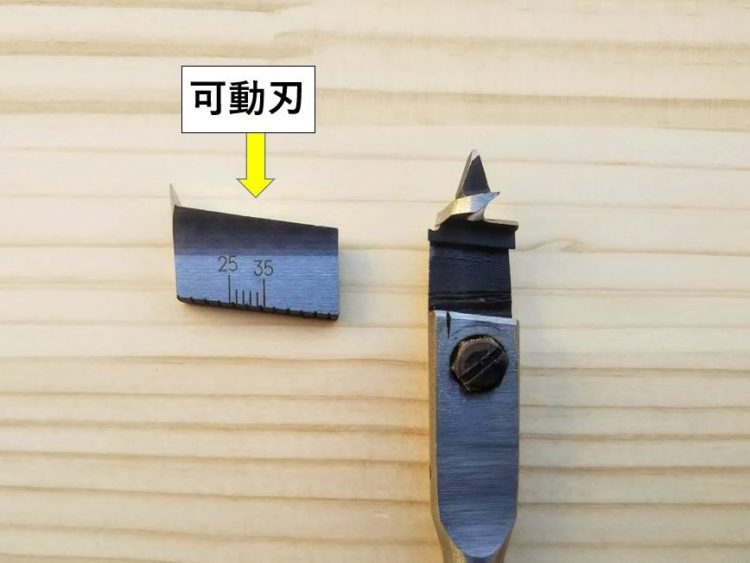
可動刃は取り外し出来る
可動刃は、取り外すことが出来、替え刃式になっています。
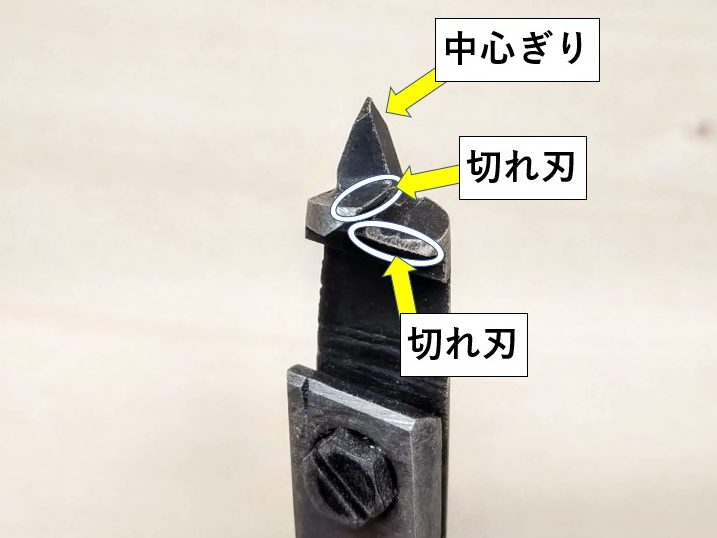
先端錐の構造
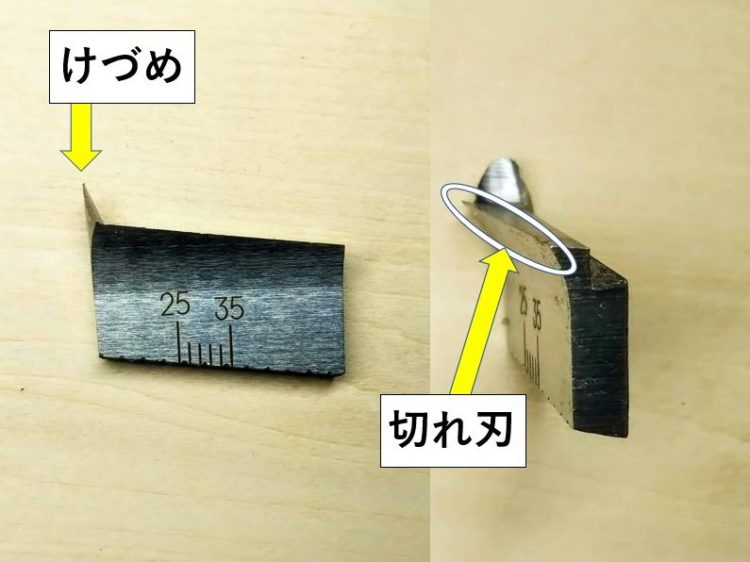
可動刃の構造
先端錐は中心ぎりと切れ刃がついており(通常のドリルビットと同じ形状)、中心ぎりがの穴あけのガイドを担い、切れ刃で穴を切削します。
可動刃にはけづめと切れ刃がついており、けづめで切削穴の外周をけがき(印の溝をつける)、切れ刃が穴を切削します。
先端錐と可動刃で穴全体を削りながら掘り進める仕組みです。
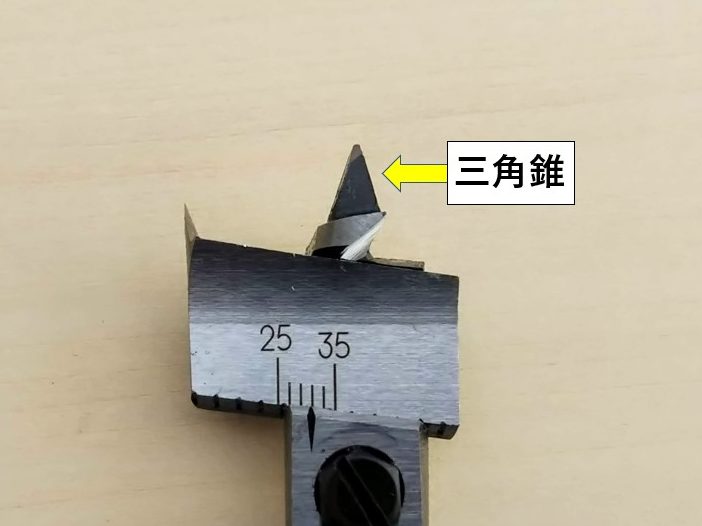
先端錐が三角錐
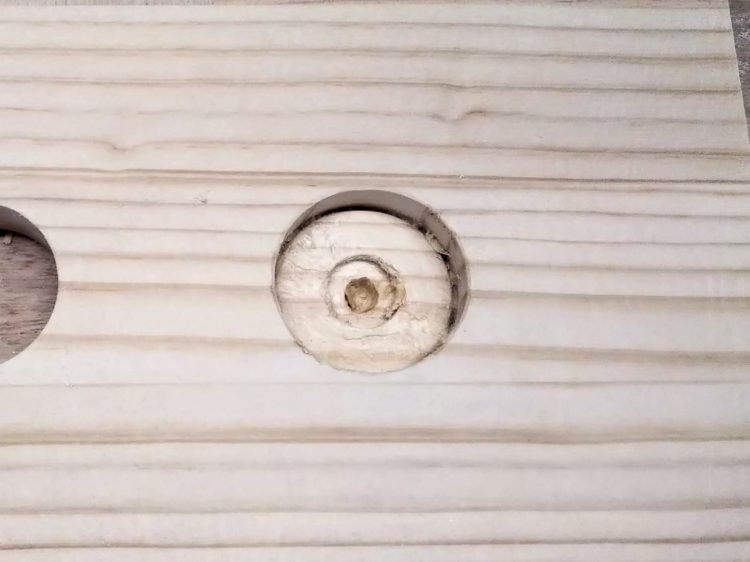
小径穴用自在錐による止め穴
先端錐の形状が三角錐の場合、止め穴加工が可能になります。
大径穴用自在錐
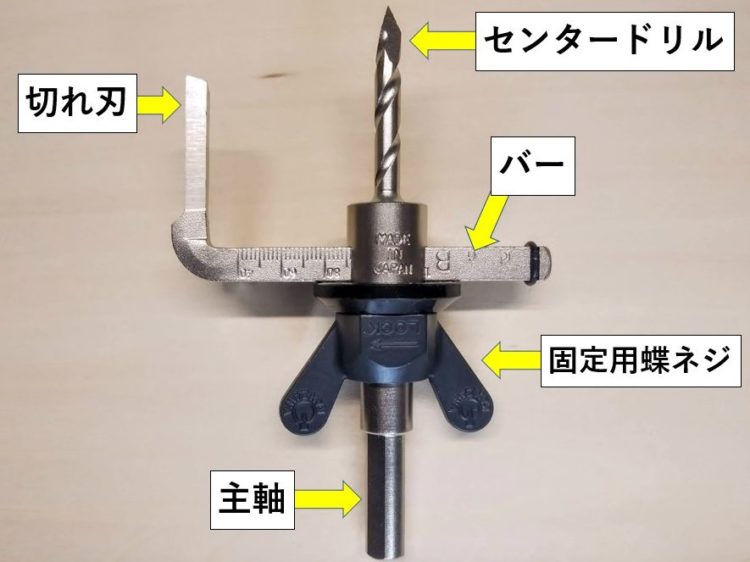
片刃タイプ・各部名称
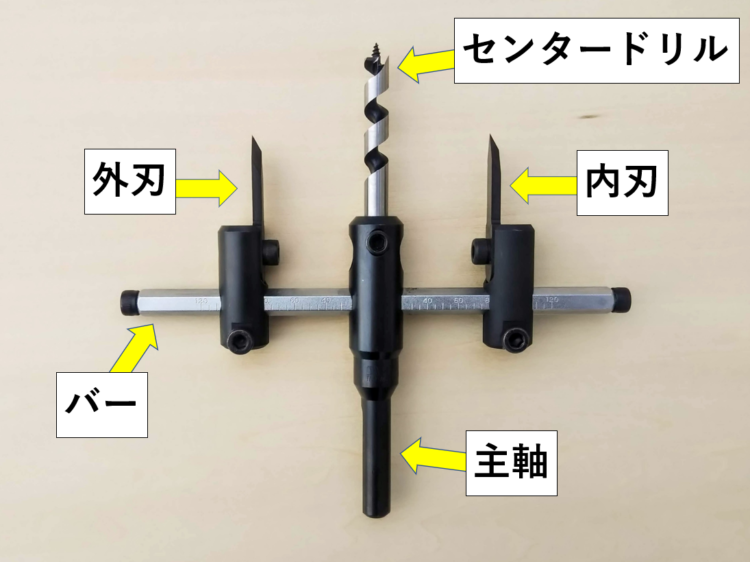
両刃タイプ・各部名称
大径穴用自在錐には、切り刃が一つだけの ”片刃タイプ” と二つある ”両刃タイプ” があります。
片刃タイプは、主軸のセンタードリル、穴径の目盛りが印してあるバーと一体化した切れ刃からなり、バーをスライドさせることにより切削する穴の径を変える仕組みになっています。
両刃タイプは、主軸のセンタードリルと両サイドの外刃・内刃からなり、両サイドの刃をバーに沿ってスライドさせることで切削する穴の径を変える仕組みになっています。
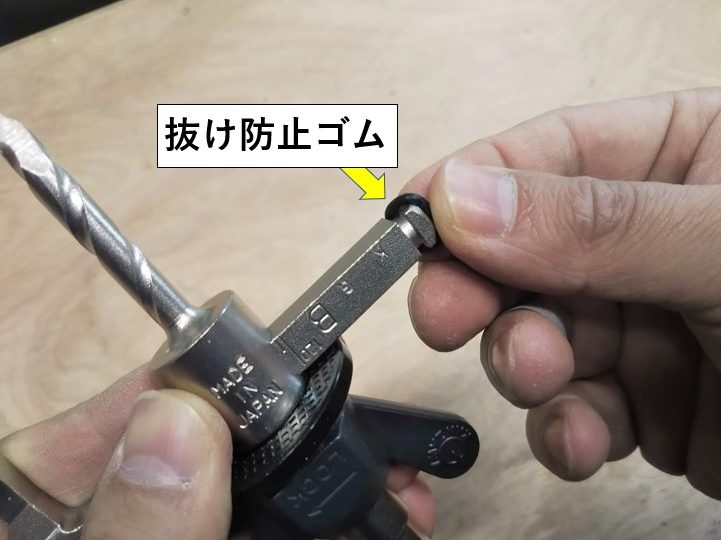
抜け防止ゴムを外す
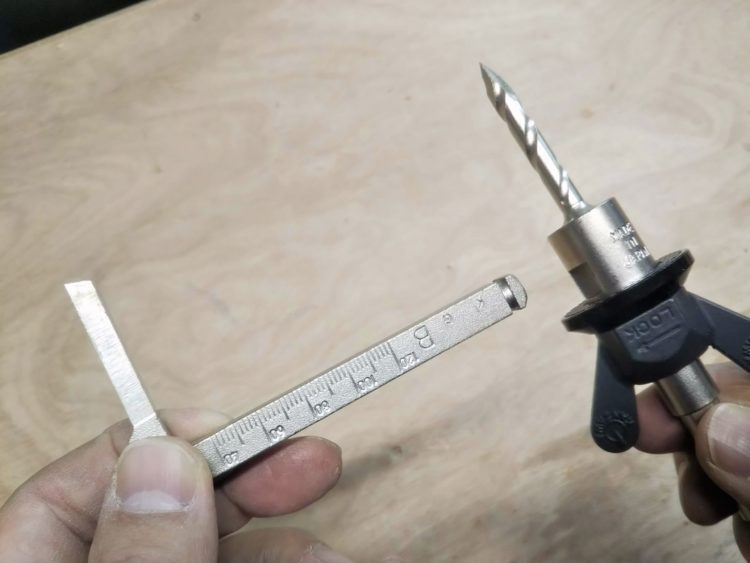
刃の交換が可能
片刃タイプは、バーの抜け防止ゴムを外すと、バー一体型の切れ刃交換(替え刃式)が出来ます。
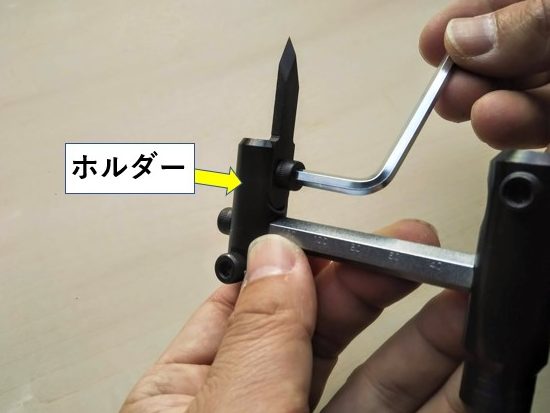
刃をホルダーから外す
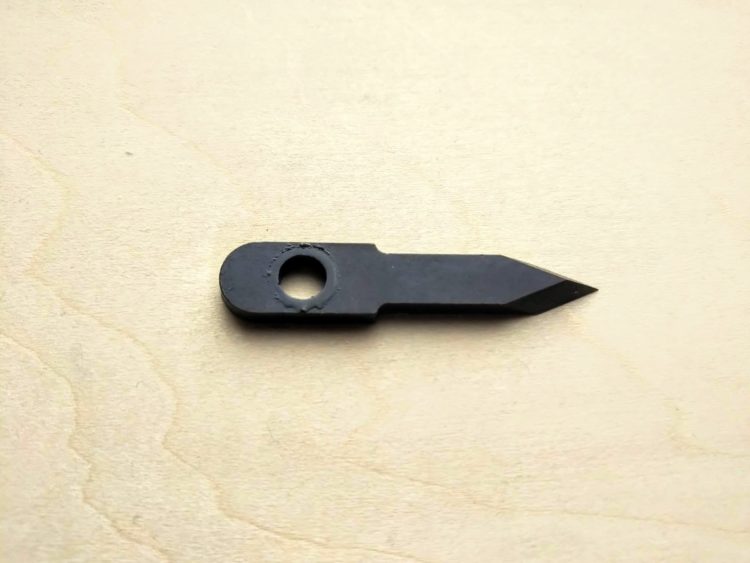
外刃用替え刃
両刃タイプは、両サイドの刃をホルダーから外すことが出来、替え刃式になっています。
内刃・外刃それぞれに専用の替え刃があるので注意が必要です。
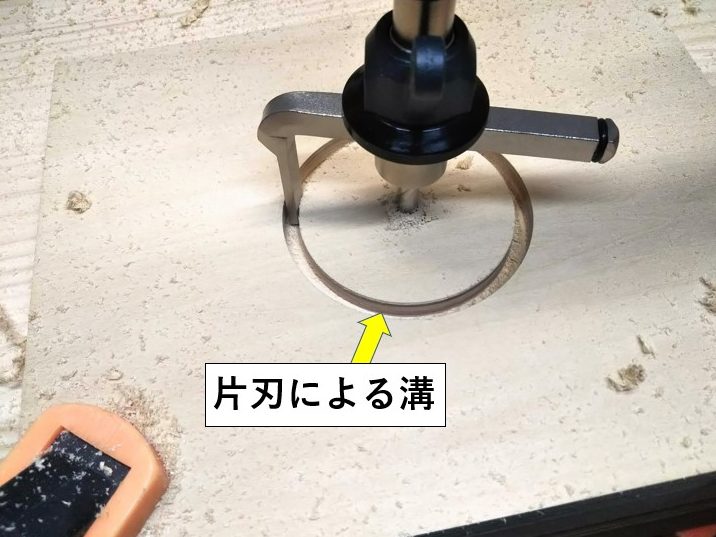
片刃による溝
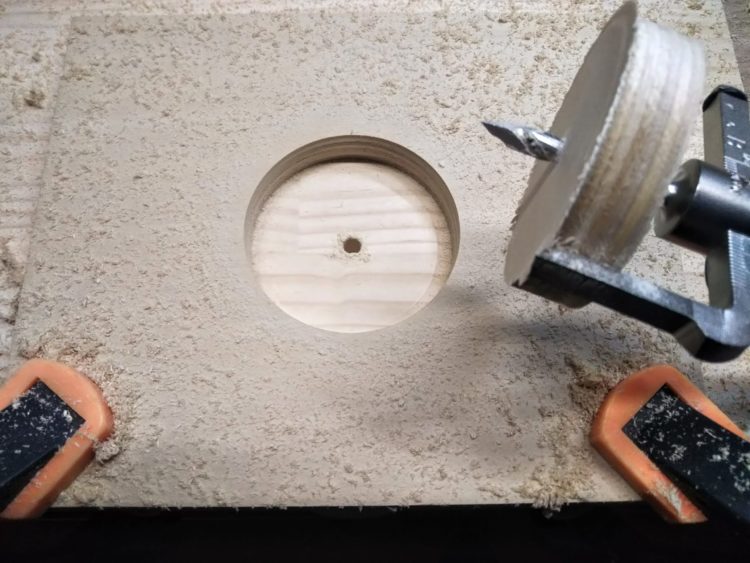
片刃タイプによる穴あけ
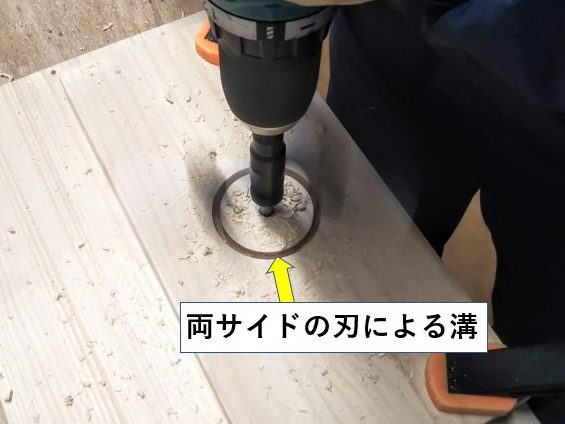
両サイドの刃による溝
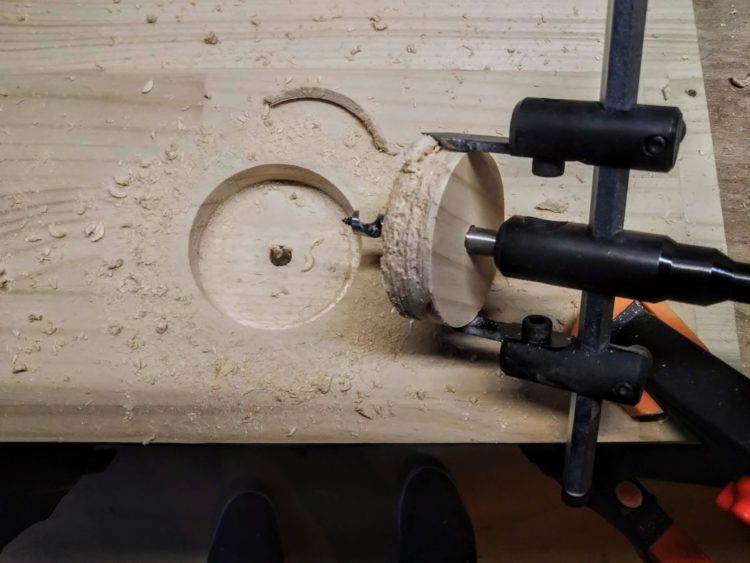
両刃タイプの穴あけ
穴あけ方式は、片刃タイプは片刃・両刃タイプは両刃で、切削穴の外周に溝を掘り、穴の中をくり抜く形になります。
両タイプ共に、止め穴加工は出来ません。
自在錐(自由錐)の使い方
小径穴用自在錐(木材・石膏ボード用)
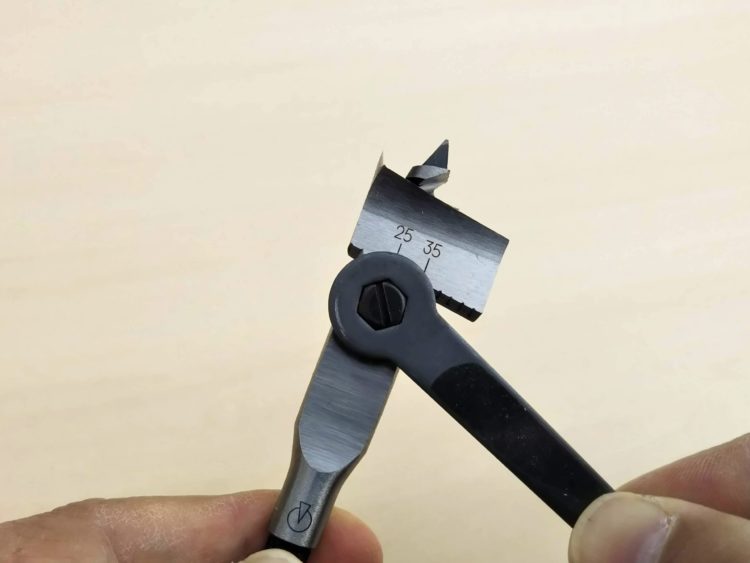
調整ネジをゆるめる
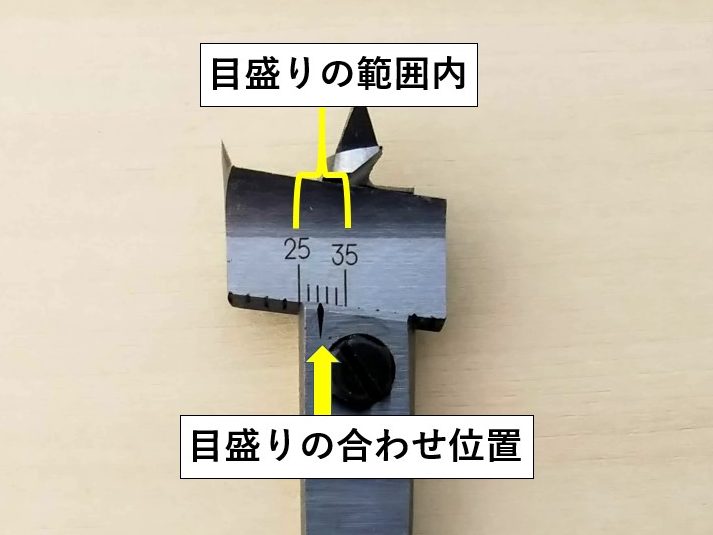
目盛りを合わせる
付属のスパナで調整ネジをゆるめ、可動刃をスライドさせます。
目盛りあわせ位置に可動刃の目盛りを合わたら、調整ネジを締めて固定します。
最大目盛り以上にセットした場合、可動刃が外れる可能性があるので、可動刃のセット位置は必ず目盛りの範囲内になるようにします。
自在錐には、適応材・穴のサイズ・板厚、使用できる電動ドライバーの種類が決められています。
適応・適合外の場合は、切削・使用が出来ないので注意が必要です。
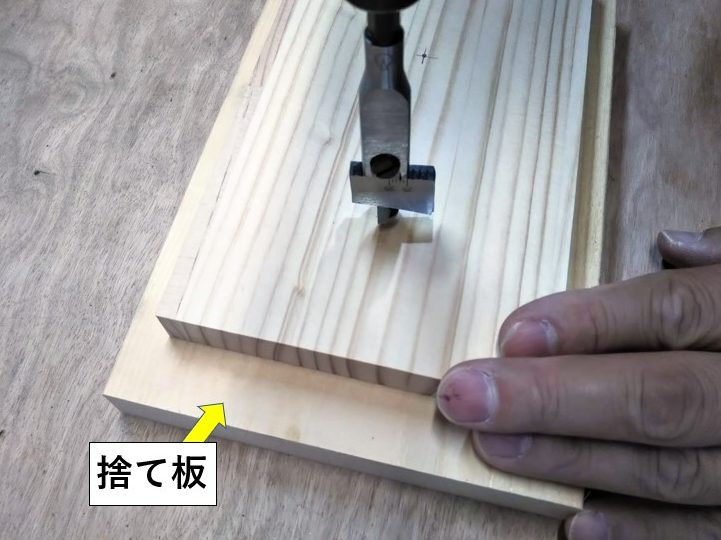
中心錐を穴のセンターに合わせる
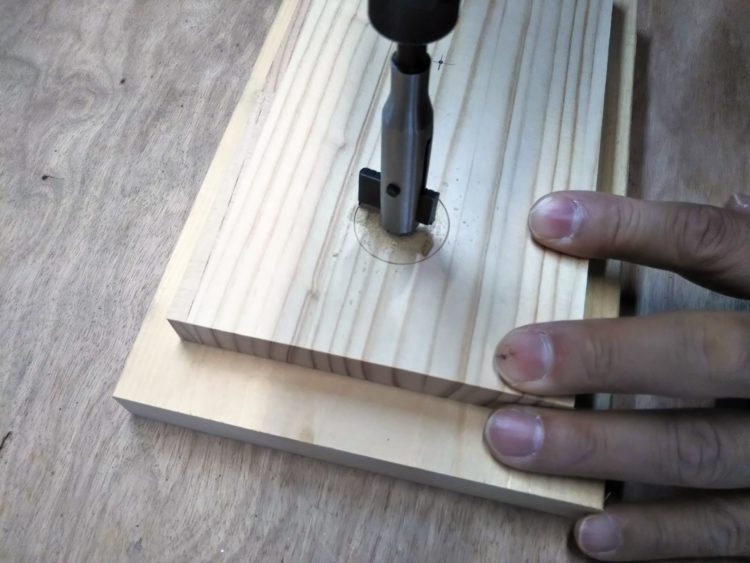
けづめによる穴外周のけがき
使用に適合した電動ドライバーへ自在錐を装着し、加工材の下に捨て板を敷き、貫通穴をあけていきます。
中心錐を穴のセンターに合わせ、けづめが切削穴の外周をけがく深さまで電源のオン・オフを繰り返しながら、垂直方向へ慎重に掘り進めます。
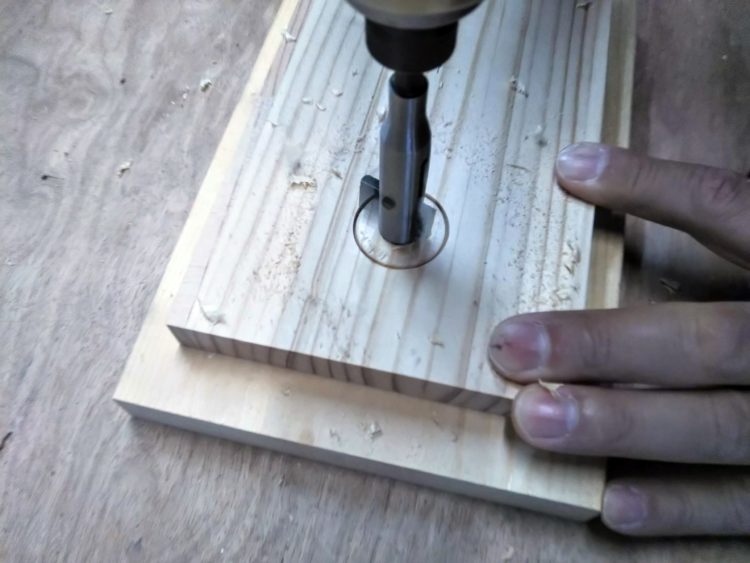
先端錐・可動刃による切削
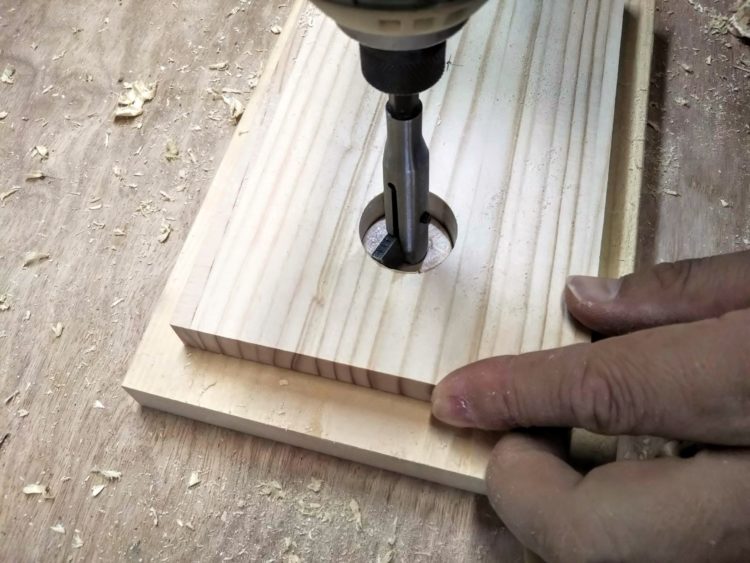
穴あけ完了
きれいなけがき線が引けたら、先端錐・可動刃全体による切削が始まる深さまで電源のオン・オフを繰り返しながら、さらに掘り進めます。
(錐全体での切削が始まる時は、切削抵抗が強くなるので、電動ドライバーをしっかり保持しておきます)
自在錐全体での切削(木くずが巻き上がり始めたら)が始まったら、回転速度を上げ掘り進めます。
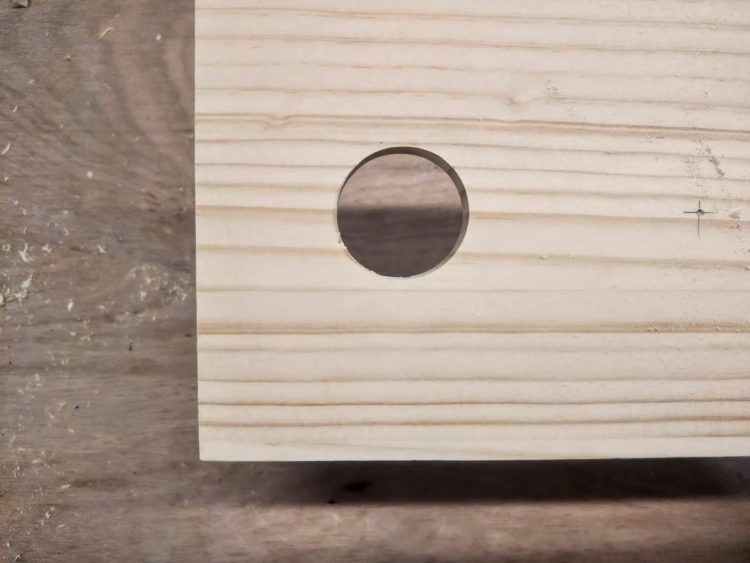
貫通穴
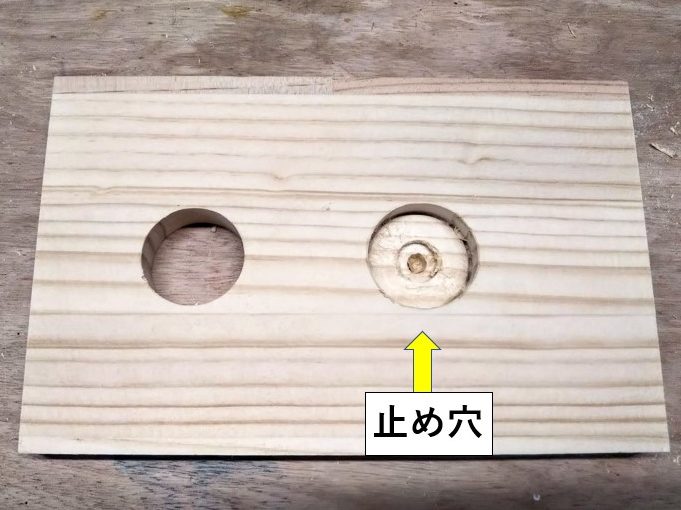
貫通穴と止め穴
きれいな貫通穴をあける事が出来ます。
前述したように、先端錐の形状が三角錐の場合止め穴加工が可能ですが、穴底がボアビットを使用した時ほどのきれいな仕上がりにはなりません。
(ボアビットの使用例は、スライド丁番とは?取り付け方と種類についてお教えします。 ボール盤の構造と使い方とは? の記事を参照して下さい)
可動刃の目盛りはあくまで目安なので、正確な寸法を必要とする穴あけの場合は、試し穴で寸法を測り、可動刃の位置を調整・固定する必要があります。
大径穴用自在錐(木材・石膏ボード用)
片刃タイプ
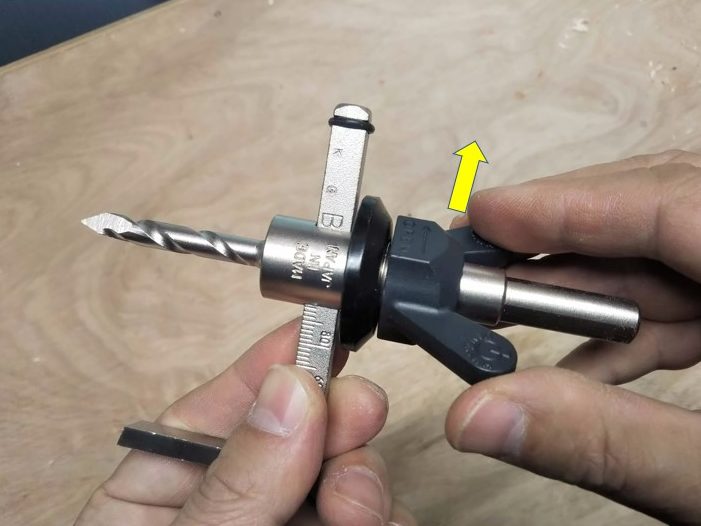
蝶ネジを右に回す
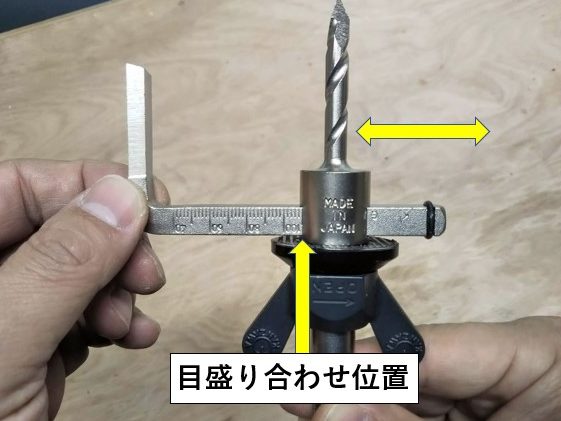
目盛りを合わせる
蝶ネジを右に回して緩め、バーを移動させます。
目盛り合わせ位置(軸の切れ刃側)にバーの目盛りを合わせたら、蝶ネジを左に回して固定します。
最大目盛り以上にセットした場合、バー(切れ刃)が外れる可能性があるので、バー(切れ刃)のセット位置は必ず目盛りの範囲内になるようにします。
バーの目盛りはあくまで目安なので、正確な寸法を必要とする穴あけの場合は、試し穴で寸法を測り、バー(切れ刃)の位置を調整・固定する必要があります。
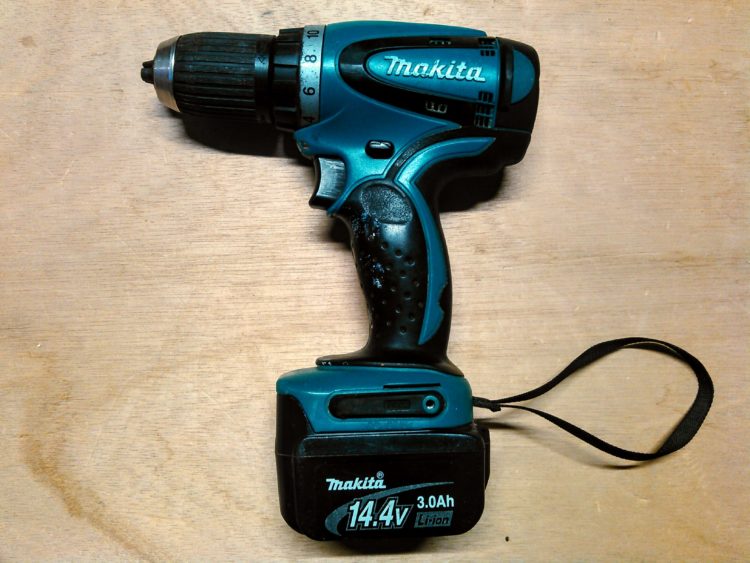
ドリルドライバー
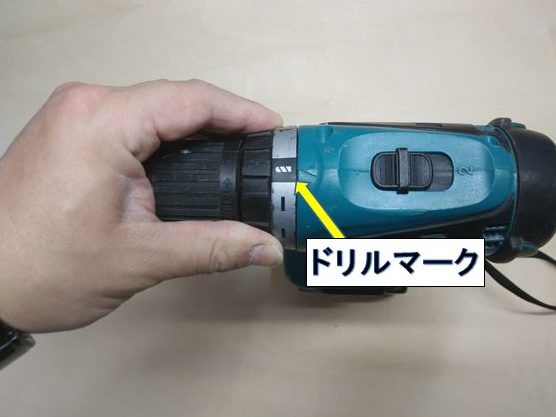
ドリルマーク
自在錐には、適応材・穴のサイズ・板厚、使用できる電動ドライバーの種類が決められています。
適応・適合外の場合は、切削・使用が出来ないので注意が必要です。
今回使用する片刃タイプの自在錐は、インパクトドライバーでの使用が出来ません。
ドリルドライバー(ドリルマークにセット)に装着し、指定された適正回転数で穴あけを行います。
錐の回転方向は、必ず正回転(時計回り)で使用します。(逆回転での使用は出来ません。)
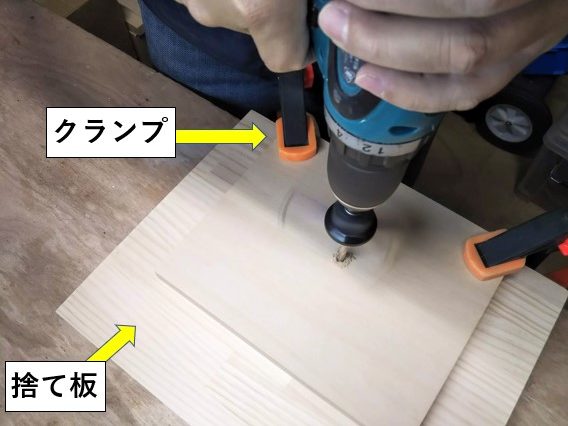
加工材をクランプで固定
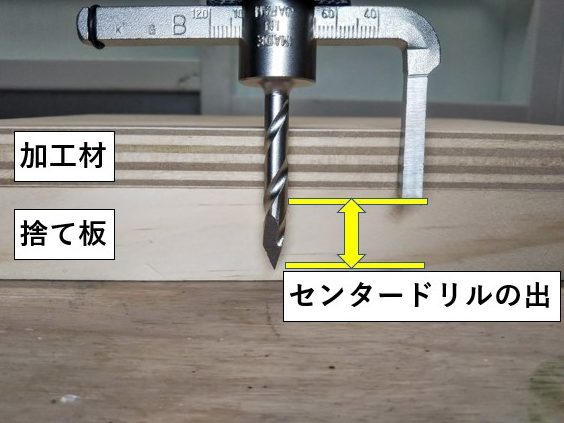
捨て板の厚み
加工材の下に捨て板を敷き、作業台等にクランプで固定したら、センタードリルを穴のセンターに合わせ切削していきます。
(切削時の錐の抵抗力が強いので、加工材を手で保持して穴あけをするのは危険です。必ず、クランプで固定して作業するようにします。)
切れ刃よりセンタードリルの先端が出ているので、加工材に穴があいた時にセンタードリルが捨て板を貫通しないように、厚みを考慮する必要があります。
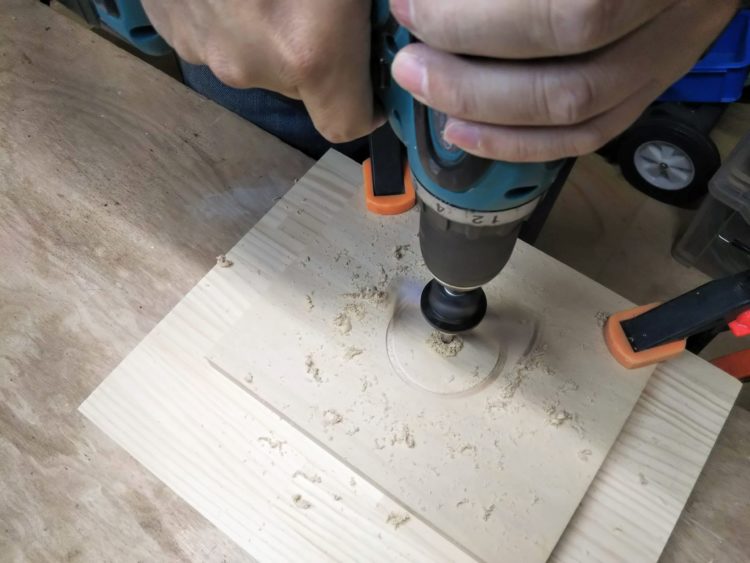
徐々に下へ押し込む
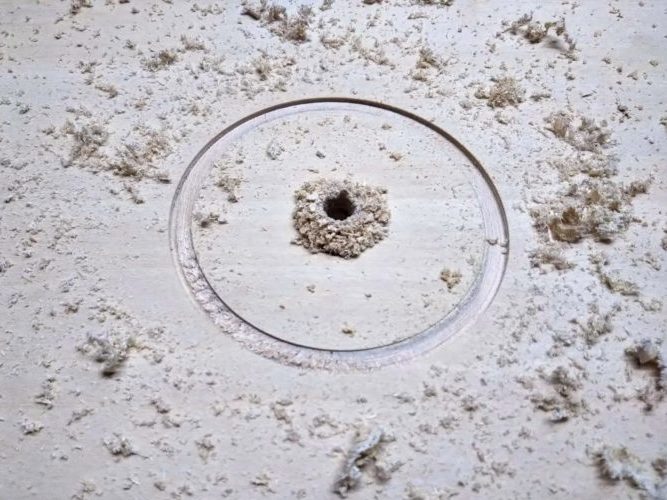
切れ刃による溝
切れ刃での切削が始まる深さまで、徐々に掘り進めます。
切れ刃での切削が始まると切削抵抗が大きくなります。
その時に切削量を多くしてしまうと、切れ刃による溝が荒れてしまい、綺麗な円の穴をあける事が難しくなります。
切れ刃の切削始めは、切削量を少なくし、綺麗な溝をほる様にします。
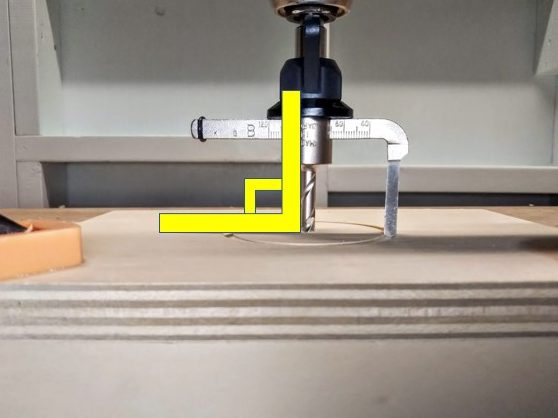
加工材と自在錐が垂直になるようにする
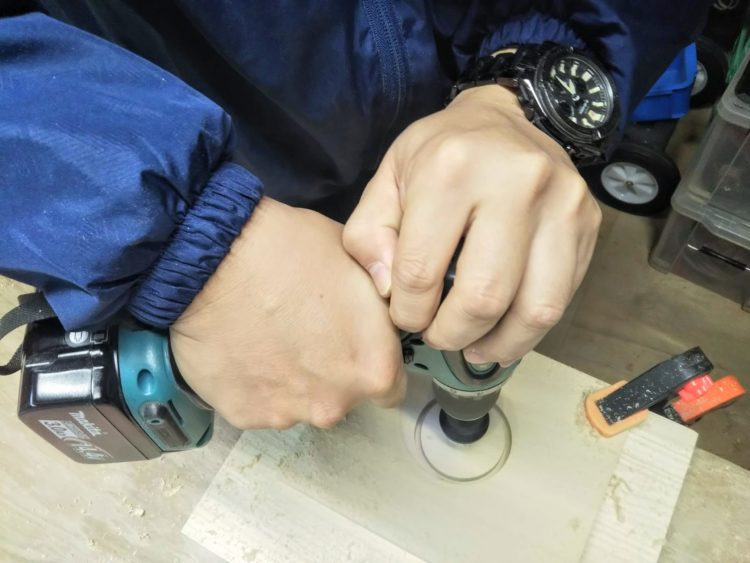
ドリルドライバーを両手で保持
自在錐が加工材に対して傾斜していると、切削抵抗が強くなり危険(ドリルドライバーの保持が困難になる・刃の破損がおこる)です。
切削時は、加工材に対して自在錐が常に垂直になる様にし、なるべくドリルドライバーは両手で保持して操作します。
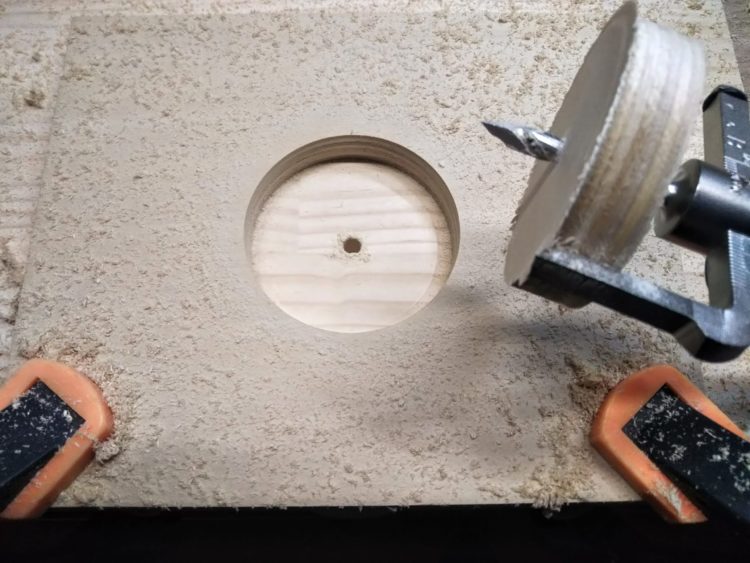
片刃タイプによる穴あけ
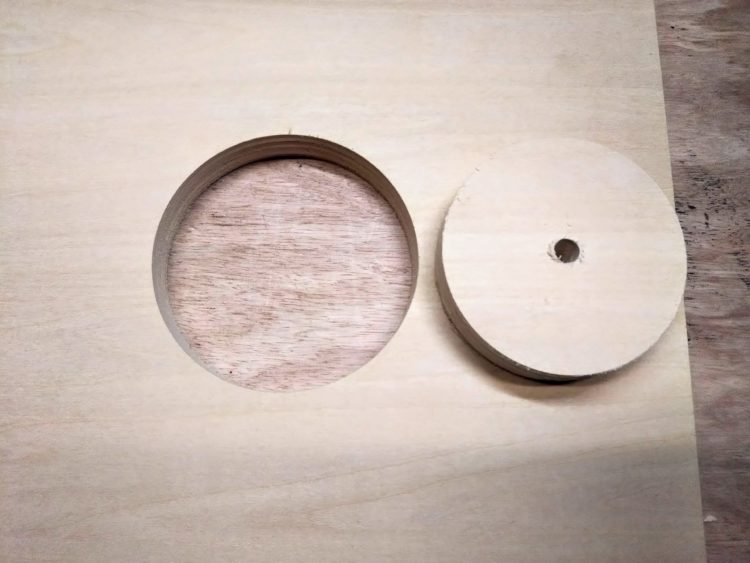
片刃タイプによる穴あけ
加工材をくり抜いた貫通穴をあける事が出来ます。
両刃タイプ
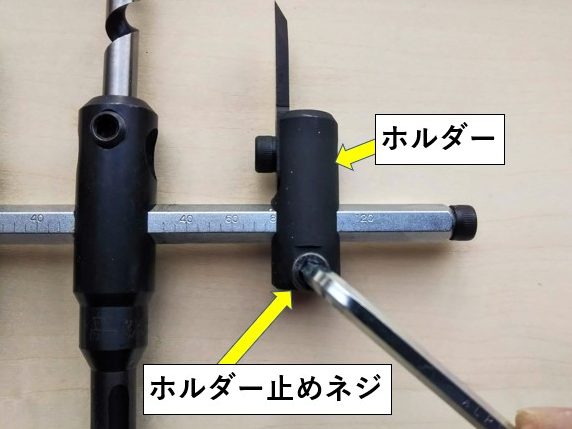
ホルダー止めネジを緩める
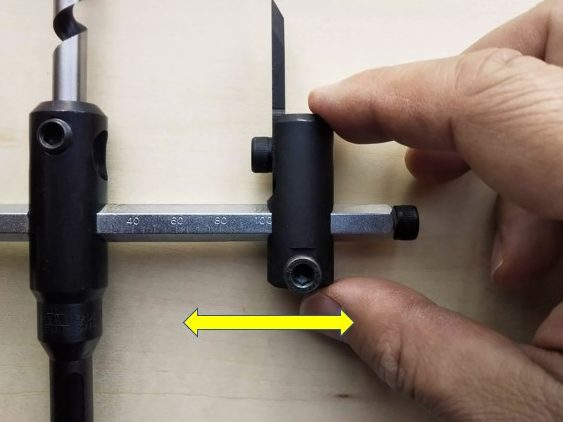
ホルダーを移動し穴径を調整
ホルダーをバーに固定している止めネジを、六角棒レンチで緩めます。
左右のホルダーを移動し、穴径を調整します。
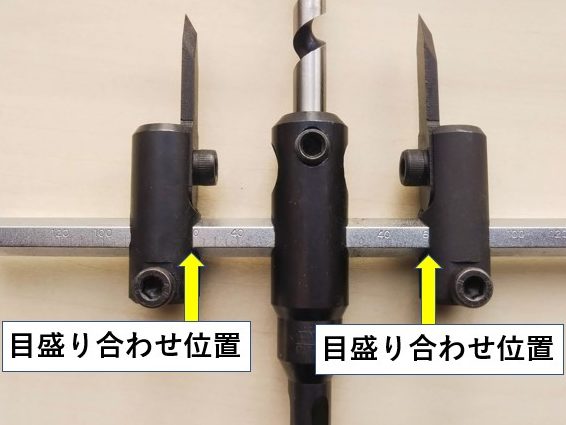
ホルダー内側をバー目盛りに合わせる
バーの目盛りにホルダーの目盛り合わせ位置(左右のホルダー共に軸側)を合わせ、止めネジを締め固定します。
左右のホルダーは共に、バーの目盛り数値が同じになる位置に固定します。
バーの目盛りはあくまで目安なので、正確な寸法を必要とする穴あけの場合は、試し穴で寸法を測り、ホルダーの位置を調整・固定する必要があります。
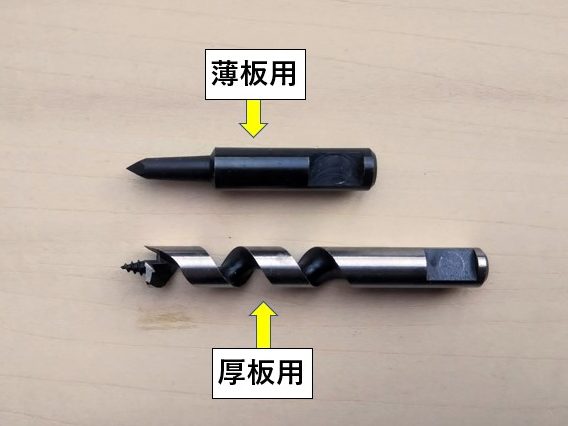
薄板用と厚板用のセンタードリル
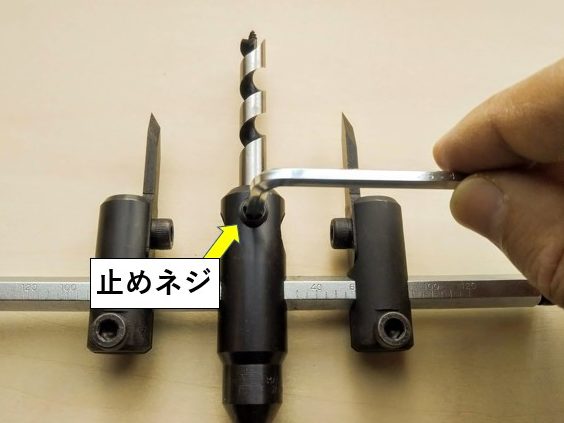
止めネジを緩める
センタードリルには、”薄板用” と ”厚板用” があり、加工材の厚みによって交換して穴あけを行います。
主軸のセンタードリル止めネジを緩めると交換することが出来ます。
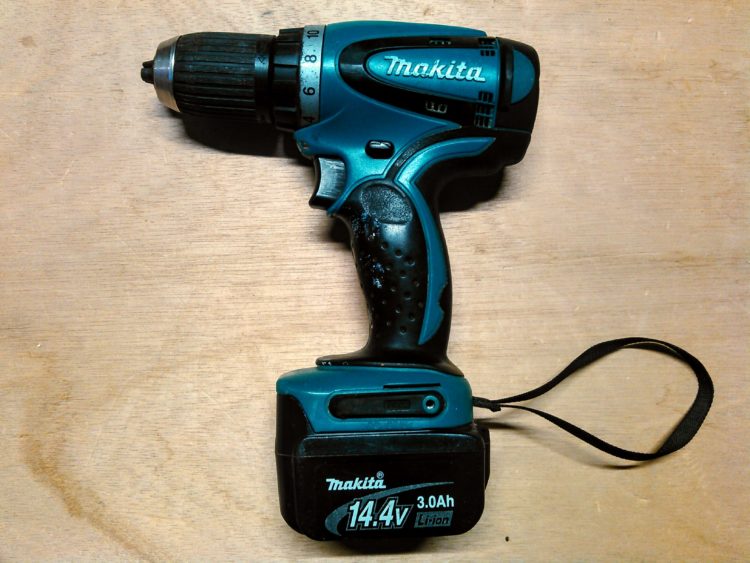
ドリルドライバー
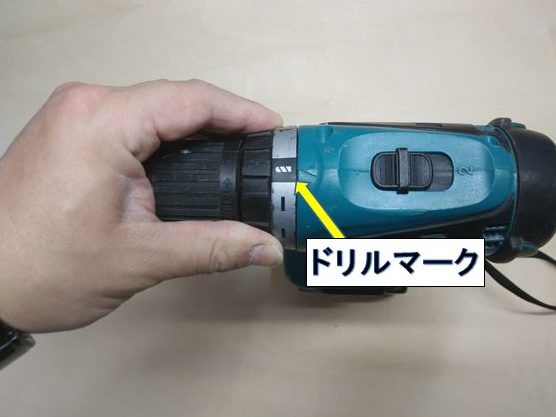
ドリルマーク
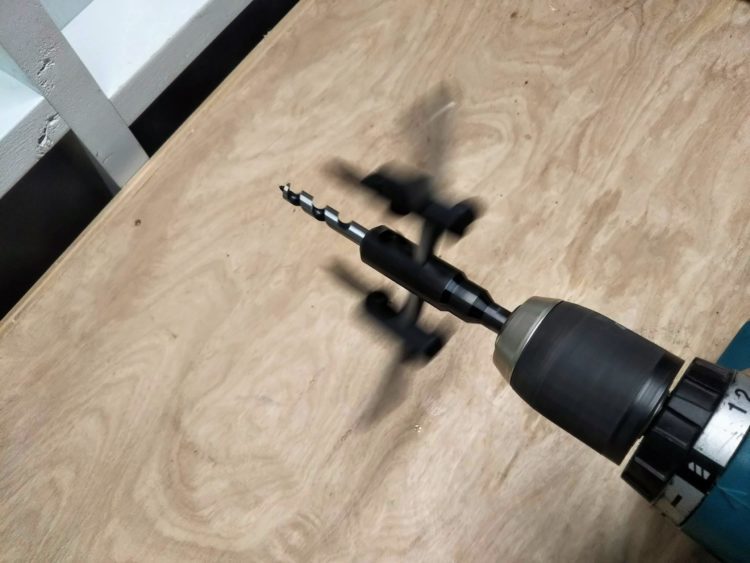
試運転
自在錐には、適応材・穴のサイズ・板厚、使用できる電動ドライバーの種類が決められています。
適応・適合外の場合は、切削・使用が出来ないので注意が必要です。
今回使用する両刃タイプの自在錐が使用できる電動工具は、回転数が毎分1500回転以下のドリルドライバーになります。
自在錐の各ネジがしっかりと締まっているか確認したら、ドリルドライバー(ドリルマークにセット)に装着します。
更に、実際に自在錐を回転させてみて、不具合がないか確認しておきます。
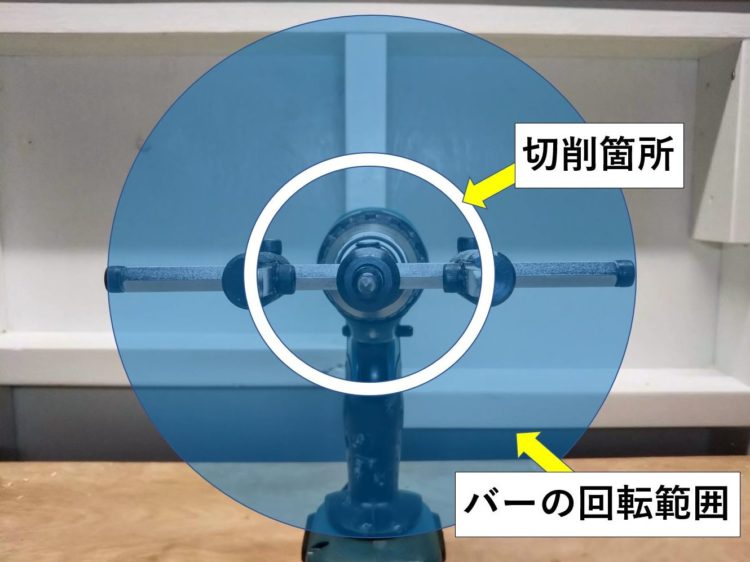
バーの回転範囲
両刃タイプの自在錐の場合、切削箇所よりバーの回転外周が外側になります。
切削時、バーの回転範囲に障害物(手やクランプなど)があると接触して危険です。
作業前に必ずバーの回転範囲の安全を確認してください。
薄板(板厚・5.5mm)の穴あけ
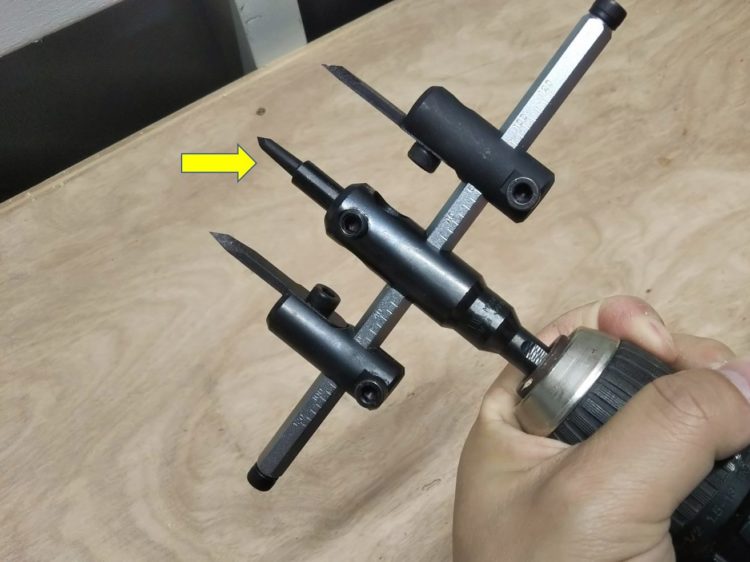
薄板用センタードリルをセット
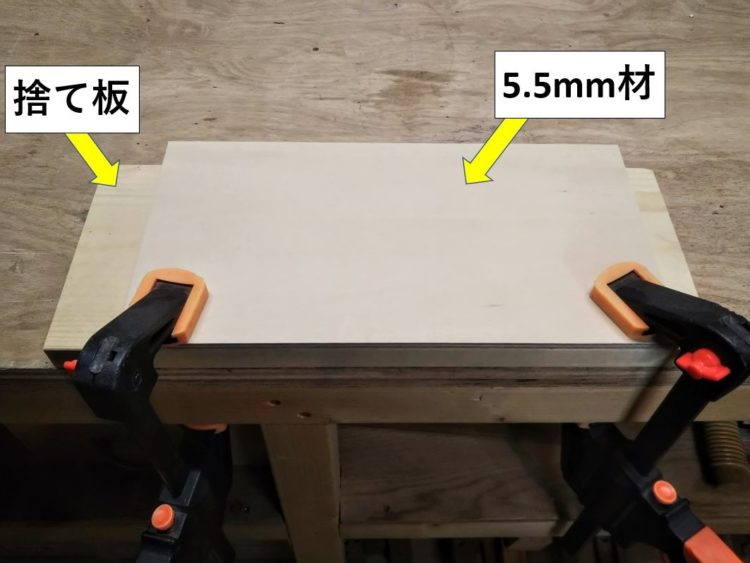
捨て板を敷いて加工材を固定
薄板用センタードリルをセットし、5.5mm材に穴あけを行います。
加工材の下に捨て板を敷いて、クランプで作業台に固定します。
(片刃タイプ同様切削抵抗が大きいので、手による加工材の保持はせず、必ずクランプ等で固定してから作業します。)
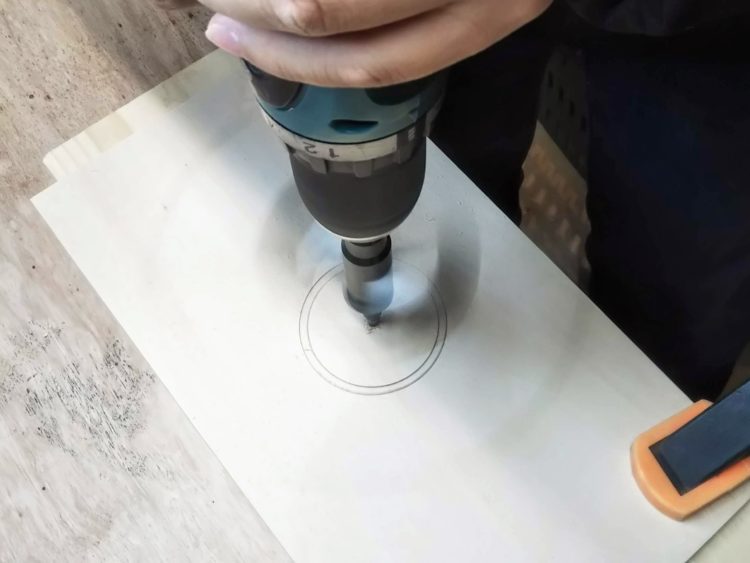
外刃・内刃による切削開始
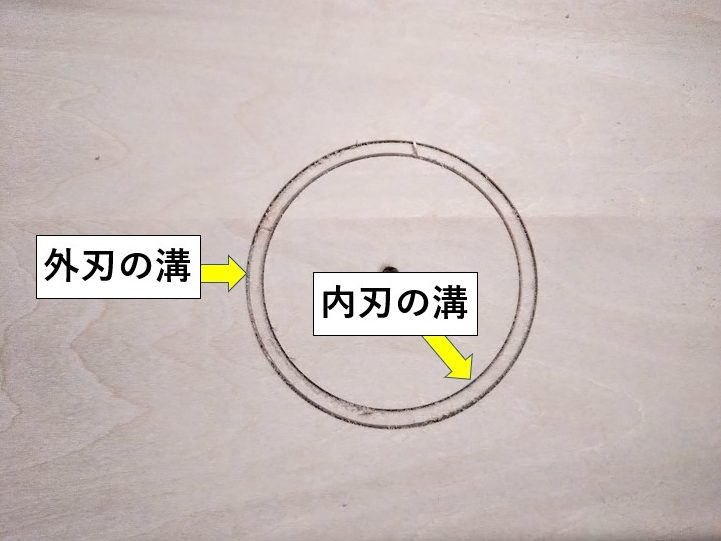
外刃と内刃による溝
センタードリルを穴のセンターに合わせたら、外刃・内刃による切削が始まる深さまで、徐々に掘り進めます。
外刃・内刃による切削が始まると切削抵抗が大きくなります。
その時に切削量を多くしてしまうと、外刃・内刃による溝が荒れてしまい、綺麗な円の穴をあける事が難しくなります。
外刃・内刃による切削始めは、切削量を少なくし、綺麗な溝をほる様にします。
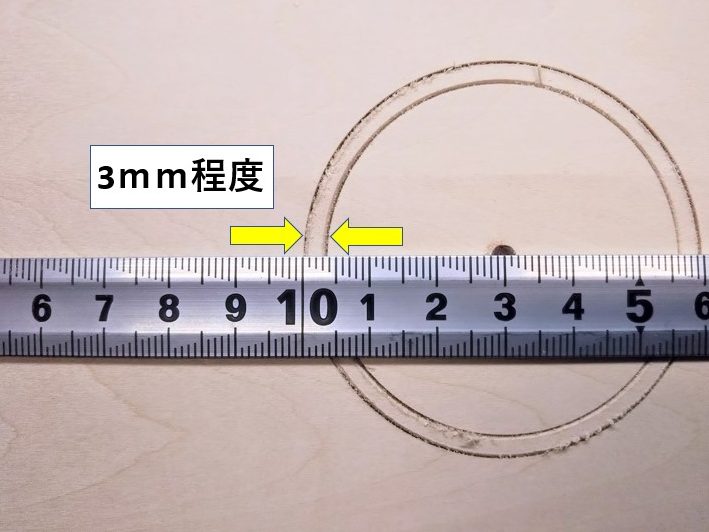
外刃と内刃の溝間隔
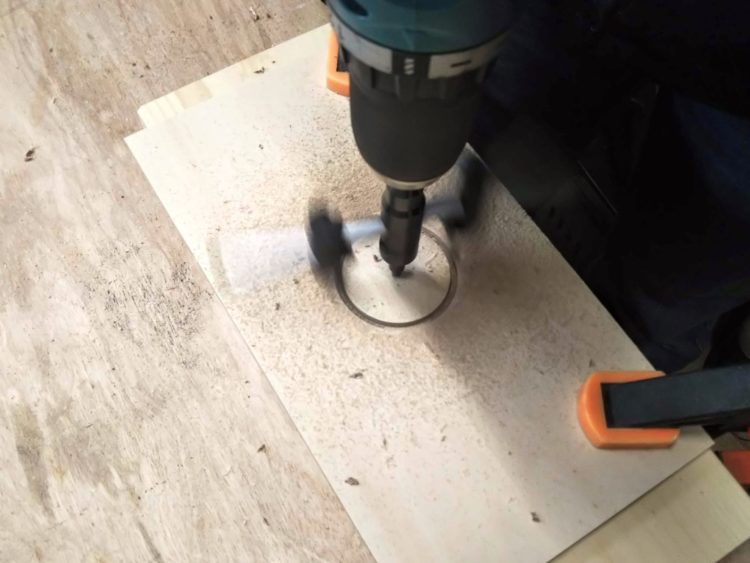
垂直方向に切削する
外刃・内刃による切削始めの溝がほれたら、一旦切削を止め、外刃と内刃の溝間隔を計測します。
適切な間隔(3mm程度)になっているか確認し、再び切削を開始します。
自在錐が加工材に対して傾斜していると、切削抵抗が強くなり危険(ドリルドライバーの保持が困難になる・刃の破損がおこる)です。
切削時は、加工材に対して自在錐が常に垂直になる様にし、なるべくドリルドライバーは両手で保持して作業します。
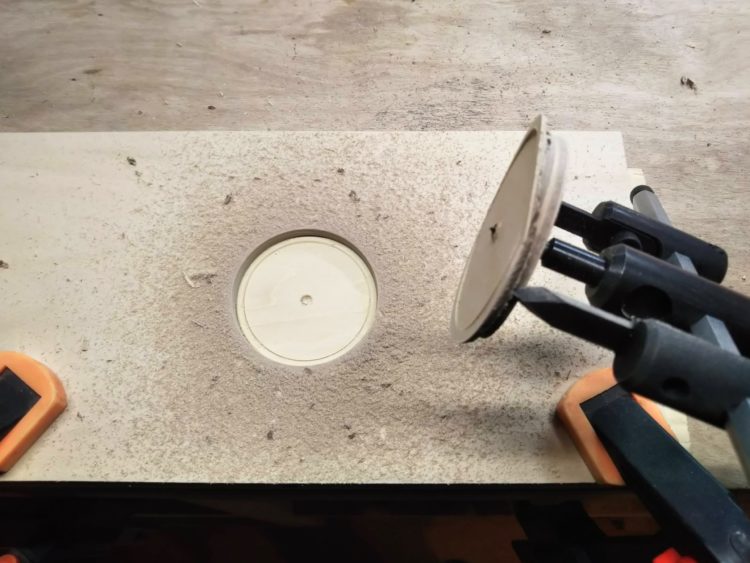
薄板の穴あけ完了
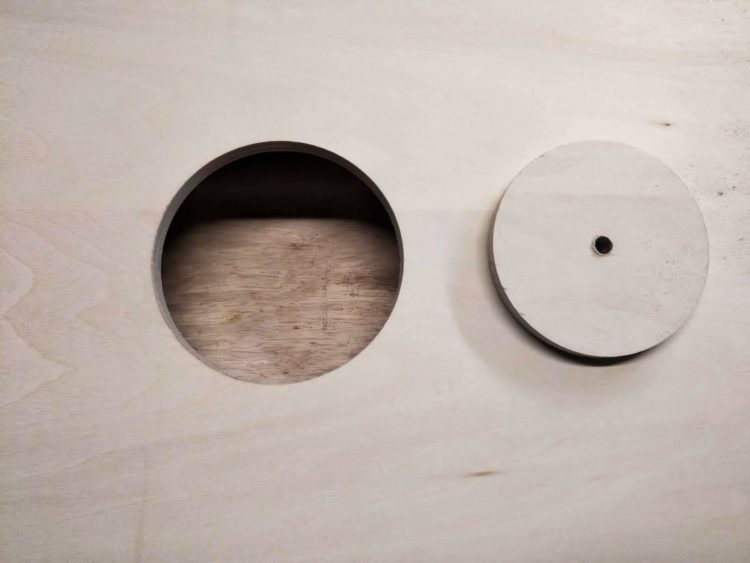
薄板の穴あけ完了
薄板をくり抜いたきれいな貫通穴をあける事が出来ます。
厚板(板厚・25mmまで)の穴あけ
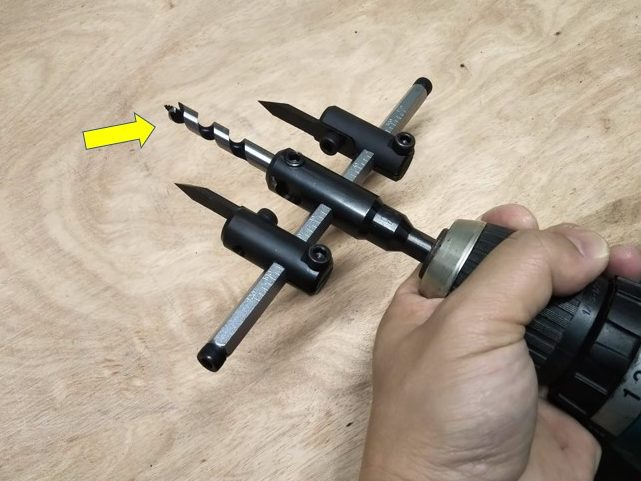
厚板用センタードリルをセット
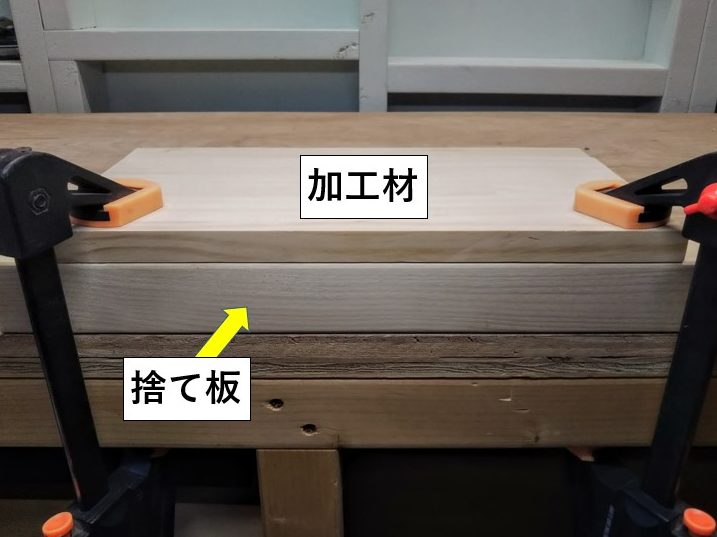
捨て板を敷いて加工材を固定
厚板用センタードリルをセットし、板厚15mmの加工材に穴あけを行います。
加工材の下に捨て板を敷いて、クランプで作業台に固定します。
厚板用のセンタードリルは薄板用に比べ、外刃・内刃よりドリルの先端がかなり出ています。
加工材に穴があいた時(外刃・内刃が捨て板に到達時)にセンタードリルが捨て板を貫通しないように、厚みを考慮する必要があります。
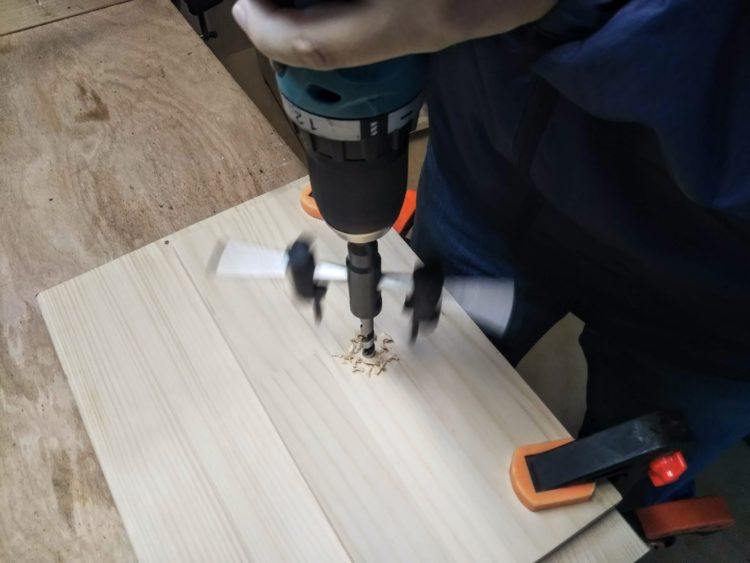
センタードリルによる切削開始
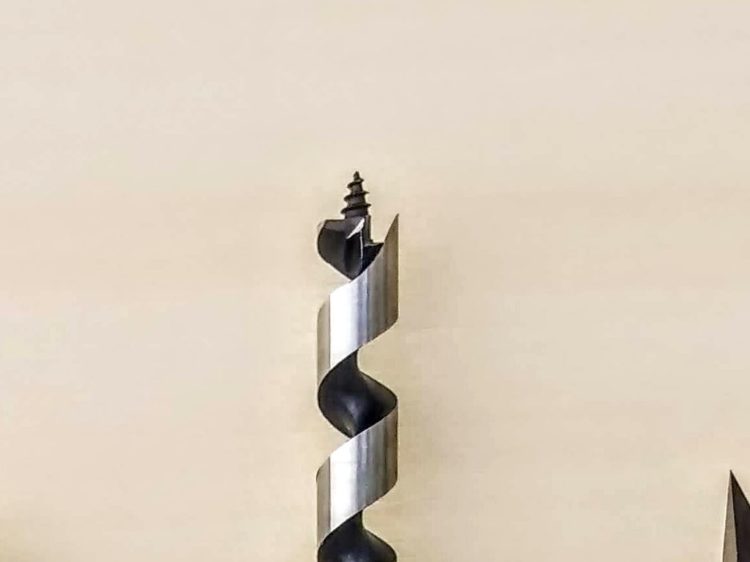
センタードリルの先端がネジ形状
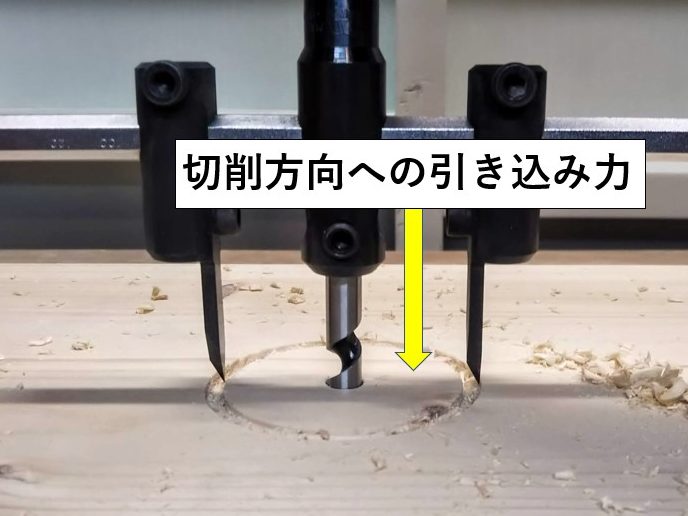
切削方向への引き込み力が強い
穴のセンターにセンタードリルを合わせ、切削を開始します。
厚板用のセンタードリルの先端は、ネジ形状になっており、切削方向への引き込み力が非常に強いです。
軽くドリルドライバーを押し込んだだけでも、外刃・内刃の切削深さまで一気に掘り下げてしまいます。
外刃・内刃の切削が始まると切削抵抗が非常に強くなり、そのままの引き込み力のままだと自在錐・ドリルドライバーのコントロールが難しくなります。
ドリルドライバーを切削方向と逆方向に若干引き揚げながら、徐々に深く切削していきます。
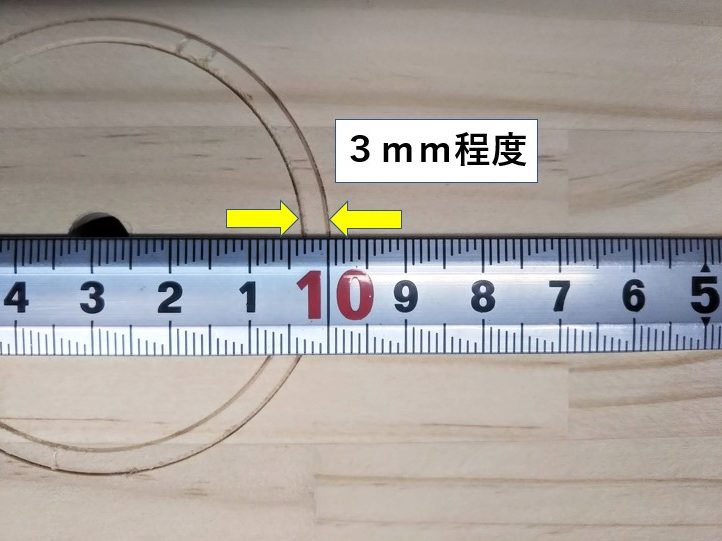
外刃・内刃の溝間隔
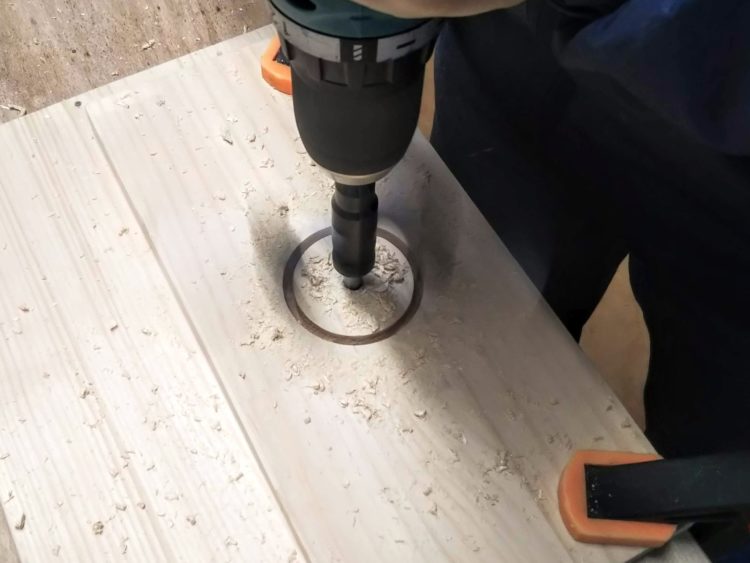
深く掘り進める
外刃・内刃の切削が始まったら、一旦切削を止め、溝間隔を計測します。
外刃・内刃の溝間隔が3mm程度であることを確認したら、加工材と自在錐の垂直を保ちながら更に深く掘り進めます。
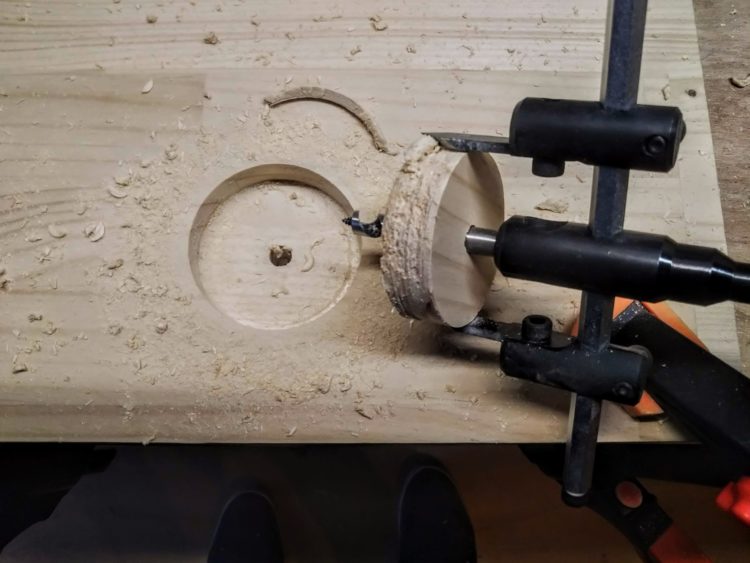
厚板の穴あけ完了
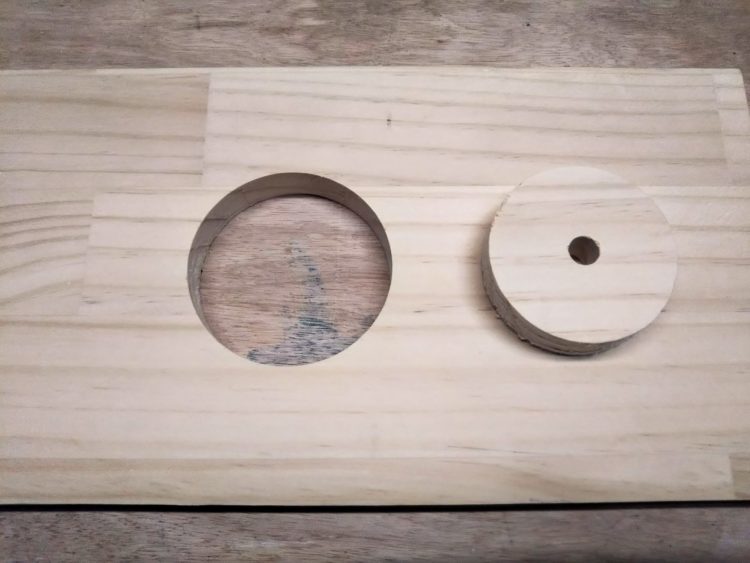
厚板の穴あけ完了
厚板(15mm厚)に貫通穴をきれいにくり抜くことが出来ます。
今回使用した自在錐では、加工材片面からの最大切削深さは、25mmまでとなります。
厚板(板厚・25mm以上)の穴あけ
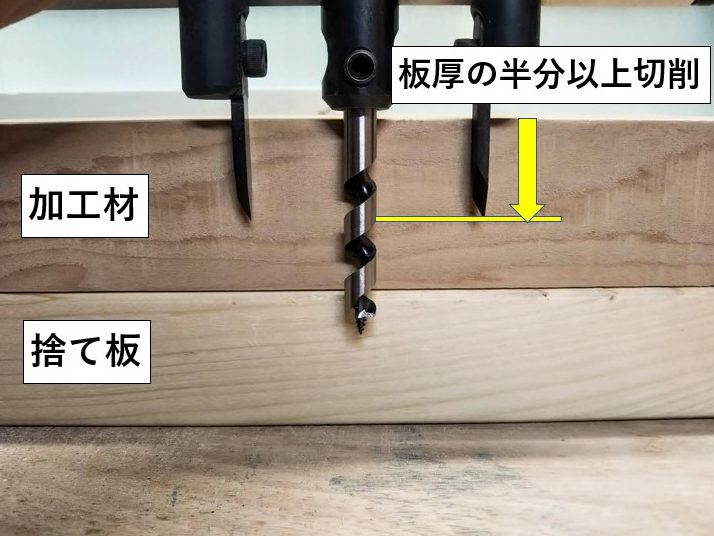
片面から加工材厚の半分以上切削する
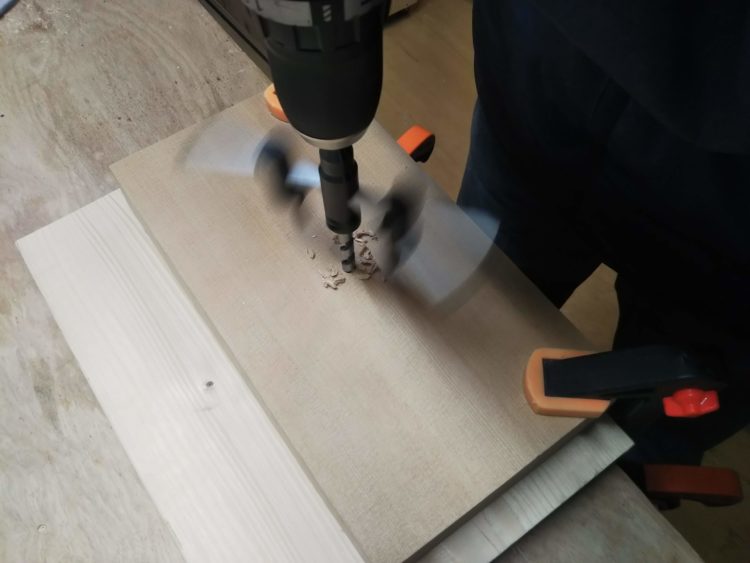
センタードリルによる切削開始
今回使用している両刃タイプの自在錐は、最大50mm厚の材に穴あけが可能です。
(加工材片面からの最大切削深さは25mm)
25mm厚以上の材に穴あけするには、片面から加工材の厚みの半分以上まで切削した後(センタードリルの貫通)、加工材を裏返しセンタードリルの貫通穴をガイドに切削し穴を貫通させる方法になります。
実際の加工材に自在錐をあてがい、材の厚み・半分以上切削した場合のセンタードリル・外刃・内刃の位置を確認しておきます。
穴のセンターにセンタードリルを合わせ、切削を開始します。
前述の厚板(25mmまでの板厚)の穴あけ加工と同じ手順で切削していきます。
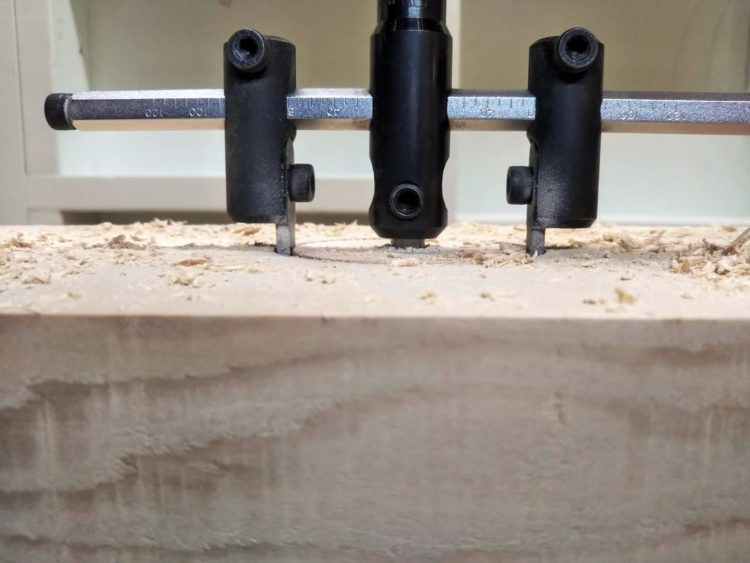
板厚の半分以上切削する
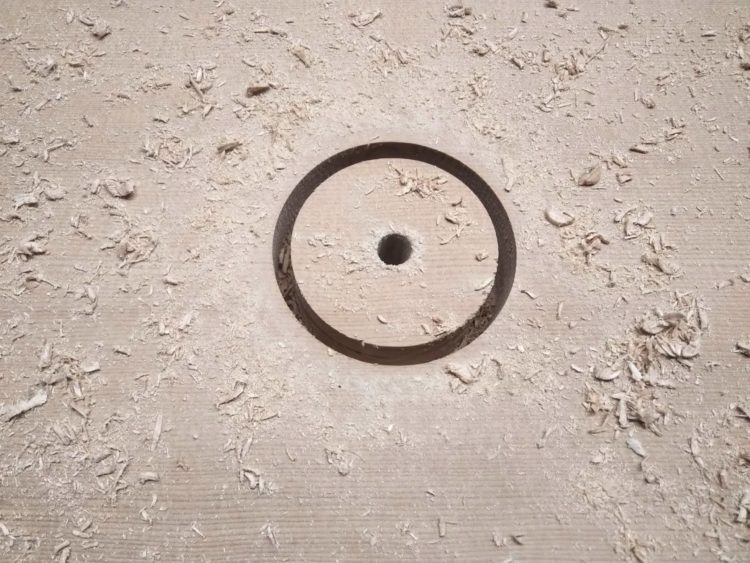
片面から板厚の半分以上の切削完了
材の厚み・半分以上の位置まで、溝を掘り下げます。
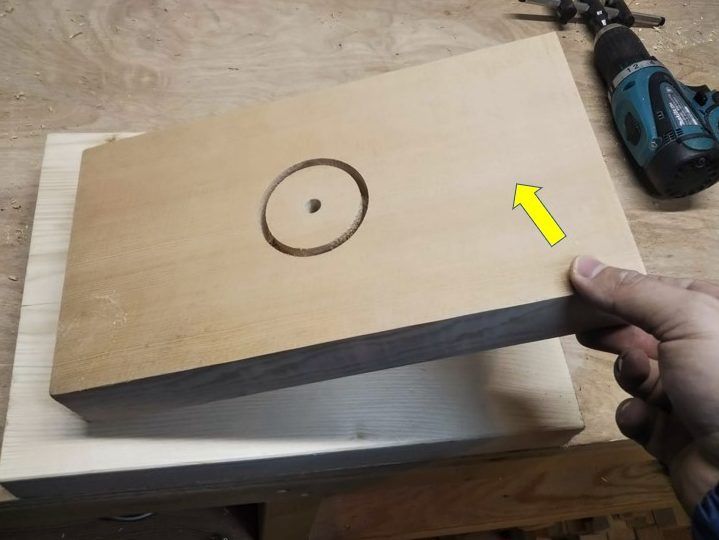
加工材をひっくり返す
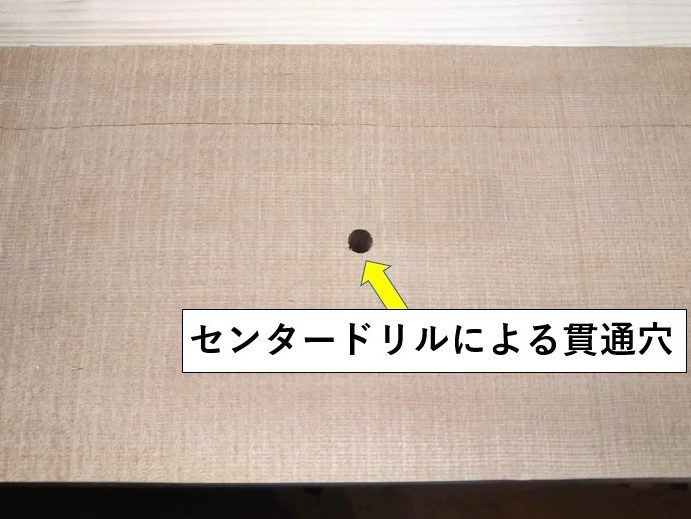
センタードリルによる貫通穴
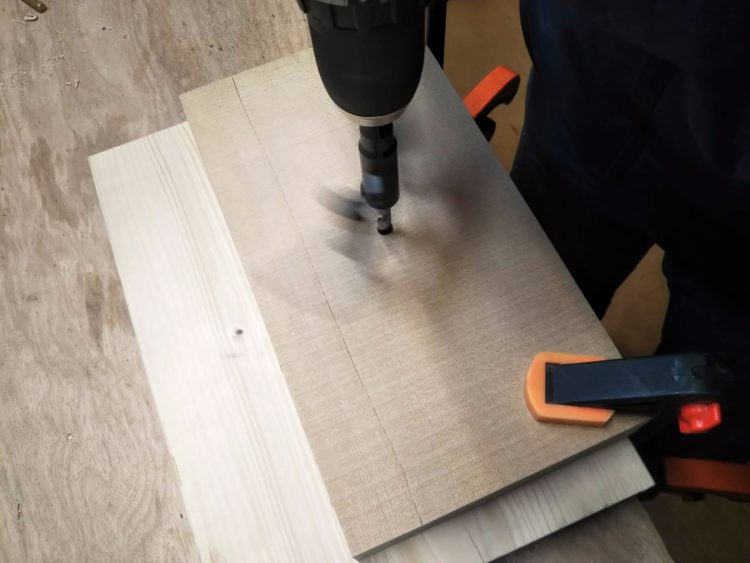
貫通穴にセンタードリルを差し込み切削する
加工材をひっくり返すと、センタードリルによる貫通穴が現れます。
貫通穴にセンタードリルを差し込み、切削していきます。
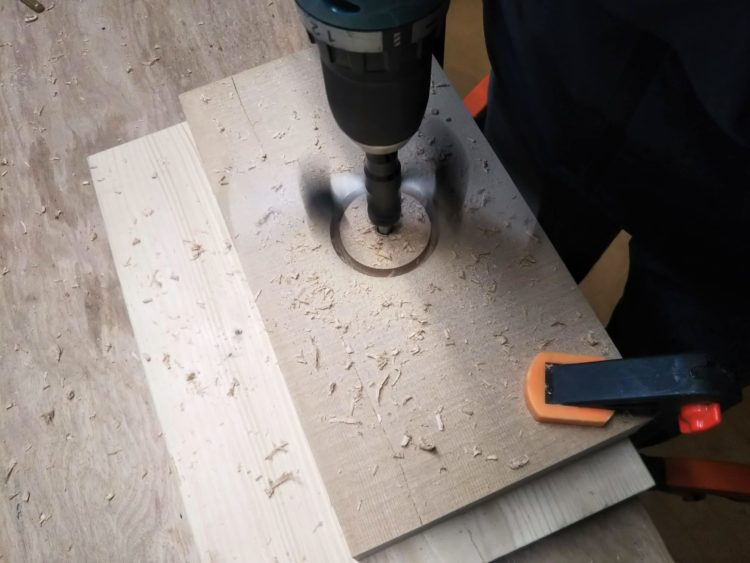
深く切削していく
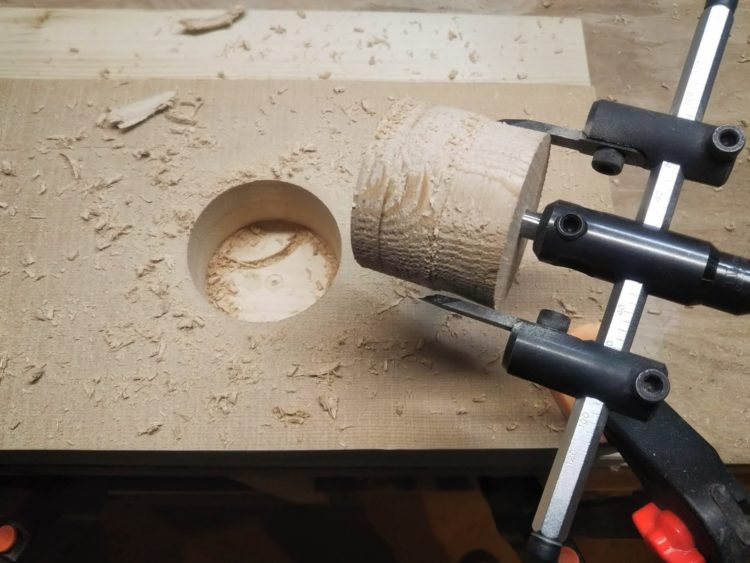
厚板(25mm以上)の穴あけ完了
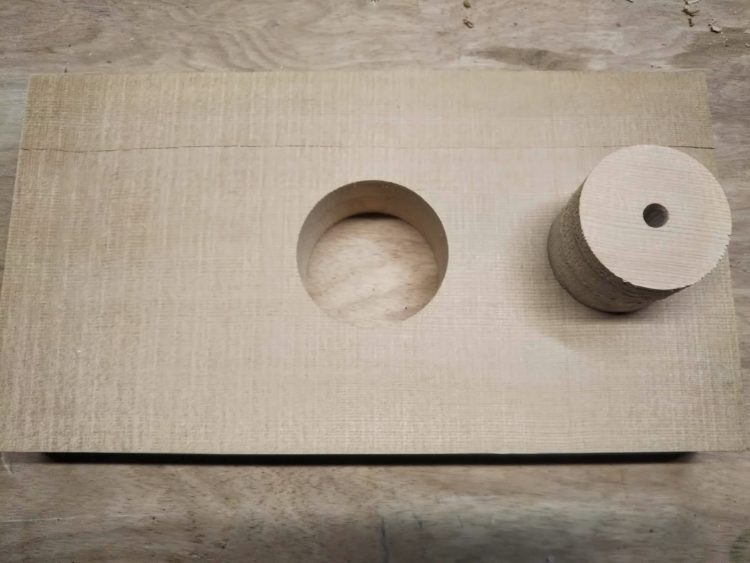
厚板(25mm以上)の穴あけ完了
徐々に深く切削していくと、片面からの溝とつながり、厚板(25mm以上)の穴をくり抜くことが出来ます。
厚板の穴あけの切削抵抗を小さくする方法
厚板用のセンタードリルは先端がネジ形状の為、切削方向への引き込み力が強く、外刃・内刃の切削抵抗が非常に強くなります。
切削抵抗が強いと、ドリルドライバーの操作がうまくいかず、穴をきれいにあけることが難しくなります。
あらかじめ穴のセンター(センタードリルの切削箇所)に下穴をあけておき、センタードリルの引き込み力を無くし、切削抵抗を小さくする方法を説明します。
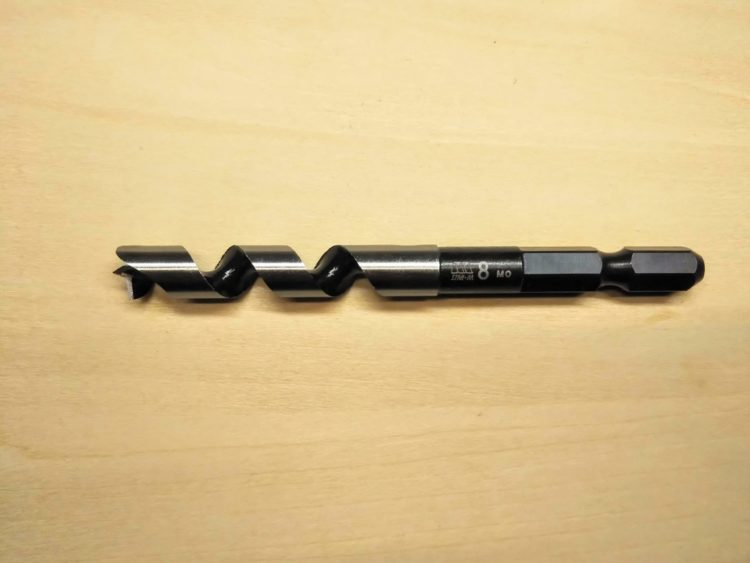
センタードリルと同径のドリルビットを用意
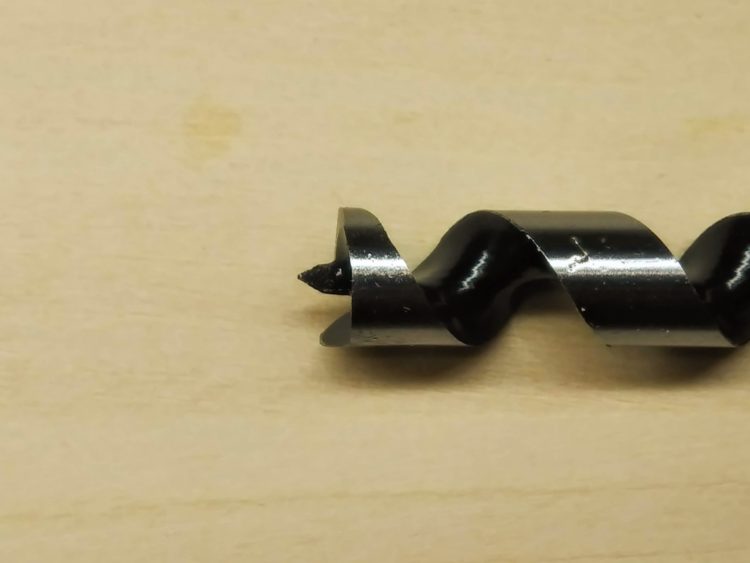
先端が三角錐
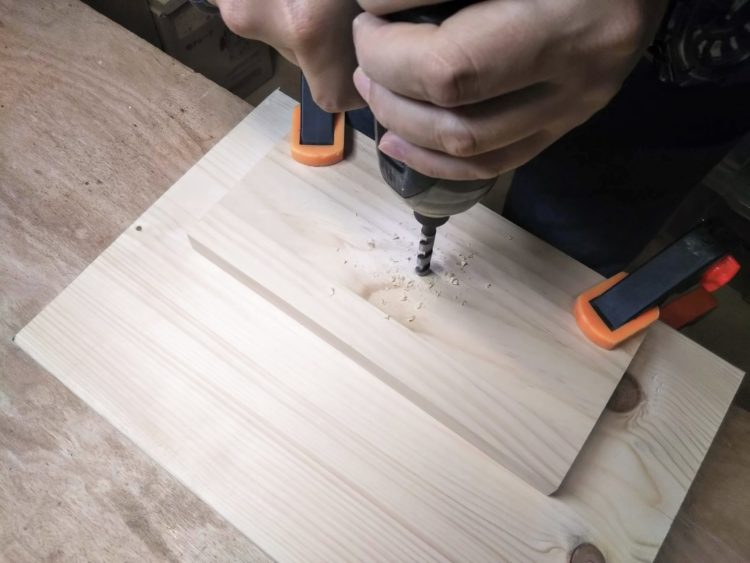
穴のセンターに下穴をあける
センタードリルと同径のドリルビット(先端形状が三角錐)を用意し、穴のセンターに下穴をあけていきます。
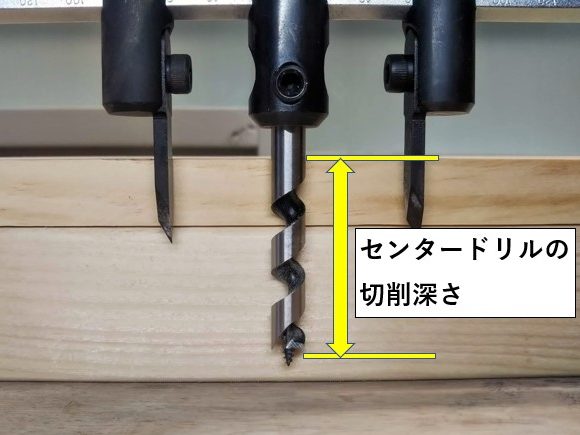
センタードリルの切削深さ
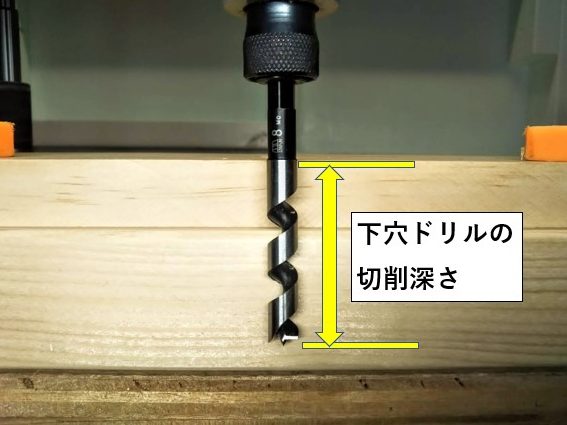
下穴ドリルの切削深さ
穴のセンター(センタードリルの切削箇所)にあける下穴の深さは、センタードリルが切削する深さと同じになります。

穴センターの下穴

下穴にセンタードリルを差し込む
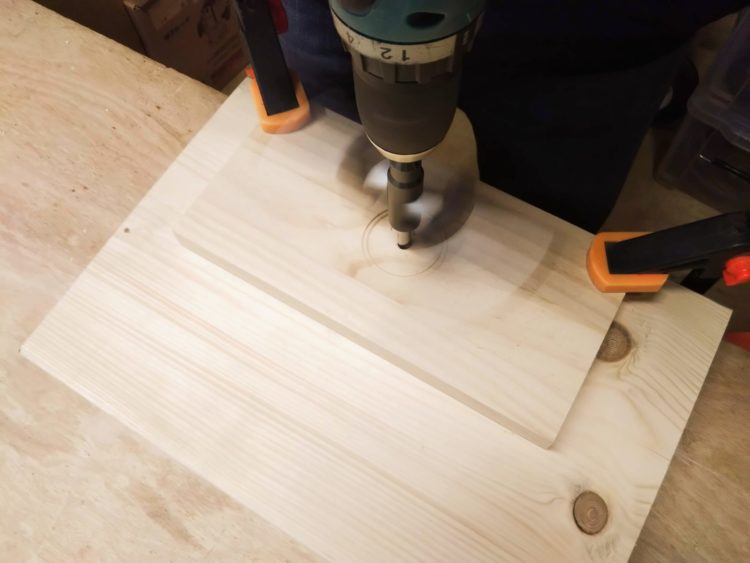
下穴をガイドに切削開始
穴のセンターに下穴をあけたら、自在錐のセンタードリルを下穴に差し込み、切削を開始します。
前述の厚板(25mmまでの板厚)の穴あけ加工と同じ手順で切削していきます。
下穴をあけてある為、センタードリルの引き込み力は無く切削量を調整出来、切削抵抗を小さくする事が可能になります。
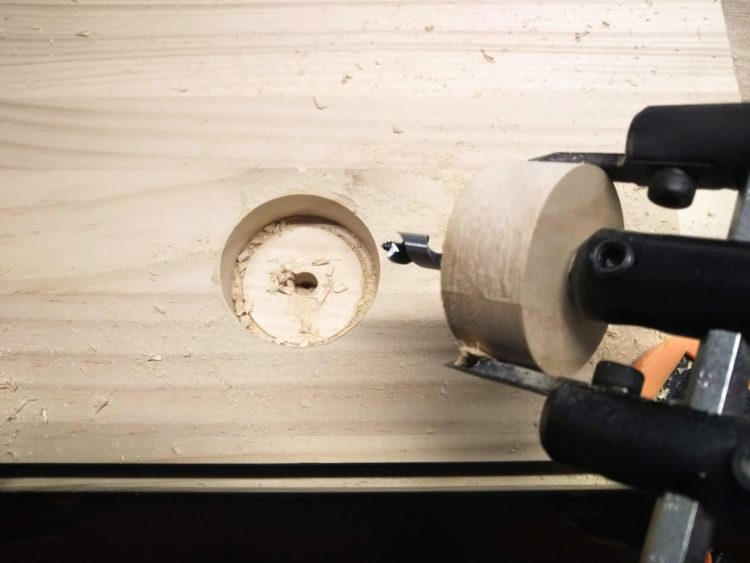
下穴をあけた場合の穴あけ
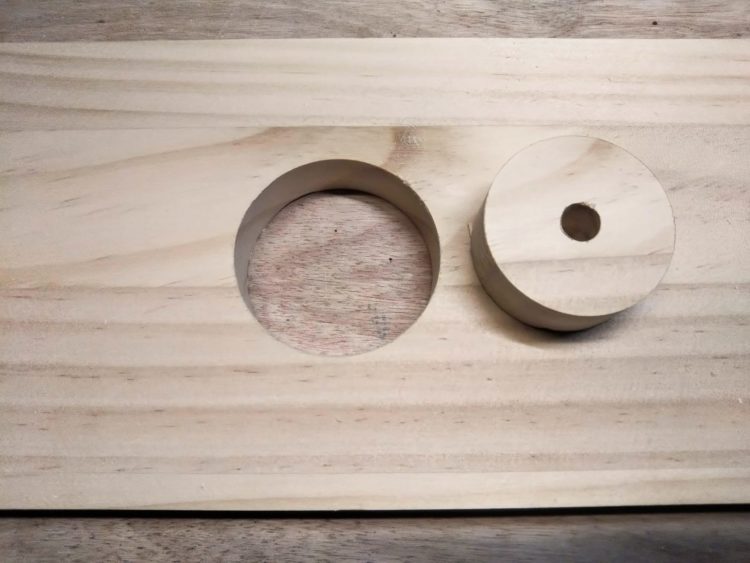
下穴をあけた場合の穴あけ
下穴をあけ切削抵抗を小さくすることで、自在錐の操作性もよくなり、穴をきれいにあける事が出来ます。
まとめ
今回は、自在錐の種類と使い方について説明しました。
自在錐は、一つあるだけで様々な径の穴あけが出来、非常に便利です。
特に大きな径の穴をあける際に大変重宝します。
しかし切削抵抗が強く、使用にはコツが必要です。
今回の記事を参考にしながら、安全に作業しきれいな穴あけ加工を行ってくださいね。